ワイヤーボンディング技術は、半導体製造プロセスにおいて不可欠な要素です。特に自動化技術の導入により、その精度と効率が飛躍的に向上しています。この記事では、自動化技術がワイヤーボンディングにもたらす革命的な進化について詳しく解説します。
ワイヤーボンディングとは
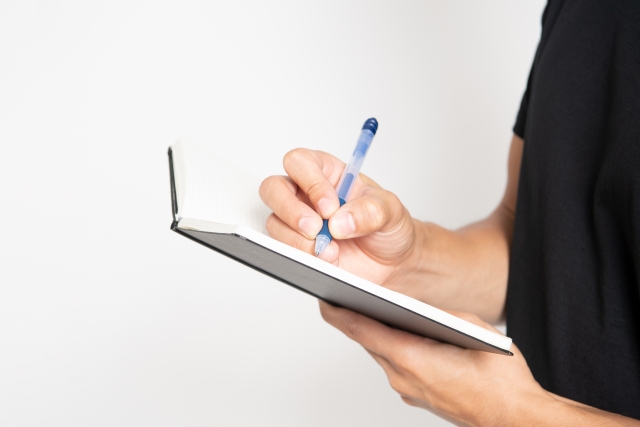
ワイヤーボンディングは、半導体製造プロセスにおいてチップと外部回路を電気的に接続するための技術です。この技術は、非常に微細な金属ワイヤーを用いて接続を行うため、高度な精度とクリーンな作業環境が求められます。半導体業界では、信頼性の高い接続方法として広く利用されており、特にスマートフォンやコンピュータ、車載電子機器などの高性能デバイスの製造において欠かせない技術です。
ワイヤーボンディングには、主にボールボンディングとウェッジボンディングの2種類があります。ボールボンディングは、金ワイヤーを溶かしてボールを形成し、チップとパッドに接続します。一方、ウェッジボンディングは、ワイヤーを圧着して接続する方法で、アルミニウムワイヤーが主に使用されます。これらの方法は、製品の用途や要求される性能に応じて選択されます。
半導体製造におけるワイヤーボンディングの重要性は、その高い信頼性とコスト効率にあります。従来の手動プロセスに比べて、自動化されたワイヤーボンディングマシンは生産性を大幅に向上させると同時に、接続の一貫性と品質を保証します。このため、半導体メーカーは競争力を維持するために、自動化技術の導入を積極的に進めています。
自動化技術の導入背景
ワイヤーボンディングの自動化技術の導入は、半導体製造業界における効率化と品質向上を目的としています。従来の手動プロセスでは、熟練した技術者が必要とされ、多くの時間とコストがかかる上に、人的ミスのリスクも存在します。これに対して、自動化されたワイヤーボンディングシステムは、プロセスの一貫性と精度を高め、製造コストの削減と生産性の向上を実現します。
自動化技術の導入により、ワイヤーボンディングのプロセスは高速化され、大量生産が可能となりました。特に、スマートフォンやタブレット、パソコンなどのエレクトロニクス製品の需要が急増する中で、自動化は不可欠な要素となっています。さらに、自動化されたシステムは、24時間体制で稼働できるため、生産能力の大幅な向上が期待できます。
また、自動化技術の進化により、最新のワイヤーボンディングマシンには高度なセンサー技術やコンピュータビジョンが搭載されています。これにより、微細な接続不良をリアルタイムで検出し、品質管理が徹底されています。これらの技術は、製品の信頼性を高め、エンドユーザーに高品質な製品を提供するために不可欠です。
高度なコンピュータビジョンシステム
自動化されたワイヤーボンディングシステムには、最新のコンピュータビジョンシステムが導入されています。コンピュータビジョンシステムは、カメラやセンサーを使用して、接続部の微細な部分をリアルタイムで監視し、精密な制御を行う技術です。この技術により、ワイヤーボンディングプロセスの精度が飛躍的に向上し、不良率の低減が実現しています。
具体的には、コンピュータビジョンシステムは、ワイヤーの位置や接続の状態を高解像度の画像で捉え、微細なズレや不具合を検出します。検出されたデータは、即座にシステムにフィードバックされ、必要に応じて修正が行われます。このプロセスは、従来の手動検査では見逃されがちな微小な不良を検出する能力を持ち、製品の品質を向上させる重要な役割を果たします。
さらに、コンピュータビジョンシステムは、機械学習と組み合わせることで、より高度な欠陥検出と予測保守が可能となります。過去のデータを分析し、将来の不具合発生のリスクを予測することで、計画的なメンテナンスを行い、システムの稼働時間を最大化します。このように、コンピュータビジョンシステムは、ワイヤーボンディングプロセスの信頼性と効率を大幅に向上させる技術です。
機械学習による欠陥制御
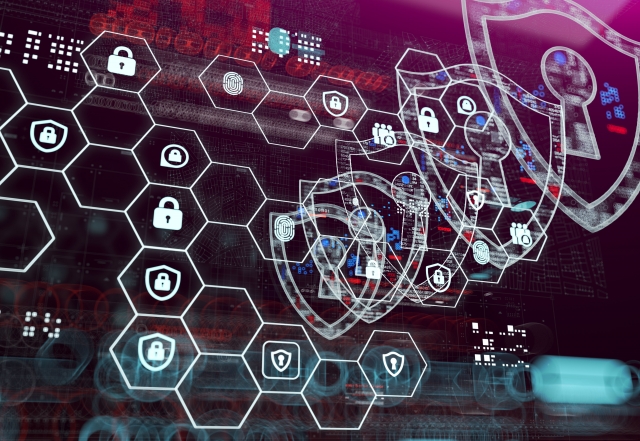
機械学習は、ワイヤーボンディングプロセスの欠陥制御において重要な役割を果たしています。機械学習アルゴリズムは、大量のデータを解析し、接続不良やその他の問題を自動的に検出し、修正する能力を持っています。この技術により、ワイヤーボンディングプロセスの精度と効率がさらに向上し、製品の品質を確保することができます。
機械学習による欠陥制御は、過去のデータを基にモデルを構築し、リアルタイムでの監視とフィードバックを行います。これにより、異常なパターンや微細な変化を早期に検出し、プロセスを調整することで、不良品の発生を最小限に抑えることが可能です。また、機械学習は、異常の原因を特定し、プロセスの最適化を支援するための洞察を提供します。
さらに、機械学習は予測保守の分野でも活用されています。ワイヤーボンディングマシンのパフォーマンスデータを分析し、故障の予兆を検出することで、計画的なメンテナンスを実施し、ダウンタイムを削減します。このように、機械学習は、ワイヤーボンディングプロセスの信頼性を高め、製造効率を最大化するための強力なツールです。
自動化技術の最新動向
ワイヤーボンディングの自動化技術は急速に進化し続けています。特に、最新のワイヤーボンディングマシンには高度な人工知能(AI)と機械学習技術が統合されており、プロセスの最適化と効率化が図られています。これにより、以前では考えられなかったレベルの精度と速度が実現され、製造コストの削減と生産性の向上が可能となっています。
最新の自動化技術には、リアルタイムでのプロセス監視とフィードバック機能が組み込まれています。例えば、センサーやカメラを用いて、ワイヤーの張力や接続の状態を常時監視し、異常を即座に検知します。この情報は、AIアルゴリズムにより解析され、必要に応じてプロセスを自動的に調整します。このように、従来の手動プロセスでは実現不可能だった高度な制御が可能となり、製品の品質向上が期待されます。
さらに、インダストリー4.0の理念に基づいたデジタルツイン技術も導入されつつあります。デジタルツインは、物理的なワイヤーボンディングマシンの仮想モデルを作成し、リアルタイムでデータを反映させる技術です。これにより、プロセスのシミュレーションや予測保守が可能となり、メンテナンスコストの削減と稼働率の向上が実現されます。このような最新技術の導入により、ワイヤーボンディングの自動化はますます進化し続けています。
フリップチップパッケージングとの比較
ワイヤーボンディングと並び称される技術にフリップチップパッケージングがあります。フリップチップパッケージングは、チップの接続面を基板に直接接続する方法であり、ワイヤーボンディングに比べていくつかの利点を持ちます。特に、熱と電気の性能が向上するため、高性能なエレクトロニクス製品において採用されています。
一方で、フリップチップパッケージングは製造コストが高く、製造プロセスも複雑です。このため、コストパフォーマンスを重視する場合や、大量生産を行う場合には、依然としてワイヤーボンディングが選ばれることが多いです。特に、スマートフォンやタブレットなどの大量生産が求められる製品においては、ワイヤーボンディングのコスト効率の高さが強みとなります。
また、ワイヤーボンディングは、微細な接続が可能であり、様々なデバイス形状に対応できる柔軟性を持っています。これに対して、フリップチップパッケージングは、基板設計の自由度が制限される場合があります。このように、両者はそれぞれ異なる特性を持ち、用途や要求される性能に応じて選択されることになります。製品開発の初期段階で、適切な接続技術を選定することが、製品の性能とコストに大きな影響を与えます。
高度な精度を実現する技術
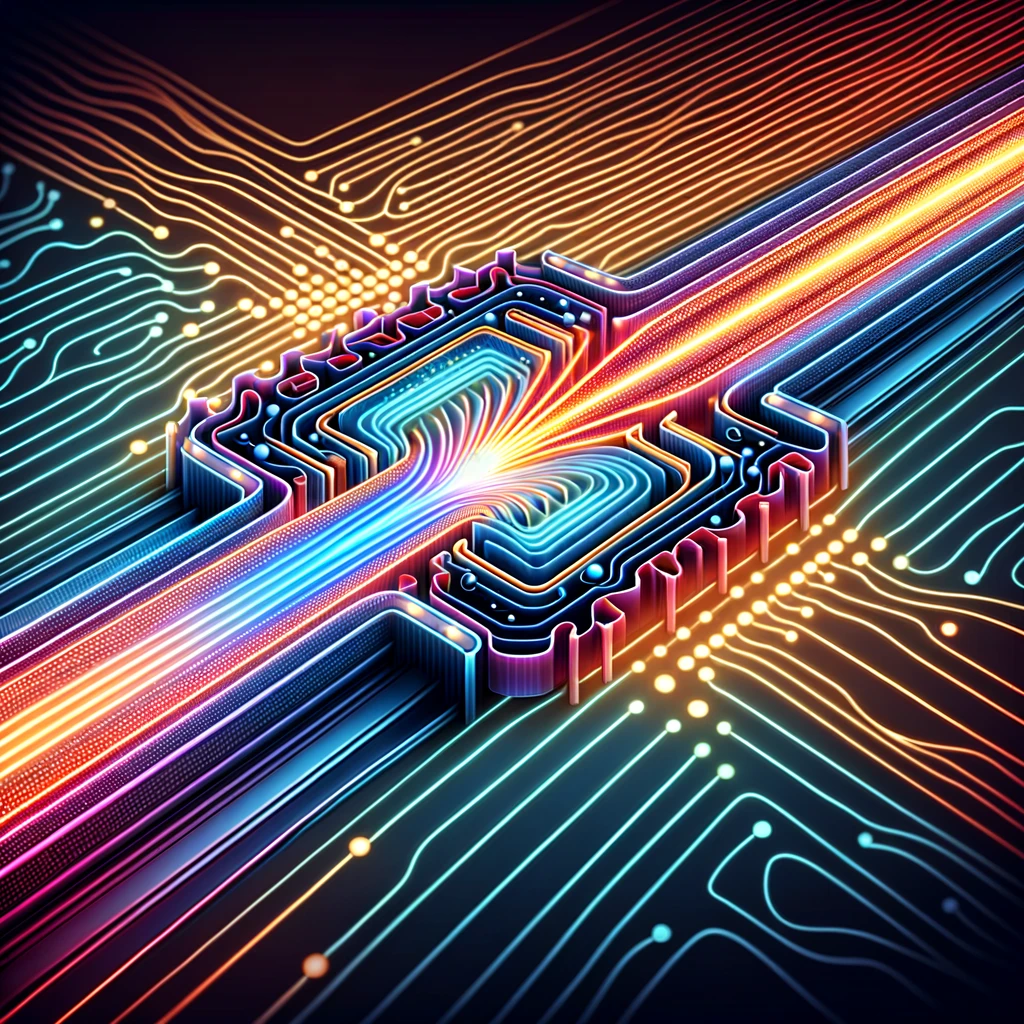
ワイヤーボンディングにおいて高度な精度を実現するための技術革新が進んでいます。特に、自動化されたワイヤーボンディングマシンには、高精度なモーションコントロールシステムが搭載されています。このシステムは、微小な動作を精密に制御し、ワイヤーの位置決めや接続の精度を飛躍的に向上させます。
具体的には、リニアモーターやピエゾエレクトリックアクチュエーターなどの高度なアクチュエーターが使用されており、ナノメートル単位の制御が可能です。これにより、微細な接続部分の位置ずれや不良を最小限に抑え、高品質な接続が実現されます。また、これらのアクチュエーターは、高速な動作が可能であり、生産性の向上にも寄与します。
さらに、レーザー測定技術や光学センサーを活用した位置検出システムも導入されています。これにより、接続部分の寸法や形状をリアルタイムで測定し、プロセスのフィードバック制御を行います。これらの技術は、従来の手動プロセスでは達成できなかった高い精度と一貫性を提供し、製品の品質向上に貢献しています。ワイヤーボンディングの未来は、これらの高度な技術により、さらなる進化を遂げることが期待されます。
インダストリー4.0とワイヤーボンディング
インダストリー4.0の理念は、製造業全体に革命をもたらしつつあり、ワイヤーボンディング分野でもその影響が顕著です。インダストリー4.0は、サイバーフィジカルシステム(CPS)を基盤とし、IoT(モノのインターネット)やビッグデータ解析、AI技術を駆使して、スマートファクトリーの実現を目指しています。この理念に基づき、ワイヤーボンディングプロセスも高度に自動化され、効率と品質が劇的に向上しています。
具体的には、ワイヤーボンディングマシンがネットワークに接続され、リアルタイムでデータの収集と分析が行われます。これにより、プロセスの最適化や予防保守が可能となり、ダウンタイムの削減と稼働率の向上が実現されます。さらに、ビッグデータ解析により、製造プロセス全体のトレンドやパターンを把握し、継続的な改善を行うことができます。
インダストリー4.0の導入は、サプライチェーン全体にも大きな影響を与えます。リアルタイムでの情報共有により、原材料の調達から製品の出荷までのプロセスがシームレスに連携し、効率化が図られます。これにより、製造コストの削減と納期の短縮が実現され、顧客満足度の向上につながります。インダストリー4.0の革新技術は、ワイヤーボンディングを含む半導体製造プロセス全体において、今後ますます重要な役割を果たしていくことでしょう。
市場の成長予測
ワイヤーボンディング市場は今後も成長が見込まれています。2023年から2030年にかけて、市場は年平均成長率(CAGR)9.8%で拡大し、最終的には16億2470万ドルに達すると予測されています。この成長は、エレクトロニクス製品の需要増加と新技術の導入によるものです。特に、自動車、通信、コンシューマーエレクトロニクスの各分野における需要の高まりが市場を牽引しています。
この市場成長には、ワイヤーボンディング技術の進化も大きく寄与しています。例えば、高精度な接続を実現する新しい材料やプロセス技術の開発が進んでおり、これにより製品の性能と信頼性が向上しています。さらに、低コストで高性能なワイヤーボンディングマシンの普及も、市場拡大の一因となっています。これにより、小規模な製造業者も最新技術を導入しやすくなり、競争力を強化することが可能です。
また、地域別の市場動向を見ると、アジア太平洋地域が最も高い成長率を示しています。この地域は、エレクトロニクス製造の中心地としての地位を確立しており、多くの主要メーカーが拠点を構えています。特に、中国、韓国、日本の市場が活発であり、これらの国々が市場全体を牽引しています。これに対して、北米や欧州も堅調な成長を続けており、技術革新と高付加価値製品の開発に注力しています。
技術革新の影響
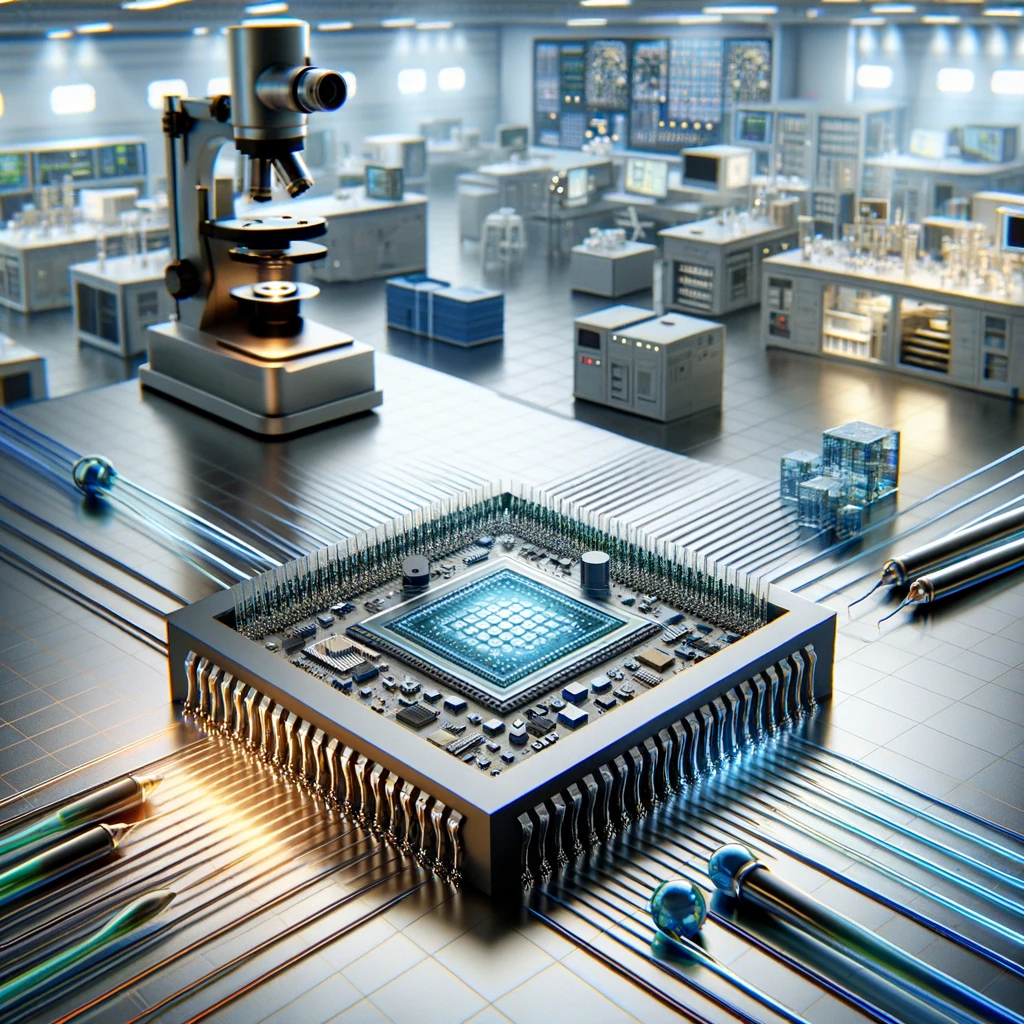
ワイヤーボンディング技術の革新は、製造プロセスに大きな影響を与えています。新しい材料やプロセス技術の導入により、接続の信頼性と効率が大幅に向上しています。例えば、銅ワイヤーの採用が進んでおり、これにより接続の強度と耐久性が向上しました。銅はコストパフォーマンスに優れ、高温環境でも安定した性能を発揮するため、広範なアプリケーションで利用されています。
また、先端的なマシンビジョンとAI技術の統合により、プロセスの自動化と最適化が進んでいます。これにより、製造の一貫性が向上し、不良品の発生率が低減されます。AIは大量のデータを解析し、リアルタイムでプロセスの改善点を見つけ出すことができます。これにより、効率的な生産が可能となり、製造コストの削減にも寄与します。
さらに、3Dパッケージング技術の進展もワイヤーボンディングの革新を促進しています。3Dパッケージングは、複数の半導体チップを垂直に積層し、ワイヤーボンディングを用いて接続する技術です。この技術により、デバイスの小型化と高性能化が実現され、次世代のエレクトロニクス製品に不可欠な要素となっています。これらの技術革新は、ワイヤーボンディングの未来を大きく切り開く鍵となるでしょう。
コストと効率のバランス
ワイヤーボンディングプロセスにおけるコストと効率のバランスは、製造業者にとって重要な課題です。最新の自動化技術を導入することで、プロセスの効率化が図られ、コスト削減が実現されています。特に、高度なAIとマシンビジョン技術の統合により、リアルタイムでのプロセス最適化が可能となり、製造コストを大幅に削減できます。
自動化されたワイヤーボンディングマシンは、24時間稼働が可能であり、人手による作業よりもはるかに高い生産性を誇ります。これにより、大量生産が求められるエレクトロニクス製品の製造において、効率的な生産が可能となります。また、精密な制御が可能なため、品質の一貫性が保たれ、不良品の発生を最小限に抑えることができます。
一方で、最新の自動化技術を導入するための初期投資は高額になることが多いです。しかし、この初期投資は長期的なコスト削減と効率向上に繋がるため、多くの企業が積極的に導入を進めています。特に、競争の激しいエレクトロニクス業界では、効率化とコスト削減が競争力を維持するための重要な要素となっています。
さらに、ワイヤーボンディングプロセスの最適化は、持続可能な製造にも寄与します。エネルギー消費の削減や廃棄物の最小化など、環境への配慮が求められる中で、効率的なプロセスは環境負荷の軽減にも貢献します。これにより、企業は持続可能な成長を実現しつつ、コストと効率のバランスを取ることが可能となります。
まとめ
ワイヤーボンディング技術の進化は、半導体製造業界に大きな影響を与え続けています。自動化技術の導入により、プロセスの効率化とコスト削減が実現され、製品の品質が向上しています。特に、AIやマシンビジョン技術の進化により、リアルタイムでのプロセス最適化が可能となり、製造の一貫性が保たれています。
また、新しい材料や3Dパッケージング技術の導入により、ワイヤーボンディングの性能と信頼性がさらに向上しています。これにより、エレクトロニクス製品の小型化と高性能化が実現され、次世代の製品開発において重要な役割を果たしています。ワイヤーボンディング技術の未来は、これらの革新によってますます明るいものとなるでしょう。
さらに、インダストリー4.0の理念に基づいたデジタルツイン技術やビッグデータ解析の導入により、製造プロセス全体の効率化が進んでいます。これにより、サプライチェーン全体がシームレスに連携し、製造コストの削減と納期の短縮が実現されています。ワイヤーボンディング技術の進化は、今後も半導体製造業界において重要な役割を果たし続けることでしょう。