アッシング装置は、電子デバイス製造における重要な技術であり、その高効率化と持続可能性の追求は業界全体で注目されています。最新の技術動向を把握し、新たな素材やエネルギー効率の最適化に焦点を当てることが求められています。この記事では、アッシング装置の基本原理から現在の市場動向、そして未来の展望までを詳しく解説します。
最新の情報に基づき、この記事を通じて、アッシング装置の技術革新がどのように進んでいるのかを理解し、持続可能な未来を見据えた取り組みを紹介します。
はじめに
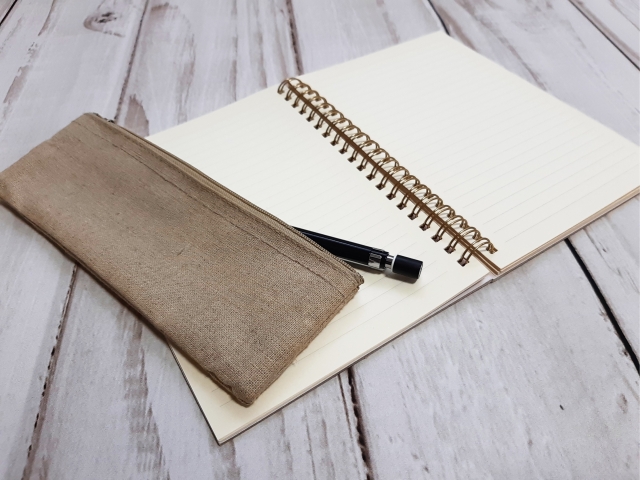
アッシング装置は、半導体や電子デバイス製造のプロセスにおいて欠かせない技術です。主にフォトレジストの除去や表面処理に利用され、高い精度と効率を求められています。近年では、高効率化と持続可能性の向上が大きなテーマとなっており、技術革新が進んでいます。このセクションでは、アッシング装置の基本概念やその重要性について詳しく解説します。
アッシング装置の基本的な役割は、製造プロセス中に発生する不要なフォトレジストや有機物を除去することです。これにより、次の製造ステップで高品質な加工が可能となります。特にプラズマアッシング技術は、従来の化学的手法に比べて環境への負荷が少なく、高い処理精度を持つため、多くの企業で採用されています。アッシング装置の進化は、製造工程の効率化とコスト削減にも大きく寄与しており、持続可能な製造プロセスの構築に不可欠です。
このように、アッシング装置の技術動向を理解することは、製造業に携わるビジネスパーソンにとって重要です。次のセクションでは、現在の市場動向と需要について詳しく見ていきます。
アッシング装置の基本原理
アッシング装置は、主にプラズマ技術を利用してフォトレジストを除去する装置です。プラズマとは、ガスが高エネルギー状態になったもので、イオン化されたガス粒子が含まれます。これらのイオン化された粒子がフォトレジストと反応し、化学的に分解することで除去が行われます。アッシング装置には、ドライアッシングとウェットアッシングの2つの主要な手法がありますが、近年では環境負荷が少ないドライアッシングが主流となっています。
ドライアッシングでは、反応ガスをプラズマ状態にするために高周波電力を利用します。プラズマは反応チャンバー内で生成され、基板上のフォトレジストに対して均一に作用します。この過程で、フォトレジストは化学的に分解されて揮発性のガスとして除去されます。この手法は、高精度かつ均一な処理が可能であり、微細なパターン形成が求められる現代の半導体製造において非常に有効です。
アッシング装置の基本原理を理解することで、その技術的なメリットや適用範囲をより深く知ることができます。次に、現在の市場動向と需要について掘り下げていきます。
現在の市場動向と需要
アッシング装置の市場は、半導体産業の成長とともに急速に拡大しています。特に5G技術の普及やIoTデバイスの増加により、半導体需要が高まっており、それに伴いアッシング装置の需要も増加しています。市場調査によると、アッシング装置の世界市場は今後数年間でさらに成長する見込みです。
市場動向としては、高効率かつ環境負荷の少ない技術へのシフトが顕著です。特に先進的なプラズマアッシング技術は、低消費電力と高精度処理を両立しており、多くの企業で採用が進んでいます。また、装置自体のコンパクト化やモジュール化が進んでおり、製造ラインの柔軟性を高める取り組みが行われています。これにより、生産性の向上とコスト削減が実現されています。
一方で、環境規制の強化も市場に影響を与えています。各国で環境保護の意識が高まる中、アッシング装置も環境に配慮した設計が求められています。例えば、排ガス処理技術の向上や再利用可能な材料の使用が進んでいます。このような技術革新により、持続可能な製造プロセスの構築が目指されています。
高効率アッシング技術の進展
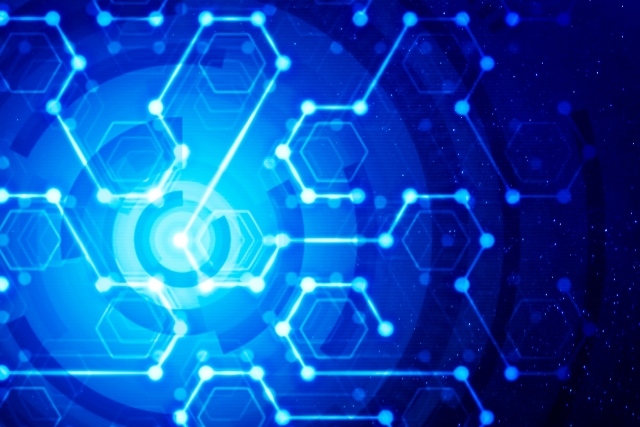
アッシング装置の高効率化は、半導体製造プロセスの生産性向上とコスト削減に直結します。最新のアッシング技術は、プラズマの制御性を向上させることで、より均一で迅速なフォトレジスト除去を実現しています。これにより、製造ラインのスループットが向上し、全体の生産効率が大幅にアップしています。
一例として、高周波電力の最適化により、プラズマの生成効率が向上しています。これにより、同じエネルギー消費でより高い処理能力を発揮することが可能となり、エネルギーコストの削減にも寄与しています。また、反応ガスの選定と流量制御の精度向上により、プロセスの再現性が高まり、不良率の低減も実現しています。
さらに、最新のアッシング装置ではAIを活用したプロセス制御が導入されつつあります。AI技術により、リアルタイムでプロセスパラメータを最適化し、常に最適な処理条件を維持することが可能です。これにより、製造の安定性と品質が飛躍的に向上しています。また、プロセスデータの蓄積と分析により、さらなる技術改善のフィードバックループが形成されます。
高効率アッシング技術の進展は、今後の半導体製造の競争力強化に不可欠です。次のセクションでは、持続可能性に向けた取り組みについて詳しく解説します。
持続可能性に向けた取り組み
アッシング装置の持続可能性は、環境保護と企業の社会的責任の観点から非常に重要です。近年、多くの企業が持続可能な製造プロセスの構築に向けて積極的に取り組んでいます。具体的な取り組みとしては、排ガス処理技術の向上やリサイクル可能な材料の使用が挙げられます。排ガス処理技術の進展により、装置から排出される有害物質の削減が可能となり、環境への負荷が軽減されています。
また、エネルギー効率の改善も持続可能性の重要な要素です。最新のアッシング装置では、消費電力を抑えつつ高効率な処理が可能となるよう設計されています。これにより、製造プロセス全体のエネルギー使用量が削減され、カーボンフットプリントの低減が図られています。さらに、再生可能エネルギーの導入も進められており、企業全体の持続可能性向上に貢献しています。
一方で、持続可能な材料の開発も進んでいます。特に、再利用可能な化学薬品や環境に優しいプラズマガスの研究が進んでおり、これらの材料を用いることで環境負荷の低減が期待されています。これらの取り組みは、企業の社会的責任を果たすだけでなく、長期的なコスト削減にもつながります。
新素材の利用とその効果
アッシング装置における新素材の利用は、処理効率と製品品質の向上に大きく貢献しています。新素材の開発と導入により、アッシングプロセスの最適化が進み、微細加工技術がさらに高度化されています。特に、低温アッシングが可能な素材や、反応性が高く環境負荷の少ないガスが注目されています。
低温アッシング素材の導入により、温度に敏感なデバイスの加工が可能となり、歩留まりの向上が実現されています。従来の高温プロセスでは処理が難しかったデバイスでも、低温アッシングにより高精度な加工が可能です。また、反応性の高いガスを用いることで、アッシング効率が大幅に向上し、処理時間の短縮が図られています。
さらに、環境負荷の少ない新素材の開発も進んでいます。例えば、温室効果ガスの排出を抑える新しいプラズマガスや、再生可能な有機材料が研究されています。これにより、製造プロセス全体の持続可能性が向上し、環境への配慮が一層進んでいます。新素材の利用は、技術革新と環境保護の両立を実現するための重要なステップです。
先進的なプラズマアッシング技術
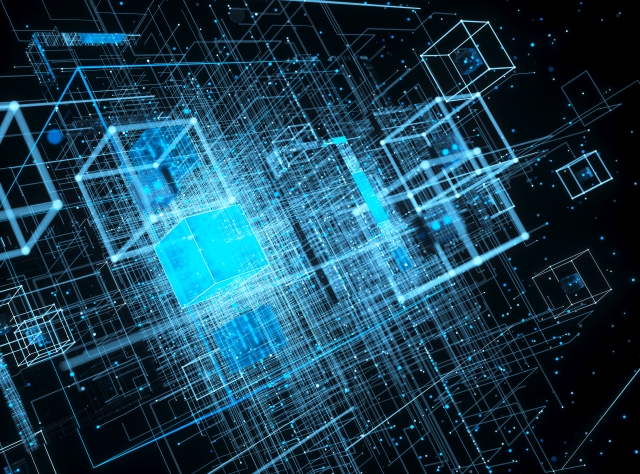
先進的なプラズマアッシング技術は、アッシングプロセスの効率と精度を飛躍的に向上させるために重要です。プラズマアッシングは、ガスを高エネルギー状態にし、イオン化させたプラズマを用いてフォトレジストを除去する技術です。従来の化学的手法に比べて環境負荷が少なく、高精度な処理が可能であるため、多くの企業で採用されています。
最新のプラズマアッシング技術では、プラズマの生成と制御において高度な技術が導入されています。例えば、マイクロ波を用いたプラズマ生成技術は、より均一で安定したプラズマを提供し、高精度なアッシングを可能にします。これにより、微細なパターン形成や高密度配線の加工が容易となり、製品品質が向上しています。
また、プラズマの制御技術も進化しており、リアルタイムでプラズマの状態をモニタリングし、最適な条件での処理を維持することができます。これにより、プロセスの再現性が高まり、不良率の低減が実現されています。先進的なプラズマアッシング技術は、製造プロセスの効率化と高品質化を同時に達成するための重要な技術です。
エネルギー効率の最適化
エネルギー効率の最適化は、アッシング装置の運用コスト削減と持続可能性向上のために欠かせない要素です。最新のアッシング装置では、エネルギー消費を最小限に抑えつつ、高効率な処理を実現するためのさまざまな工夫が施されています。これにより、全体のエネルギー使用量が削減され、環境負荷の低減が図られています。
一例として、高周波電力の最適化があります。高周波電力を効率的に利用することで、プラズマの生成効率が向上し、同じエネルギーでより多くの処理が可能となります。また、反応ガスの選定と流量制御の精度向上により、プロセスの効率がさらに高まります。これにより、アッシングプロセス全体のエネルギー効率が向上し、運用コストの削減にもつながります。
さらに、エネルギー回収システムの導入も進んでいます。アッシングプロセスで発生する熱エネルギーを再利用することで、エネルギーの無駄を減らし、全体の効率を高めることができます。例えば、廃熱を他のプロセスに利用することで、全体のエネルギー消費を削減し、持続可能な製造プロセスの構築が可能となります。エネルギー効率の最適化は、企業の競争力強化と環境保護の両立を実現するための鍵となります。
事例研究: 成功した導入例
アッシング装置の導入に成功した企業の事例は、多くのビジネスパーソンにとって参考になります。ある半導体メーカーは、最新のプラズマアッシング技術を導入することで、生産性と品質の両方を大幅に向上させました。この企業は、従来の装置に比べてエネルギー効率が高く、処理速度も速い新型装置を採用し、製造コストの削減と環境負荷の低減を同時に実現しました。
具体的には、新しいアッシング装置を導入することで、フォトレジスト除去のプロセスが大幅に効率化されました。これにより、製品一つあたりの処理時間が短縮され、年間を通じて生産量が約20%増加しました。さらに、最新の装置は排ガス処理システムを備えており、有害物質の排出が大幅に削減され、環境規制にも適合しました。この結果、企業の環境評価も向上し、持続可能な経営を実現しています。
また、他の事例としては、AI制御を導入したアッシング装置を利用している企業があります。この企業では、リアルタイムでプロセスパラメータを最適化することで、常に最適な処理条件を維持し、高品質な製品を安定して供給しています。AI技術により、プロセスのばらつきが減少し、歩留まりの向上が実現されています。
今後の展望と課題
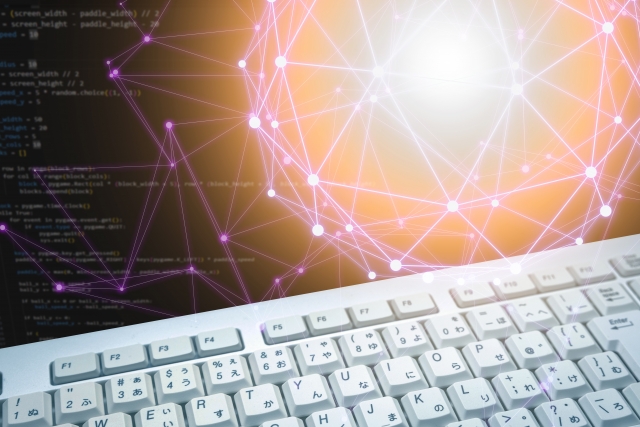
アッシング装置の技術は日々進化しており、今後もさらなる発展が期待されています。特に、ナノスケールの加工技術や高効率・低エネルギー消費のプロセスが求められています。これらの技術革新により、半導体製造のさらなる微細化と高性能化が進むと考えられています。
一方で、技術的な課題も残っています。例えば、高度なプラズマ制御技術の開発には多大なコストと時間が必要です。また、新素材の導入には、その素材に適した新しいプロセスの開発が不可欠です。これらの課題を克服するためには、企業間の協力や研究開発投資の増加が必要です。
また、持続可能性に関する規制の強化も課題となっています。環境に配慮した製造プロセスの構築は必須ですが、そのためには技術革新だけでなく、全体のサプライチェーンの見直しやエネルギー使用の最適化が求められます。さらに、グローバル市場での競争力を維持するためには、常に最新の技術動向を把握し、迅速に対応することが重要です。
規制と標準化の動向
アッシング装置に関連する規制と標準化の動向は、製造業に大きな影響を与えます。近年、環境保護やエネルギー効率に関する規制が強化されており、企業はこれに対応するための取り組みを進めています。特に、排出ガスの管理や使用する材料の環境影響を最小限に抑えるための規制が厳しくなっています。
国際標準化機構(ISO)や各国の環境庁などが制定する規制に基づき、アッシング装置の設計や運用が見直されています。例えば、ISO 14001などの環境マネジメントシステムの認証取得が進められています。これにより、企業は環境負荷を低減し、持続可能な製造プロセスを構築することが求められています。
さらに、標準化の動向としては、装置の互換性やプロセスの統一化が重要なテーマとなっています。これにより、異なるメーカーの装置間でのデータ交換や操作性の向上が図られ、製造プロセスの効率化が進んでいます。また、標準化されたプロセスにより、品質のばらつきを減少させることが可能となり、製品の信頼性が向上します。
まとめ
アッシング装置の技術動向は、製造業界における高効率と持続可能性の追求において重要な役割を果たしています。最新技術の導入により、生産性の向上や環境負荷の低減が実現されています。企業はこれらの技術を積極的に採用し、持続可能な製造プロセスの構築を目指しています。アッシング装置の進化は、今後も半導体製造の未来を支える重要な要素となるでしょう。