近年、多くの企業や組織が取り組む「リーンマネジメント」。この言葉を耳にしたことがある方も多いでしょう。しかし、実際にはその本質や、日常業務への取り入れ方、さらにはデジタルトランスフォーメーションとの関係性まで、多くの疑問が浮かんでくるかと思います。
この記事では、リーンマネジメントの基本的な考え方から、その実際の適用例、未来の展望に至るまで、徹底的に解説していきます。リーンを業務に導入して、組織の効率や生産性を向上させたい方は、ぜひ最後までご覧ください。
はじめに:リーンマネジメントの基本
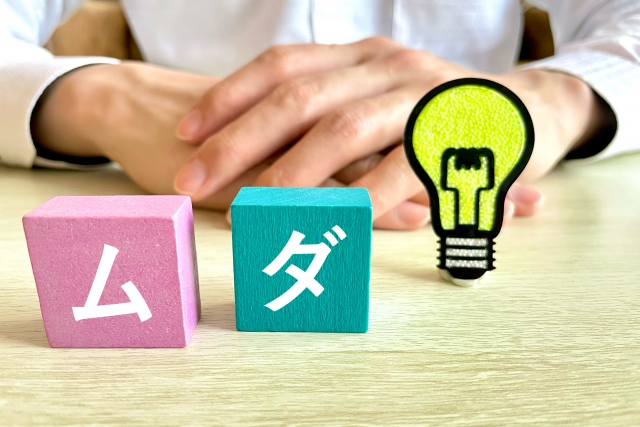
近年、多くのビジネスマンや経営者たちが注目している「リーンマネジメント」。この言葉を耳にしたことはありますか?この記事では、リーンマネジメントの基本から、その背後にある哲学、そしてどのようにして多くの企業がこれを活用しているのかについて解説します。
リーンマネジメントとは、簡潔に言えば「無駄を排除して価値を最大化する経営手法」です。ここでの「無駄」とは、顧客から見て価値がない活動や過程のことを指します。リーンマネジメントの核心は、これらの無駄を特定し、削減または排除することで、製品やサービスの品質を高めながらコストを削減することにあります。
リーンマネジメントの起源:トヨタ生産方式との関連
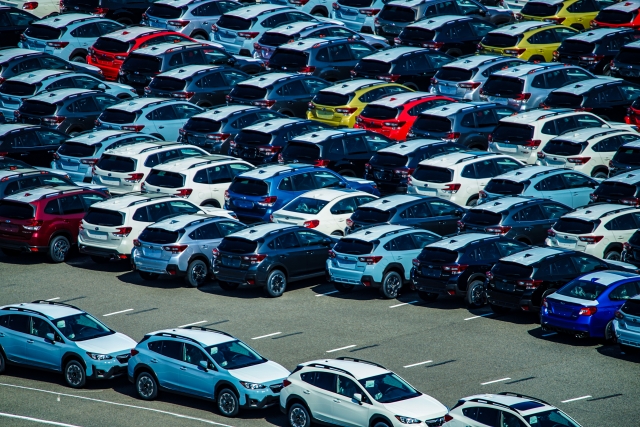
リーンマネジメントのコンセプトが現在の形になったのは、日本の自動車産業、特にトヨタ生産方式(TPS)に起源を持っています。戦後の資源が乏しい中で、トヨタは無駄を極力排除し、効率的な生産を追求する方法を模索しました。
TPSは、在庫を最小限に抑えながら、ジャストインタイム生産を実現する方法として注目されました。この手法は、顧客の要求に応じて、必要な部品を必要な時に提供することで、無駄な在庫や過剰生産を防ぐものです。
リーンマネジメントとトヨタ生産方式は、その核心に「顧客価値の最大化」と「無駄の排除」という共通の哲学を持っています。この成功した生産手法は、後に多くの企業や業界に取り入れられ、現在のリーンマネジメントの原型となりました。
リーンマネジメントの5つの原則
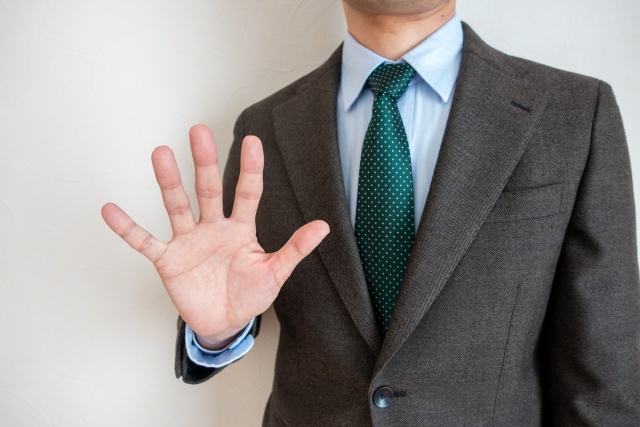
リーンマネジメントの成功は、5つの基本原則に基づいています。これらの原則を理解し実践することで、組織はより効率的かつ顧客中心の業務運営が可能となります。
価値の特定
最初に、顧客が価値と感じるものを明確に定義します。これは、製品やサービスが顧客の問題をどのように解決するかを理解することから始まります。
価値流れのマッピング
次に、製品やサービスが生み出される過程をマッピングします。この過程で無駄なステップを特定し、その削除や改善を行います。
フローの最適化
マッピングした過程を滑らかにし、障害や遅延を取り除くことで、製品やサービスの流れを効率的にします。
プル生産の導入
顧客の要求に基づいて生産する手法。これにより、過剰生産や在庫の無駄が削減されます。
完璧を目指す
リーンは絶えず改善を追求する文化です。完璧を目指して、日々の業務を見直し、改善を継続します。
ムダ(Waste)の7+1の種類とその削減方法
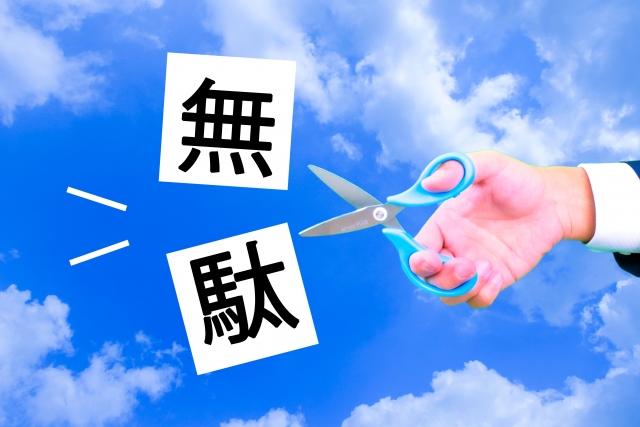
リーンマネジメントでは、業務プロセス中の無駄を特定し削減することが重要です。伝統的なリーンの考え方では、ムダは7つのカテゴリーに分けられますが、近年、さらに1つのカテゴリーが追加されています。
在庫のムダ
不要な在庫はキャッシュフローの圧迫やスペースの無駄につながります。
過剰生産のムダ
需要を超える生産は資源の浪費を招きます。
過剰な加工のムダ
顧客が求めていない機能や品質の向上は無駄です。
運搬のムダ
不要な移動は効率を下げる要因となります。
待ち時間のムダ
生産ラインの遅延や待機は生産性の低下を招きます。
動きのムダ
労働者の不要な動きや歩行も無駄となります。
不良品のムダ
不良品の製造は修正や再製造のコストを引き起こします。
才能のムダ (追加のカテゴリー)
スタッフの能力や才能を十分に活用しないことも無駄とされています。
これらのムダを特定し、適切な改善策を導入することで、リーンマネジメントの真髄を体現することができます。
リーンマネジメントを支えるツールと技法
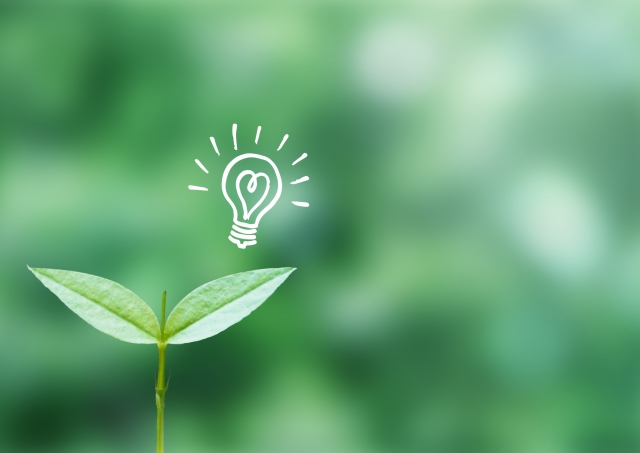
リーンマネジメントの実践においては、具体的なツールや技法が使用されることで、無駄の排除やプロセスの改善が進められます。以下に主要なツールと技法を紹介します。
カンバン
ジャストインタイム生産をサポートするツール。需要に応じた生産を促進し、在庫の無駄を削減します。
5S
仕事場の効率的な組織化を促進する手法。5つの「S」の頭文字(整頓、整理、清掃、清潔、しつけ)に基づき、作業環境を最適化します。
ヒョウカ (標化)
作業の標準化。ベストプラクティスを標準として確立し、業務の品質や効率を一貫して維持します。
これらのツールや技法は、リーンマネジメントの原則を実際の現場で具体化し、継続的な改善を実現するためのものです。
リーン思考とカイゼン:継続的改善の文化
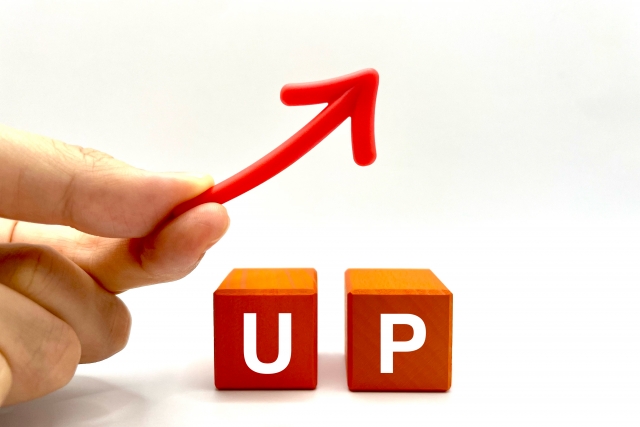
リーン思考は、組織全体が顧客価値を最大化するためのアプローチを持つことを指します。この思考を実践する上で、カイゼンの哲学が不可欠です。
カイゼンは、「改善」を意味する日本語で、小さな改善を継続的に行い、全体としての大きな成果を得るという考え方です。リーンマネジメントにおいて、カイゼンは日々の業務の中で発見される課題や問題点を、全員が参加して改善する文化を築くための基石となります。
リーン思考とカイゼンは、組織が持続的な成長と変革を達成するための心の持ち方や考え方を提供します。これらを取り入れることで、組織は市場の変化に迅速に対応し、競争力を高めることができます。
リーンマネジメントの成功事例
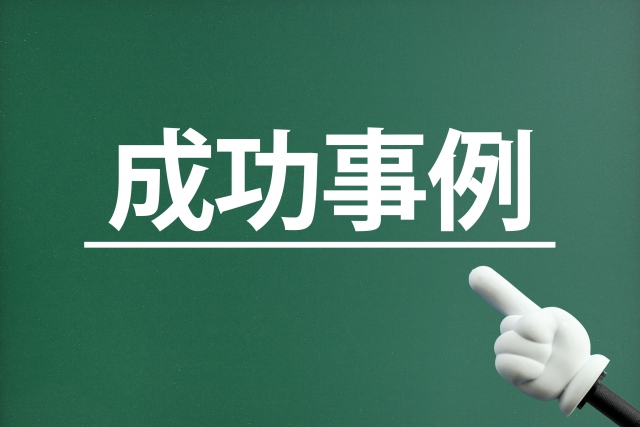
リーンマネジメントが、組織の効率向上やコスト削減にどのように寄与するのか、具体的な成功事例を通して紹介します。
大手自動車メーカー
トヨタは、ジャストインタイム生産やカンバンシステムを導入することで、在庫の無駄を大幅に削減。製品の品質向上と納期の短縮を実現しました。
航空業界のリーダー
ある航空会社は、リーンマネジメントの原則を活用し、整備の作業フローを見直すことで、飛行機の運行遅延を大幅に減少させました。
これらの事例は、業界や規模を問わず、リーンマネジメントの手法がビジネスの効果を高める具体的な証拠となっています。
リーンマネジメント導入時のよくある誤解とチャレンジ
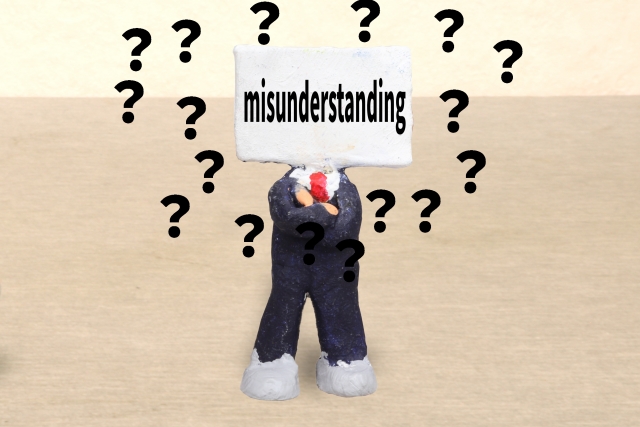
リーンマネジメントの導入は多くの組織で期待される一方、その導入には誤解やチャレンジも存在します。
誤解:リーン=コスト削減
リーンマネジメントは、単にコスト削減の手法ではなく、価値の最大化や顧客満足の向上を目指す哲学です。
チャレンジ:組織文化の変革
リーンを実践するためには、組織文化の変革が不可欠。これには時間と持続的な努力が求められます。
リーンマネジメントを効果的に導入し、その恩恵を受けるためには、これらの誤解を払拭し、チャレンジを正面から受け止めることが必要です。
日本企業と海外企業におけるリーンの違い
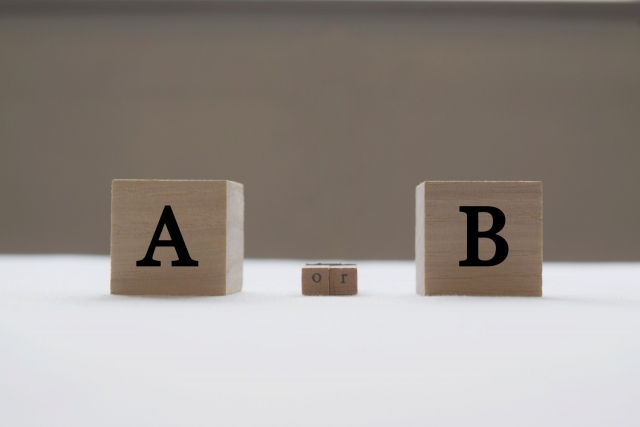
リーンマネジメントは、その起源が日本にある一方で、現在では世界中の多くの企業が取り入れています。しかし、文化や組織の背景によって、その取り組み方には違いが見られます。
日本企業
日本の企業文化には、「一つの課題をチーム全体で解決する」や「長期的な目線での取り組み」などの特徴があり、これがリーンの実践を後押ししています。
海外企業
一方、海外の企業では、短期的な成果を求める文化や、個人の責任と権限が強調されることが多く、これがリーンの取り組みに影響を与えています。
文化や背景の違いを理解することで、より効果的なリーンマネジメントの実践が期待されます。
リーンマネジメントの未来:デジタルトランスフォーメーションとの融合
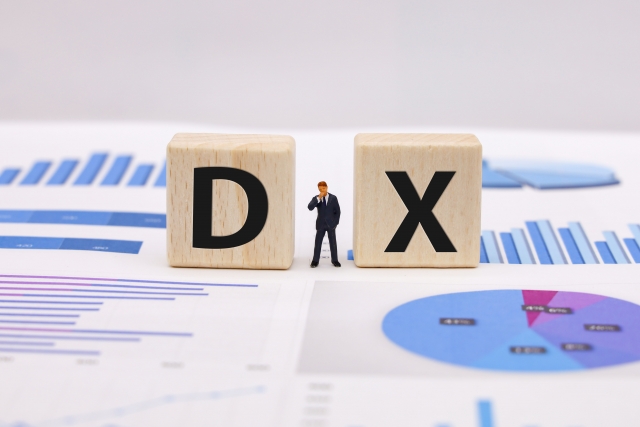
近年、デジタルトランスフォーメーション(DX)が組織の変革のキーワードとして注目されています。このDXとリーンマネジメントの融合は、次世代の生産性向上をリードする可能性があります。
データの活用
リアルタイムのデータ分析を行うことで、ムダの発見やプロセスの最適化が迅速に行えるようになります。
自動化とAI
AI技術を利用して業務を自動化することで、人間が行うべき価値ある業務に注力できるようになります。
デジタル技術とリーンマネジメントの融合は、組織の持続的成長とイノベーションをサポートする強力な組み合わせとなり得ます。
まとめ:リーンマネジメントを日常の業務にどう取り入れるか
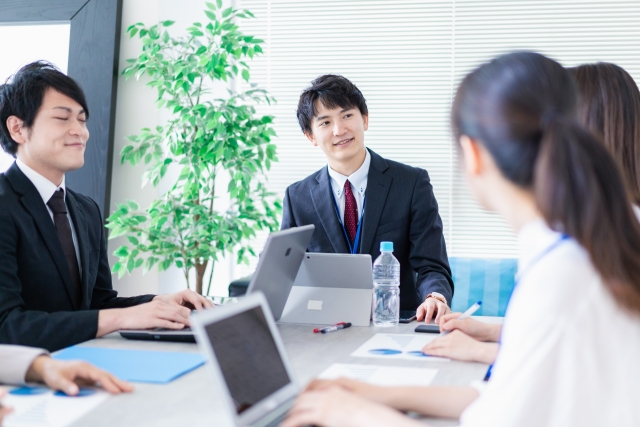
リーンマネジメントの基本原則やツール、成功事例について詳しく見てきました。しかし、最も重要なのは、これらの知識を日常の業務にどのように実践していくかです。
日常の業務を見直す
まず、現在の業務フローを客観的に分析し、ムダや非効率的な部分を見つけ出しましょう。これはリーンマネジメントの第一歩です。
全員参加の文化を育む
リーンは上からの指示だけでなく、現場の声や提案を活かすことが不可欠です。継続的な改善の文化を築くために、全員が参加する環境を作り上げることが大切です。
デジタルツールを活用する
データの収集や分析、業務の自動化など、デジタルツールを利用してリーンマネジメントの取り組みをさらに強化しましょう。
リーンマネジメントは、一度導入すれば終わりというものではありません。組織や市場の変化に合わせて、継続的に取り組むことで、真の効果を実感することができます。日常業務にリーンの考え方を取り入れ、組織の競争力を高めるステップを進めていきましょう。