量子コンピューティングの進化は、半導体産業に新たな革命をもたらしています。特に、微細な欠陥の検出と解析は、製品の品質向上と信頼性確保において重要な課題です。本記事では、最新の半導体検査法について、AIや量子技術を駆使した最先端のアプローチを紹介し、産業界のニーズに応えるための革新的な技術とその応用事例を探ります。
量子コンピューティングの進展と半導体検査の重要性
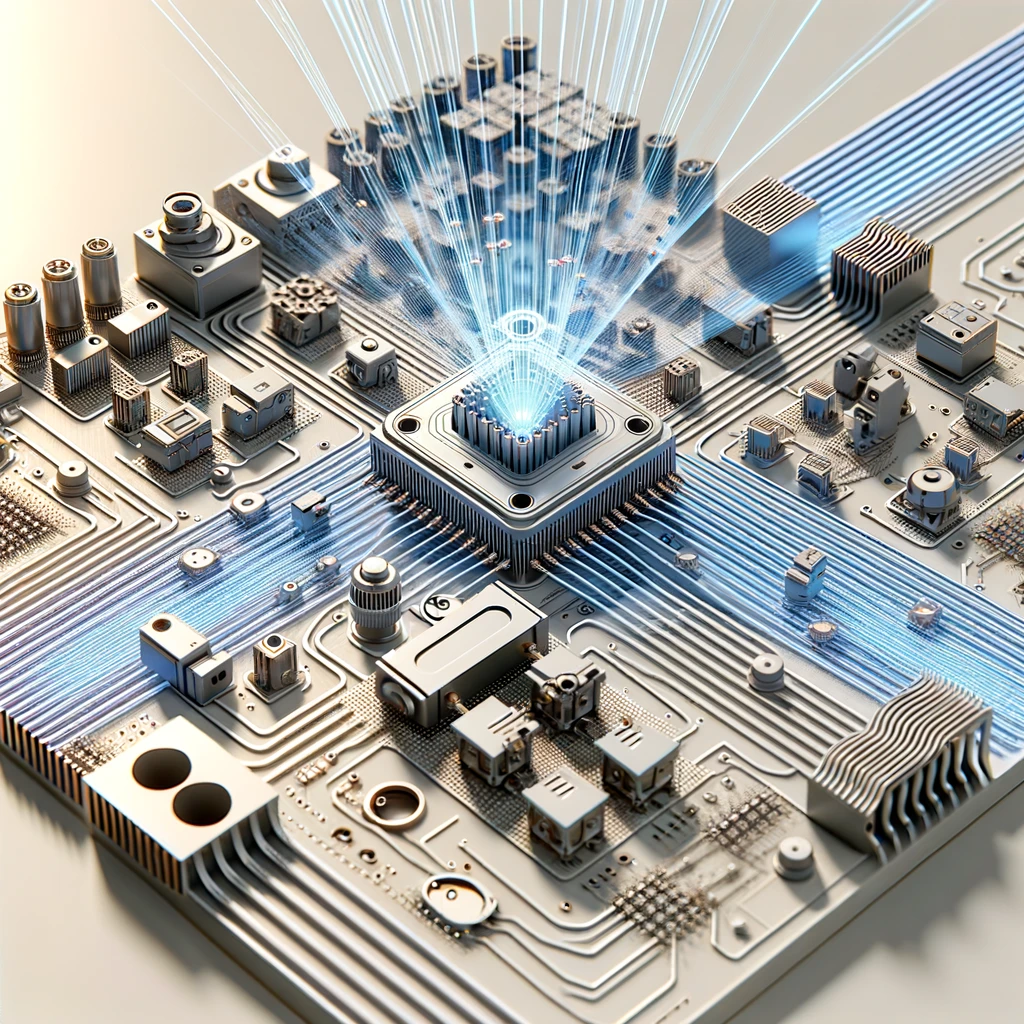
量子コンピューティングの進展は、データ処理のスピードと効率性を飛躍的に向上させ、さまざまな産業において新たな可能性を切り開いています。その中でも半導体産業は、特に量子技術の恩恵を受ける分野の一つです。半導体製造における微細欠陥の検出と解析は、製品の品質向上と信頼性確保に直結するため、極めて重要です。
従来の検査手法では、微細化が進む現代の半導体製造プロセスに対応しきれないことが多く、これが製品不良の原因となり得ます。そこで、量子コンピューティングを活用した新しい検査手法の導入が求められています。これにより、より迅速かつ正確な欠陥検出が可能となり、製造プロセスの効率化と品質管理の向上が実現します。
量子コンピューティングの特徴として、並列処理能力の高さが挙げられます。この特性を活用することで、従来の計算方式では難しいとされていた微細欠陥の検出や解析が容易になります。また、量子アルゴリズムを駆使することで、従来の方法では見逃されがちな微小な欠陥も高精度で検出することが可能です。これにより、製品の歩留まりを向上させ、コスト削減にも寄与することが期待されています。
半導体製造における微細欠陥の発生原因
半導体製造プロセスにおける微細欠陥の発生は、多くの要因によって引き起こされます。これらの要因には、材料の品質、製造環境の微小な変動、プロセスの安定性、不純物の混入などが含まれます。特に、ナノメートルスケールでの製造が進む現代の半導体製造においては、極微細な欠陥も製品の性能や信頼性に大きな影響を与える可能性があります。
例えば、シリコンウェハーの表面に微細な粒子が付着するだけで、回路の断線や短絡を引き起こし、デバイスの機能を損なうことがあります。さらに、製造プロセス自体の複雑さも欠陥発生の一因となります。多層構造を持つ半導体デバイスでは、各層の形成プロセスにおいて精密な制御が求められますが、微小な変動が積み重なることで欠陥が生じることがあります。
また、エッチングや成膜などの工程で使用される化学薬品や装置の状態も、欠陥発生に影響を与えることがあります。これらの要因を総合的に管理し、欠陥を最小限に抑えるためには、高度な検査技術が不可欠です。
伝統的な半導体検査手法の限界
従来の半導体検査手法は、光学顕微鏡や電子顕微鏡を用いた観察が主流でしたが、これらの手法には限界があります。まず、光学顕微鏡は波長の制約により、微細化が進む現代の半導体デバイスの欠陥検出には不向きです。
一方、電子顕微鏡は高い解像度を持つものの、観察範囲が狭く、時間とコストがかかるという欠点があります。また、これらの手法は主観的な判断に依存する部分が大きく、検査者の技術や経験によって結果が左右されることも問題です。
さらに、従来の検査手法ではリアルタイムでの欠陥検出が難しく、生産ラインにおける即時対応ができないことが多いです。これにより、欠陥が発見されるまでに多くの不良品が生産されてしまうリスクがあります。これらの課題を克服するためには、新しい検査技術の導入が求められています。量子コンピューティングやAIを活用した新しい検査手法は、これらの限界を超え、高精度かつ効率的な欠陥検出を実現する可能性があります。
AIを活用した画像解析技術の進化
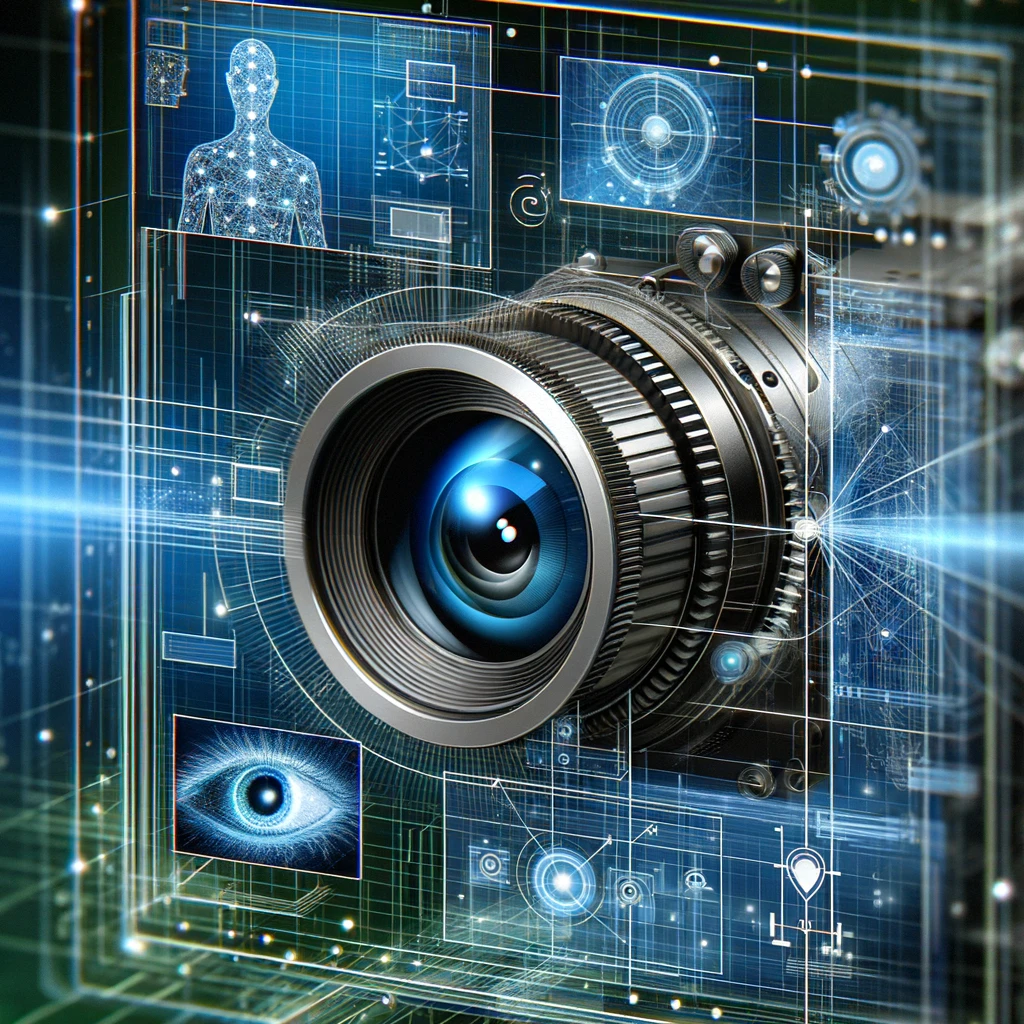
AIを活用した画像解析技術は、半導体検査に革命をもたらしています。従来の検査手法では検出が難しかった微細欠陥も、AIアルゴリズムによる解析により高精度で検出可能となりました。例えば、ディープラーニング技術を用いることで、膨大な画像データから欠陥パターンを学習し、自動的に欠陥を識別することができます。これにより、検査のスピードと精度が飛躍的に向上し、製品の品質管理が大幅に改善されました。
AI画像解析のもう一つの利点は、リアルタイムでの検査が可能な点です。生産ライン上での即時欠陥検出が実現することで、早期の問題発見と迅速な対応が可能となります。これにより、不良品の大量生産を防ぎ、製造コストの削減にもつながります。さらに、AIは疲労や感情に左右されることがないため、安定した検査精度を維持することができます。
また、AI技術は継続的な学習と進化を遂げることができるため、新しい欠陥パターンや製造プロセスの変化にも柔軟に対応できます。これにより、半導体製造における欠陥検出の精度と効率が一層向上し、次世代の高品質な半導体製品の生産が可能となります。
量子技術を利用した新しい欠陥検出法
量子技術を活用した欠陥検出法は、半導体検査の新たな次元を開いています。この技術は、量子力学の原理を利用して、従来の手法では検出が困難だった微細な欠陥を高精度で特定することが可能です。例えば、量子ビット(キュービット)の超高感度な反応を活用し、ナノスケールの欠陥をリアルタイムで検出することができます。このアプローチにより、従来の光学的および電子顕微鏡では見逃されがちな微小な欠陥も確実に捉えることができます。
さらに、量子計測技術は、極低温環境下でも高精度な検出を可能にするため、半導体製造プロセスのあらゆる段階での欠陥検出に適しています。これにより、製造過程で発生する微小な物理的欠陥や化学的不純物を迅速に特定し、問題の早期解決を図ることができます。量子技術の導入は、製品の信頼性向上と歩留まりの改善に大きく寄与するでしょう。
量子技術を利用した検査法のもう一つの利点は、プロセスの自動化とデータ解析の精度向上です。量子コンピュータを用いることで、膨大なデータを迅速に処理し、欠陥のパターンをリアルタイムで解析することが可能です。これにより、製造ラインの効率性が向上し、欠陥発生の原因を迅速に特定することができます。量子技術は、今後の半導体製造において欠かせないツールとなるでしょう。
先端のSEM式欠陥検査装置の役割
先端の走査電子顕微鏡(SEM)を用いた欠陥検査装置は、半導体検査の精度と効率を大幅に向上させています。SEM技術は、高解像度の画像を提供し、微細な欠陥を詳細に観察することが可能です。特に、ナノメートルスケールの微小な欠陥の検出において、SEMは他の検査手法に比べて優れた性能を発揮します。この技術により、製造プロセス中に発生する欠陥を迅速かつ正確に特定し、製品の品質を維持することができます。
SEM式欠陥検査装置は、材料の表面だけでなく、内部構造の欠陥も高解像度で観察できるため、半導体デバイスの多層構造における欠陥検出に非常に有効です。これにより、従来の検査手法では見逃されがちな内部欠陥も確実に検出することができます。さらに、最新のSEM技術は、AIアルゴリズムと組み合わせることで、検査結果の解析と欠陥の分類を自動化し、検査の効率と精度を一層向上させることが可能です。
また、SEM式欠陥検査装置は、製造プロセスの最適化にも役立ちます。欠陥検出データをリアルタイムで解析し、製造条件の微調整を行うことで、製品の品質と歩留まりを向上させることができます。これにより、製造コストの削減と生産性の向上が実現します。SEM技術の進化は、半導体検査の新たな可能性を広げ、産業全体の競争力を強化する鍵となるでしょう。
ナノスケールでの欠陥検出と解析技術
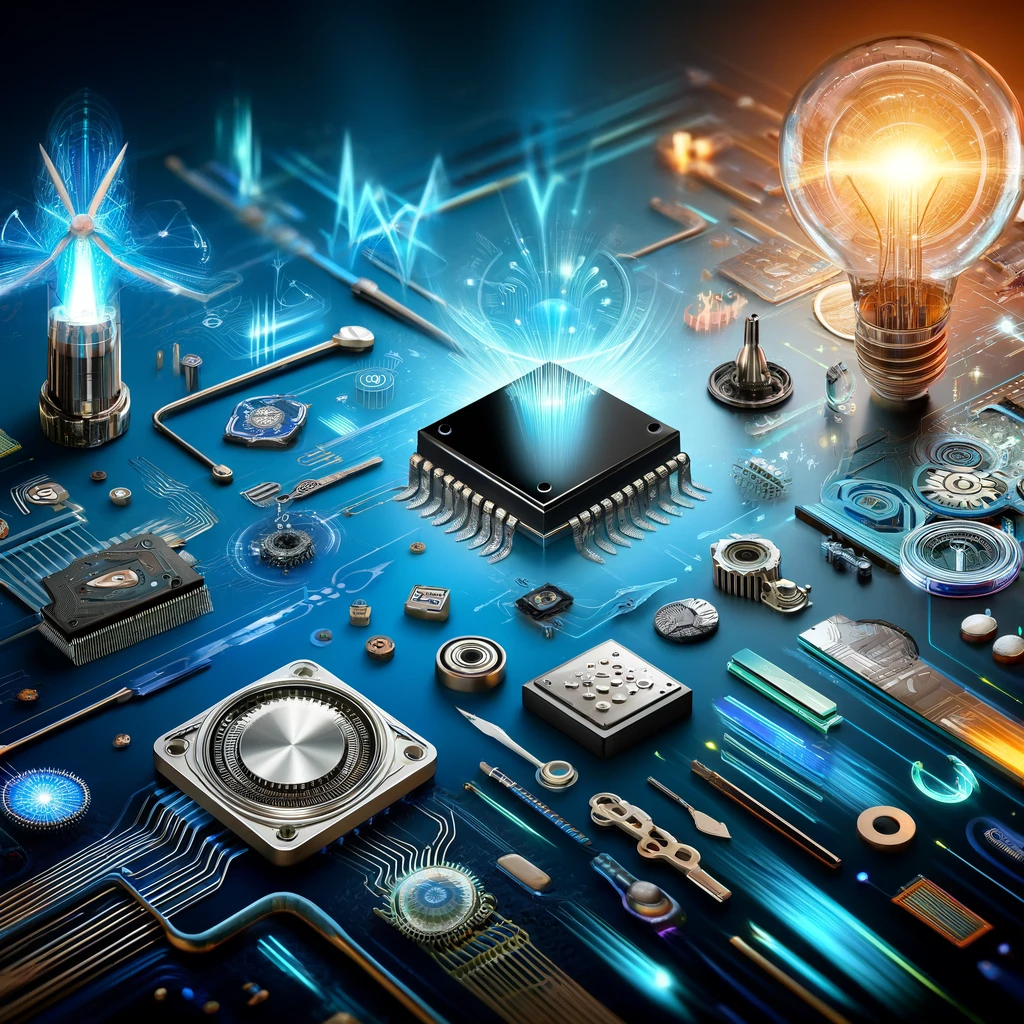
ナノスケールでの欠陥検出と解析技術は、現代の半導体製造において不可欠な要素です。微細化が進む半導体デバイスにおいて、ナノメートルレベルの欠陥が製品の性能や信頼性に大きな影響を与えることがあります。従来の検査手法では検出が難しいこれらの欠陥を特定するために、最先端の技術が導入されています。例えば、ナノスケールのX線顕微鏡や原子間力顕微鏡(AFM)などの高解像度解析装置が用いられています。
これらの装置は、半導体デバイスの表面および内部構造を詳細に観察し、微小な欠陥を高精度で検出することが可能です。特に、原子間力顕微鏡は、表面の原子レベルの凹凸を測定し、ナノメートルスケールの欠陥を識別する能力を持っています。また、X線顕微鏡は、材料の内部構造を非破壊で解析できるため、多層構造の半導体デバイスの検査に適しています。
さらに、ナノスケールの欠陥検出技術は、AIアルゴリズムと組み合わせることで、その効果を最大限に発揮します。AIを活用することで、膨大なデータを迅速に解析し、欠陥のパターンや原因を特定することができます。これにより、製造プロセスの最適化や品質管理が一層進み、製品の信頼性向上とコスト削減が実現します。ナノスケールの解析技術は、今後の半導体産業において不可欠なツールとなるでしょう。
最新の3DX線顕微鏡技術の応用
最新の3DX線顕微鏡技術は、半導体検査の革新をもたらしています。この技術は、高解像度の3次元画像を提供し、半導体デバイスの内部構造を詳細に観察することが可能です。従来の2次元検査では見逃されがちな欠陥も、3DX線顕微鏡を用いることで、立体的に検出することができます。これにより、製品の品質管理が飛躍的に向上し、不良品の発生を大幅に減少させることができます。
3DX線顕微鏡は、非破壊検査が可能であるため、製品を傷つけることなく内部の欠陥を検出できます。これにより、製造プロセスの各段階での欠陥検出が可能となり、早期に問題を発見し対策を講じることができます。さらに、最新の3DX線技術は、リアルタイムでの画像取得と解析を可能にし、製造ラインにおける即時対応を実現します。
また、3DX線顕微鏡技術は、材料の組成や構造の詳細な分析にも適しており、半導体デバイスの性能向上や新素材の開発に役立ちます。例えば、異なる材料間の界面の状態や、微細な内部構造の評価を行うことで、製品の改良点や潜在的な問題点を特定することができます。この技術は、半導体製造プロセス全体の最適化に貢献し、より高品質な製品の提供を可能にします。
最新の3DX線顕微鏡技術の導入は、半導体産業において競争力を強化するための重要なステップとなります。製品の品質向上とコスト削減を両立させるために、この先進的な検査技術を積極的に活用することが求められています。
量子コンピューティングがもたらす検査法の変革
量子コンピューティングは、半導体検査の分野において革命的な変化をもたらしています。量子コンピュータの並列処理能力と高い計算速度を利用することで、従来の検査手法では困難だった複雑なデータ解析が可能となり、微細な欠陥の検出精度が飛躍的に向上しました。
特に、量子アルゴリズムを用いた欠陥検出は、ノイズに対する耐性が強く、微小な変動も正確に捉えることができます。これにより、製造ラインで発生する欠陥の早期発見と迅速な対応が可能となり、製品の品質管理が大幅に改善されます。
量子コンピューティングのもう一つの強みは、リアルタイムでの大規模データ処理です。これにより、製造プロセスの各段階で生成される膨大なデータを即座に解析し、欠陥の原因を特定することができます。従来の方法では時間がかかる解析作業も、量子コンピュータの力を借りることで瞬時に行うことができ、生産性の向上とコスト削減に繋がります。また、量子技術は、シミュレーションやモデリングの精度を高めるため、欠陥予測やプロセスの最適化にも役立ちます。
産業界における実用化と今後の課題
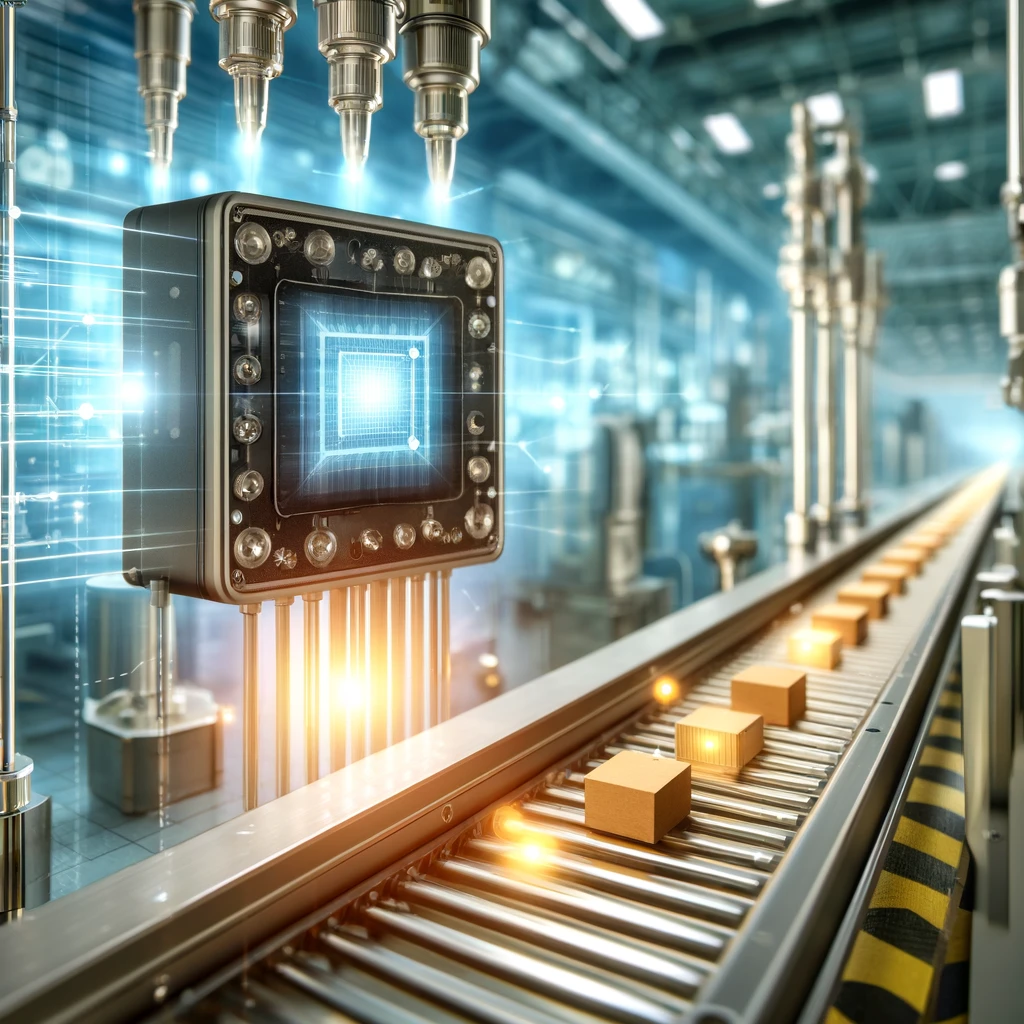
量子コンピューティングの実用化が進む中、産業界でもその応用が広がっています。特に半導体製造業界では、量子技術を活用した新しい検査法が導入され始めており、製品の品質と信頼性の向上が期待されています。例えば、IBMやGoogleなどの企業は、量子コンピューティングを利用して微細な欠陥を高精度で検出するシステムを開発し、製造プロセスの効率化を図っています。これにより、製品の不良率が低下し、コスト削減が実現しています。
しかし、量子コンピューティングの導入にはまだいくつかの課題が残されています。まず、量子コンピュータの開発コストが高く、導入に伴う初期投資が大きいことが挙げられます。また、量子技術に精通した専門家の不足も問題となっており、企業内でのスキル習得や教育が必要です。
さらに、量子コンピュータ自体がまだ発展途上にあるため、その性能を最大限に引き出すための技術的な課題も多く存在します。これらの課題を克服するためには、産学官連携による研究開発や人材育成が不可欠です。
ケーススタディ: 量子技術を利用した成功例
量子技術を活用した成功例として、日立の取り組みが挙げられます。日立は、量子コンピューティングとAIを組み合わせた新しい半導体検査システムを開発し、その成果を実証しています。このシステムは、量子アルゴリズムを用いて微細な欠陥を高精度で検出し、AIによる解析で欠陥の原因を特定するものです。実際の製造ラインでの運用結果では、従来の検査手法に比べて検出精度が大幅に向上し、不良品の発生率が劇的に低減しました。
また、日立はこの技術を活用して製造プロセスの最適化も行っています。欠陥データをリアルタイムで収集・解析し、その結果を基に製造条件を調整することで、製品の品質を維持しながら生産性を向上させることに成功しています。
さらに、このシステムは柔軟性が高く、異なる製品ラインにも容易に適用できるため、幅広い応用が期待されています。このように、量子技術を導入することで、企業は競争力を強化し、より高品質な製品を市場に提供することが可能となります。
まとめ
量子コンピューティングとAI技術の進化により、半導体検査の分野は大きな変革を迎えています。従来の手法では見逃されがちだった微細な欠陥も、これらの先端技術を活用することで高精度に検出することが可能となり、製品の品質と信頼性が飛躍的に向上しています。
また、リアルタイムでのデータ解析やプロセスの最適化が可能となり、製造効率の向上とコスト削減にも貢献しています。今後も量子技術の発展に伴い、半導体検査の手法はさらなる進化を遂げることでしょう。