ワイヤーボンディング技術は、半導体実装の分野で長年にわたり重要な役割を果たしてきました。その技術は絶え間ない進化を遂げており、現在ではフリップチップ実装を凌駕するとも言われています。今回は、ワイヤーボンディング技術の基本から最新の進化までを詳しく解説します。
ワイヤーボンディング技術の基本概要
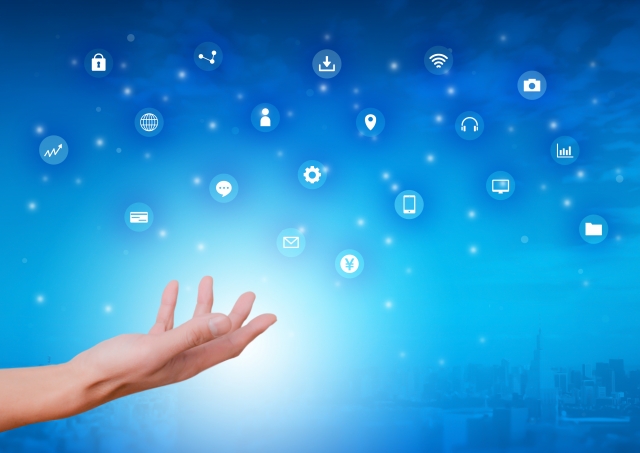
ワイヤーボンディング技術は、半導体デバイスの接続方法として最も広く使用されている技術の一つです。この技術では、半導体チップと基板の間を非常に細いワイヤーで接続し、電気的な接続を確立します。ワイヤーには主に金やアルミニウムが使用され、その柔軟性と導電性から非常に優れた接続方法とされています。チップ上のパッドにワイヤーを超音波や熱圧力を用いて接合することで、高い信頼性と耐久性を持つ接続が可能になります。
ワイヤーボンディング技術の利点としては、まずそのコスト効率の高さが挙げられます。特に大量生産に適しており、比較的低コストで高品質な接続が可能です。また、技術的に成熟しているため、多くの製造ラインで標準的に使用されています。このため、新たな設備投資が少なくて済む点も大きなメリットです。さらに、柔軟な設計が可能であり、さまざまな形状やサイズのデバイスに対応できる点も魅力です。
一方で、ワイヤーボンディングにはいくつかの課題も存在します。例えば、接続のためにワイヤーを用いるため、スペース効率が劣る場合があります。特に小型化が進むデバイスにおいては、フリップチップ実装に対して劣る部分があるのは否めません。しかし、これらの課題も最新技術の導入によって徐々に克服されつつあります。
フリップチップ実装との比較
フリップチップ実装は、ワイヤーボンディングと並ぶ主要な半導体接続技術の一つです。この技術では、チップを裏返しにして基板に直接接合します。チップ上のバンプと呼ばれる小さな突起が、基板上の対応するパッドと直接接続することで電気的な接続を確立します。これにより、ワイヤーボンディングのような追加の接続材料を必要とせず、よりコンパクトな実装が可能になります。
フリップチップ実装の最大の利点は、その高いスペース効率です。ワイヤーを使用しないため、接続部分の占有面積が小さく、デバイス全体の小型化に貢献します。また、接続距離が短いため、信号の遅延や損失が少なく、高速動作が求められるアプリケーションに適しています。さらに、接続強度が高く、耐熱性や耐振動性に優れているため、高信頼性が求められる用途にも向いています。
一方、フリップチップ実装にはいくつかのデメリットも存在します。まず、製造コストが比較的高い点が挙げられます。チップのバンプ形成や高精度な接合技術が必要となるため、設備投資や製造プロセスが複雑になります。また、製造ラインの立ち上げに時間とコストがかかる点も考慮する必要があります。これに対して、ワイヤーボンディングは既存の製造設備で対応可能なため、コストパフォーマンスに優れています。
ワイヤーボンディング技術の進化の歴史
ワイヤーボンディング技術は、1960年代に初めて実用化されて以来、半導体製造の中核を担ってきました。当初は金属ワイヤーを手作業で接合する方法が一般的でしたが、技術の進歩とともに自動化が進み、現在では高度なロボット技術を用いた自動ワイヤーボンディングが主流となっています。この自動化により、製造速度と精度が飛躍的に向上し、コストも大幅に削減されました。
1970年代から1980年代にかけて、超音波振動を用いたワイヤーボンディング技術が開発され、接合強度と信頼性がさらに向上しました。超音波を利用することで、ワイヤーとパッドの間に強固な接合が形成され、電気的な接続が安定するようになりました。また、これにより異なる材料同士の接合が可能となり、技術の適用範囲が広がりました。
2000年代以降は、ナノテクノロジーの発展により、ワイヤーボンディング技術も新たな段階に入りました。ナノメートルスケールのワイヤーや接合技術が開発され、さらに小型で高性能なデバイスの製造が可能となりました。最近では、環境に配慮したエコ材料を用いたワイヤーボンディングが注目されており、持続可能な製造プロセスの確立に向けた研究も進んでいます。
超音波振動の活用とその利点
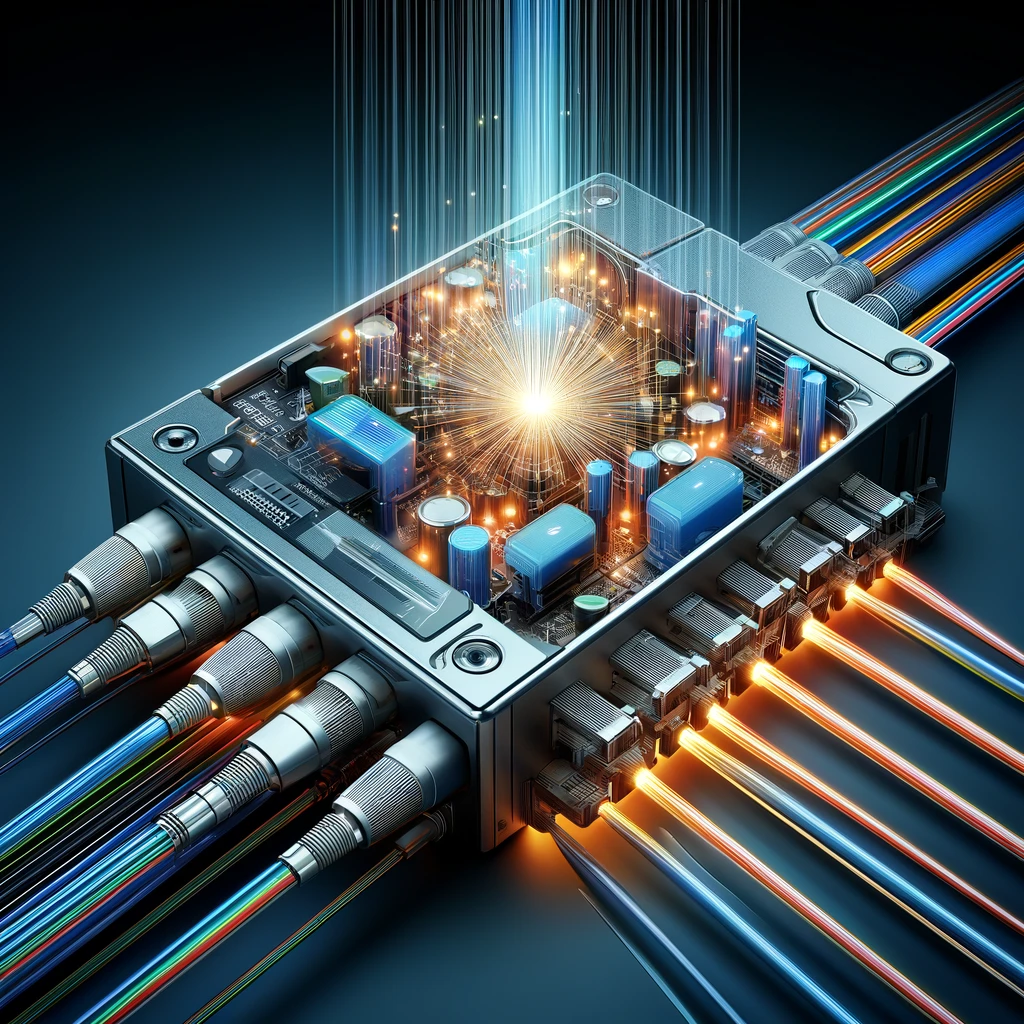
超音波振動は、ワイヤーボンディング技術の中で重要な役割を果たしています。この技術では、ワイヤーと接合パッドの間に超音波振動を加えることで、接合面に微小な変形を引き起こし、強固な接合を実現します。超音波振動の使用により、接合プロセスが迅速かつ効率的に行われるため、製造速度の向上とコスト削減が可能です。
超音波振動の最大の利点は、接合強度の向上です。振動により接合面がクリーンな状態に保たれ、酸化膜や汚れが取り除かれるため、接合の信頼性が高まります。また、低温での接合が可能となるため、熱による材料の劣化を防ぎ、デバイス全体の寿命を延ばすことができます。これにより、高温環境や厳しい使用条件下でも安定した性能を発揮するデバイスの製造が可能です。
さらに、超音波振動を活用することで、異なる材料間の接合が容易になります。例えば、アルミニウムと金などの異種材料間でも、強固で信頼性の高い接合が可能となります。これにより、さまざまな材料特性を持つデバイスの製造が可能となり、応用範囲が広がります。また、接合プロセスが短時間で完了するため、製造ラインの効率も向上し、生産性の向上に寄与します。
高速化・高精度化のための最新技術
ワイヤーボンディング技術の進化は、製造速度と精度の両方で大きな飛躍を遂げています。特に、自動化技術の導入により、高速で高精度なボンディングが実現されています。これには、先端のロボティクス技術やAIによるプロセス制御が重要な役割を果たしています。自動化システムは、精密な動作を繰り返すことで、微細な位置ズレを防ぎ、安定した品質を維持します。
さらに、高速化のための技術としては、超音波振動やレーザー技術が挙げられます。超音波振動は、短時間で強固な接合を可能にし、製造プロセスの効率を大幅に向上させます。レーザー技術は、非接触での高精度な加工を実現し、デバイスの微細化に対応しています。これらの技術の組み合わせにより、従来の方法では達成できなかった高速かつ高精度な接合が可能となり、製造コストの削減にも寄与しています。
また、最新の材料技術も重要な要素です。ナノ材料や新型合金の開発により、接合の信頼性がさらに向上しています。これらの材料は、高温や高圧などの過酷な条件下でも安定した性能を発揮し、デバイスの長寿命化に貢献します。製造装置の進化と相まって、これらの新材料は今後のワイヤーボンディング技術のさらなる発展を支える重要な要素となります。
実装プロセスの最適化
ワイヤーボンディング技術の進化は、実装プロセス全体の最適化にも大きく寄与しています。プロセスの各段階において、最新の技術と設備を導入することで、効率的かつ高品質な製造が可能となります。例えば、温度管理や環境制御システムの高度化により、接合の安定性が向上し、欠陥の発生を最小限に抑えることができます。
プロセスの最適化には、工程ごとのリアルタイムモニタリングも重要です。最新のセンサ技術を活用し、接合の状態やワイヤーの品質を常に監視することで、不良品の早期発見と対策が可能となります。また、AIを用いたデータ解析により、プロセスの効率化と品質向上が図られています。これにより、製造ラインの生産性が大幅に向上し、コスト削減にも繋がります。
さらに、実装プロセスの自動化も進んでいます。自動搬送システムやロボットアームの導入により、人手によるミスやバラツキを排除し、安定した製造が実現されています。これにより、高度な技術が要求される製品の大量生産が可能となり、市場の需要に迅速に対応できるようになっています。最適化された実装プロセスは、製造業の競争力を高めるために欠かせない要素となっています。
小型化・薄型化への対応
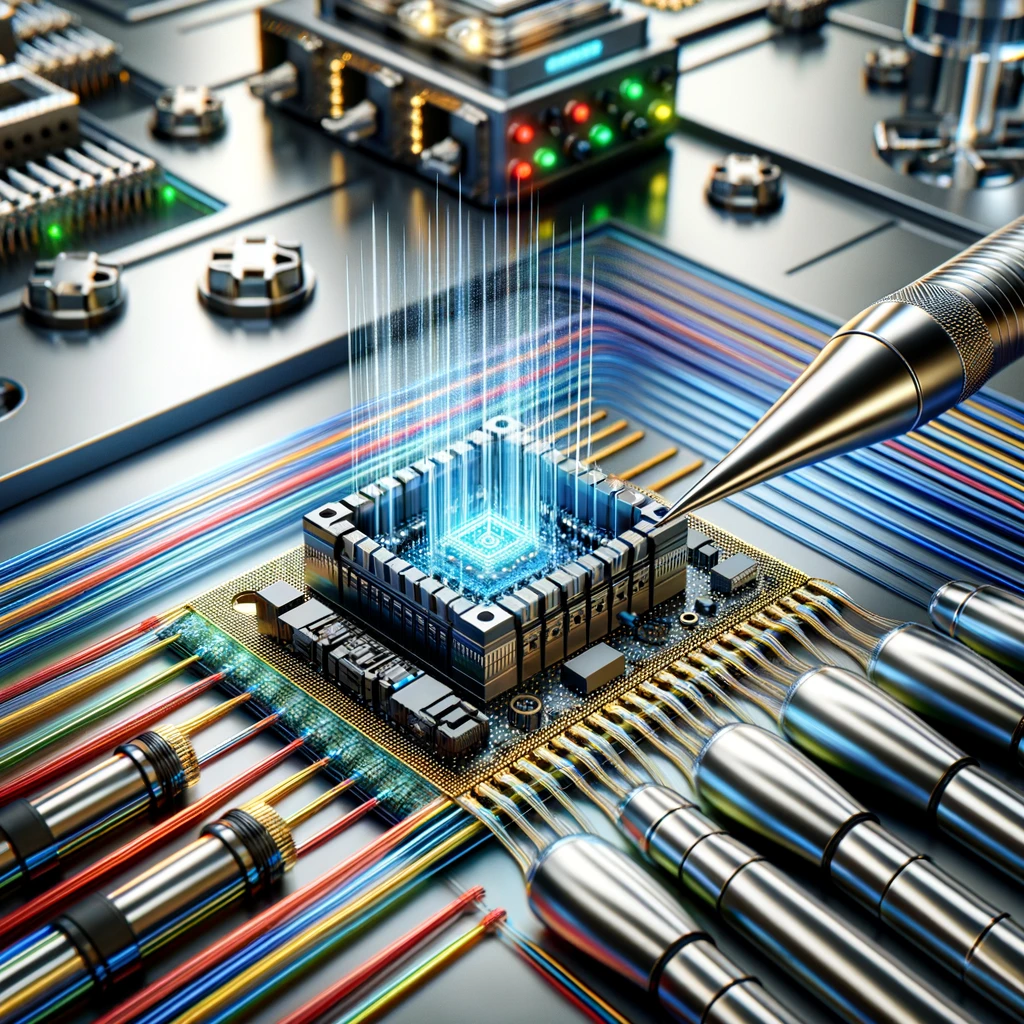
現代の電子機器のトレンドは、小型化と薄型化です。ワイヤーボンディング技術もこれに対応する形で進化を遂げています。特に、チップの実装密度を高めるための技術が重要視されています。超細径ワイヤーや微細ピッチ技術の導入により、チップ間のスペースを最小限に抑え、デバイス全体の小型化が実現されています。
また、薄型化への対応として、低プロファイルワイヤーボンディング技術が開発されています。これにより、チップと基板の間の接合部分が薄くなり、デバイス全体の厚みを抑えることが可能です。さらに、フリップチップ実装と組み合わせることで、さらなる薄型化が実現されています。このような技術の進化は、スマートフォンやタブレットなど、携帯性が求められるデバイスの開発に大きな影響を与えています。
これらの小型化・薄型化技術は、単にデバイスのサイズを縮小するだけでなく、性能の向上にも寄与しています。短い接続距離により、信号伝達の遅延が減少し、高速動作が可能となります。また、エネルギー効率が向上し、バッテリー寿命の延長にも繋がります。これにより、消費者にとってより魅力的な製品が提供され、市場競争力が高まります。
高信頼性を実現するための技術
ワイヤーボンディング技術の進化は、デバイスの高信頼性を実現するための重要な要素です。特に、過酷な環境下での使用に耐えるための技術が求められています。例えば、軍事用や宇宙用のデバイスでは、高温、高圧、振動などの厳しい条件に耐える必要があります。このため、接合部分の強度と耐久性が極めて重要です。
超音波振動やレーザー技術の活用により、接合の強度が飛躍的に向上しています。これにより、振動や衝撃に対する耐性が強化され、高信頼性が求められる用途に適しています。また、接合部分の品質を確保するための非破壊検査技術も進化しており、接合の状態をリアルタイムで評価することが可能です。これにより、製造段階での不良品を早期に発見し、対策を講じることができます。
さらに、最新の材料技術も高信頼性の実現に寄与しています。耐熱性や耐酸化性に優れた新素材の導入により、接合部分の長寿命化が図られています。これにより、長期間にわたって安定した性能を維持することが可能となり、信頼性の向上に繋がっています。これらの技術の進化は、高性能なデバイスの開発と供給を支える基盤となっています。
コスト効率の改善
ワイヤーボンディング技術の進化は、製造コストの効率化にも大きな影響を与えています。特に、自動化と最適化技術の導入により、人件費や材料費の削減が可能となっています。自動化システムは、高速かつ高精度でのボンディングを実現し、製造時間を短縮することでコスト削減に貢献します。また、最新のAI技術を用いることで、製造プロセスの効率化と不良品の早期発見が可能となり、トータルコストの低減に寄与しています。
材料費の削減も重要な要素です。従来の金ワイヤーに代わり、アルミニウムや銅ワイヤーの使用が増加しています。これらの材料はコストが低く、導電性や接合強度も優れているため、全体の製造コストを抑えつつ高品質な接合が実現可能です。さらに、エコフレンドリーな材料の導入により、環境負荷を低減しつつ、コスト効率の向上が図られています。
プロセスの最適化もコスト効率改善に寄与しています。リアルタイムモニタリングやプロセス制御技術の進化により、製造プロセスのムダを排除し、効率的な生産が可能となっています。これにより、製造ラインのダウンタイムを最小限に抑え、生産性を最大化することができます。結果として、総合的なコスト効率が向上し、競争力の強化に繋がっています。
フリップチップ実装の課題とワイヤーボンディングの解決策
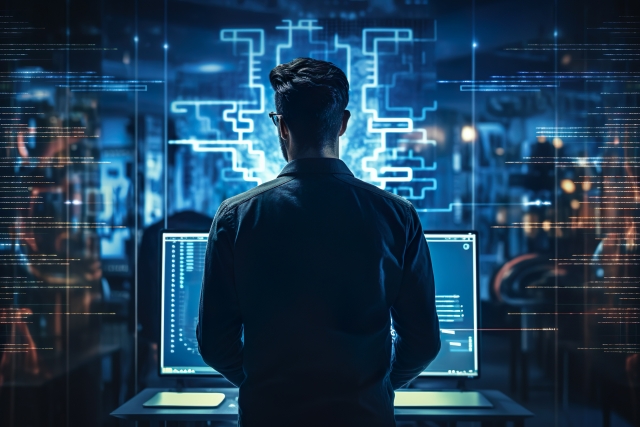
フリップチップ実装は、多くの利点を持つ一方で、いくつかの課題も抱えています。まず、製造コストが高い点が挙げられます。フリップチップ実装には高度な設備と技術が必要であり、これがコスト上昇の要因となります。また、チップと基板の接合において、バンプ形成や精密な位置合わせが求められるため、プロセスが複雑で時間がかかることも問題です。
これらの課題に対する解決策として、ワイヤーボンディング技術が再評価されています。ワイヤーボンディングは、比較的低コストで実装が可能であり、既存の製造設備を利用できるため、新たな設備投資が不要です。さらに、技術の進化により、接合強度や信頼性も大幅に向上しており、フリップチップ実装と同等以上の性能を発揮することが可能です。
また、ワイヤーボンディング技術は、プロセスの柔軟性が高い点も大きなメリットです。様々な形状やサイズのチップに対応できるため、多様な製品ラインに適応可能です。さらに、超音波振動やレーザー技術の導入により、接合プロセスが迅速化され、生産性が向上しています。これにより、総合的な製造コストの削減と品質の向上が実現され、フリップチップ実装の課題を克服する有力な手段となっています。
今後の技術展望
ワイヤーボンディング技術は、今後さらに進化を遂げることが期待されています。特に、ナノテクノロジーや新材料の開発が、技術の発展を牽引する重要な要素となるでしょう。ナノスケールの接合技術により、より小型で高性能なデバイスの製造が可能となり、次世代の電子機器の開発が加速します。これにより、様々な産業分野での応用が広がり、技術の進化が期待されます。
また、AIとビッグデータの活用も、ワイヤーボンディング技術の未来を形作る要素となります。AIによるプロセス制御やデータ解析により、製造プロセスの効率化と品質向上が図られます。リアルタイムでのモニタリングとフィードバックにより、最適な製造条件を自動で設定し、安定した製品品質を維持することが可能です。これにより、製造コストの削減と生産性の向上が実現され、競争力が強化されます。
さらに、環境に配慮した技術開発も重要なテーマとなります。エコフレンドリーな材料の導入や、エネルギー効率の高いプロセスの開発により、持続可能な製造が求められます。これにより、企業の社会的責任を果たしつつ、コスト効率の向上が図られます。ワイヤーボンディング技術の未来は、技術革新と持続可能な開発の両立により、ますます明るいものとなるでしょう。
まとめ
ワイヤーボンディング技術は、半導体実装の分野で重要な役割を果たし続けています。技術の進化により、高速化・高精度化が進み、製造コストの効率化が図られています。特に、超音波振動やレーザー技術の活用により、接合の強度と信頼性が向上しています。
また、プロセスの最適化と自動化により、効率的な製造が実現され、小型化・薄型化にも対応しています。これらの技術革新は、競争力の強化に寄与し、今後の市場展開においても大きなメリットをもたらします。ワイヤーボンディング技術の進化と展望に期待が高まります。