デジタルツインとシミュレーション技術は、半導体製造のコスト最適化において重要な役割を果たしています。これらの技術を導入することで、製造プロセスの効率化や品質向上が実現し、結果としてコスト削減につながります。本記事では、デジタルツインとシミュレーション技術を活用した半導体製造の具体的な手法とその効果について詳しく解説します。
デジタルツインとは何か
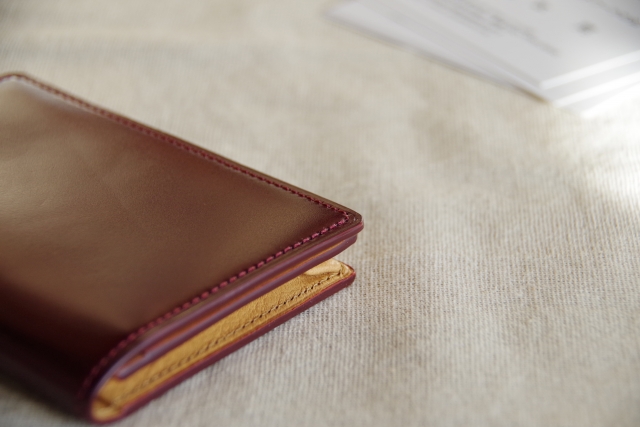
デジタルツインとは、物理的な製品やプロセスの正確なデジタルコピーを指します。この技術は、センサーやIoTデバイスからのデータを収集し、リアルタイムで物理的なシステムと連動する仮想モデルを作成します。デジタルツインは、設計から製造、運用、メンテナンスに至るまでの全ライフサイクルにおいて、システムの性能を監視し、予測分析を行うことができます。
デジタルツインの最大の利点は、物理的なシステムに対する影響をシミュレーションできる点です。これにより、実際の生産ラインを中断することなく、改善点を見つけ出し、コストを削減できます。また、異常検知や予防保全のための予測モデルを構築することで、ダウンタイムを最小限に抑えることが可能です。
さらに、デジタルツインは、製品開発の早期段階から使用することで、設計の最適化や市場投入までの時間短縮に寄与します。例えば、新しい半導体デザインをデジタルツインでテストすることで、製品の品質向上と製造コストの削減を同時に実現できます。このように、デジタルツインは製造業において、特に半導体産業で重要な役割を果たしているのです。
半導体製造におけるデジタルツインの役割
半導体製造において、デジタルツインはプロセス全体の効率化と最適化を図るための重要なツールです。まず、製造装置やラインの仮想モデルを作成し、リアルタイムデータと組み合わせることで、プロセスの詳細な監視と解析が可能になります。この仮想モデルは、製造プロセスの各ステップをシミュレートし、ボトルネックや潜在的な問題を事前に特定するのに役立ちます。
さらに、デジタルツインを活用することで、製造ラインの稼働率を最大化し、無駄なコストを削減できます。例えば、装置のメンテナンススケジュールを最適化することで、予期せぬ故障を未然に防ぎ、稼働時間を延ばすことができます。また、製造プロセス中のパラメータをリアルタイムで調整することにより、製品の品質を一定に保つことが可能です。
特に、半導体製造における微細なプロセス制御では、デジタルツインが有効です。微小なズレや異常を迅速に検出し、修正することで、高い精度と一貫性を維持できます。このように、デジタルツインは半導体製造における生産性向上とコスト削減に不可欠な技術として注目されています。
シミュレーション技術の概要と重要性
シミュレーション技術は、複雑な製造プロセスやシステムの挙動をコンピュータ上で再現する手法です。この技術は、製造業において特に重要であり、製品開発から製造プロセスの最適化まで幅広く利用されています。シミュレーションを活用することで、実際のプロセスを再現し、さまざまなシナリオをテストすることができます。
シミュレーション技術の主な利点は、コストと時間の削減です。実際の製造ラインを止めることなく、仮想環境で試行錯誤ができるため、開発期間を短縮し、リソースの無駄を省くことができます。さらに、リスクの低減も図れます。例えば、新しい製造プロセスや装置の導入前に、シミュレーションで性能や問題点を確認することで、導入後のリスクを最小限に抑えることが可能です。
また、シミュレーション技術は教育やトレーニングにも活用されています。技術者やオペレーターは、実際の製造ラインに触れることなく、シミュレーションを通じてスキルを習得できます。これにより、実際の生産現場でのトラブルを減少させ、スムーズな運用が実現します。このように、シミュレーション技術は半導体製造における効率化とリスク管理において不可欠な役割を果たしています。
デジタルツインとシミュレーション技術の連携
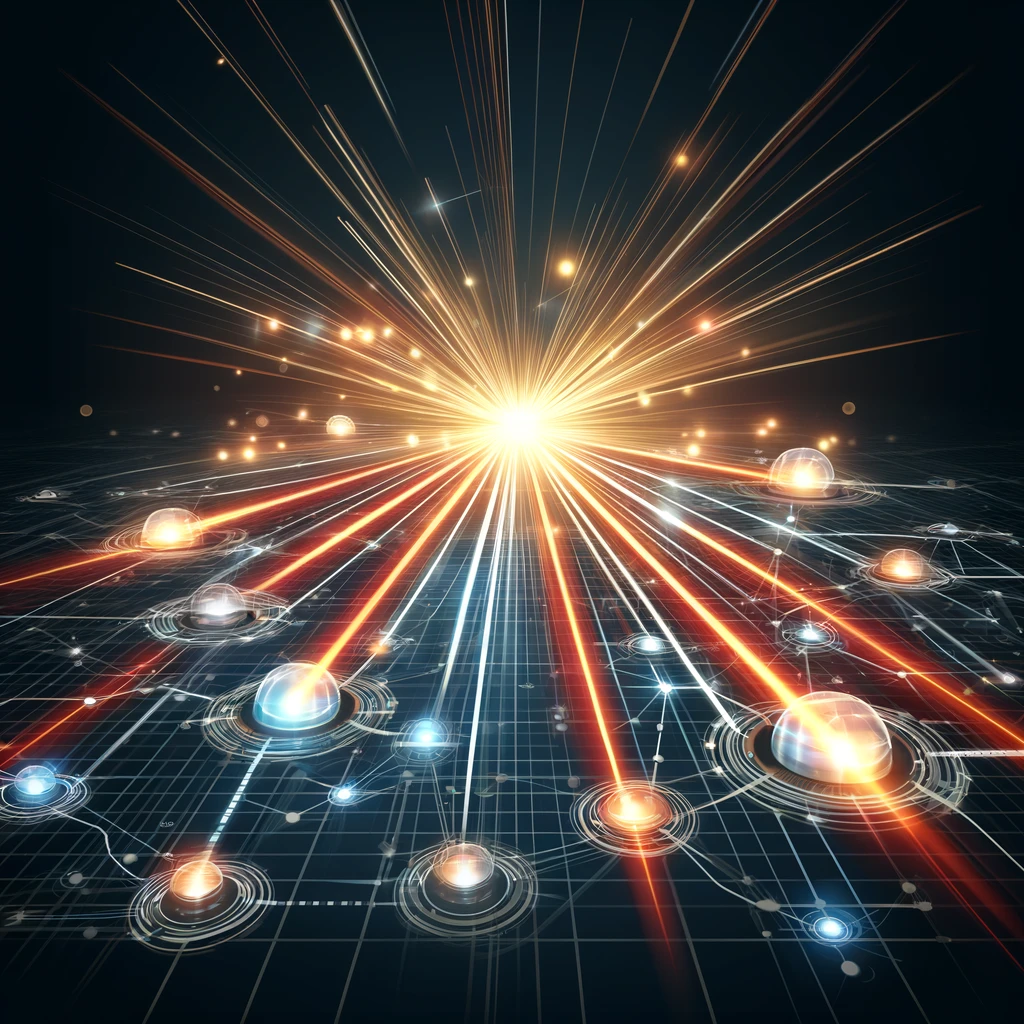
デジタルツインとシミュレーション技術は、半導体製造において強力な連携を見せます。デジタルツインが物理的な製品やプロセスのリアルタイムデータを提供する一方で、シミュレーション技術はそのデータを基に仮想環境での試行錯誤を可能にします。この連携により、製造プロセス全体の効率化と最適化が実現します。
まず、デジタルツインから取得したデータをシミュレーションに取り入れることで、より現実に即したモデルが作成できます。これにより、プロセスの最適化や問題の予測精度が向上し、コスト削減につながります。例えば、製造ラインのボトルネックをシミュレーションで特定し、改善策を仮想環境で試すことで、実際の生産に適用する前にリスクを評価できます。
さらに、デジタルツインとシミュレーション技術の連携は、リアルタイムでのプロセス改善にも寄与します。製造中のデータをリアルタイムでシミュレーションし、最適なパラメータを即座にフィードバックすることで、品質と効率を高めることが可能です。このように、デジタルツインとシミュレーション技術の連携は、半導体製造における革新的なソリューションとして注目されています。
コスト最適化のメリット
デジタルツインとシミュレーション技術の導入により、半導体製造におけるコスト最適化が実現します。まず、これらの技術を用いることで、製造プロセス全体の効率が向上し、無駄なコストを削減できます。例えば、設備の稼働状況をリアルタイムで監視し、必要なメンテナンスを予測することで、ダウンタイムを最小限に抑えることが可能です。これにより、生産ラインの停止による損失を防ぎ、安定した生産が維持されます。
さらに、デジタルツインを活用することで、プロトタイプの開発コストも削減できます。従来の物理的な試作品を作成する代わりに、デジタル環境で設計の検証を行うことで、材料費や時間を節約できます。また、製造プロセスのシミュレーションを通じて、最適な製造条件を見つけ出し、エネルギーコストの削減にも寄与します。これにより、全体的な製造コストが大幅に低減されます。
さらに、デジタルツインとシミュレーション技術の連携により、品質管理の精度が向上し、廃棄物の削減が図れます。不良品の発生を未然に防ぎ、リソースの無駄をなくすことで、コストパフォーマンスの高い生産体制が実現します。このように、デジタルツインとシミュレーション技術は、半導体製造におけるコスト最適化において非常に重要な役割を果たします。
実際の導入事例
デジタルツインとシミュレーション技術は、すでに多くの半導体製造企業で導入され、その効果が実証されています。例えば、ある大手半導体メーカーは、デジタルツインを用いて製造ライン全体を仮想環境で管理しています。この企業では、製造プロセスの各ステップをリアルタイムで監視し、シミュレーションによる最適化を行うことで、生産効率を大幅に向上させました。
また、別の企業では、デジタルツインを活用した設備の予防保全が行われています。センサーからのデータを基に設備の状態を監視し、故障の兆候を早期に発見することで、メンテナンスを計画的に実施しています。この結果、予期せぬダウンタイムが削減され、稼働率が向上しました。これにより、製造コストの削減と生産性の向上が同時に達成されています。
さらに、デジタルツインとシミュレーション技術を組み合わせた製品開発プロジェクトも成功しています。新しい半導体製品の設計段階でデジタルツインを使用し、様々なシナリオをシミュレートすることで、最適な設計を迅速に見つけ出しました。
これにより、開発期間の短縮とコスト削減が実現し、市場投入までのスピードが加速されました。これらの事例から、デジタルツインとシミュレーション技術の導入が半導体製造において大きな効果をもたらすことがわかります。
デジタルツインの導入ステップ
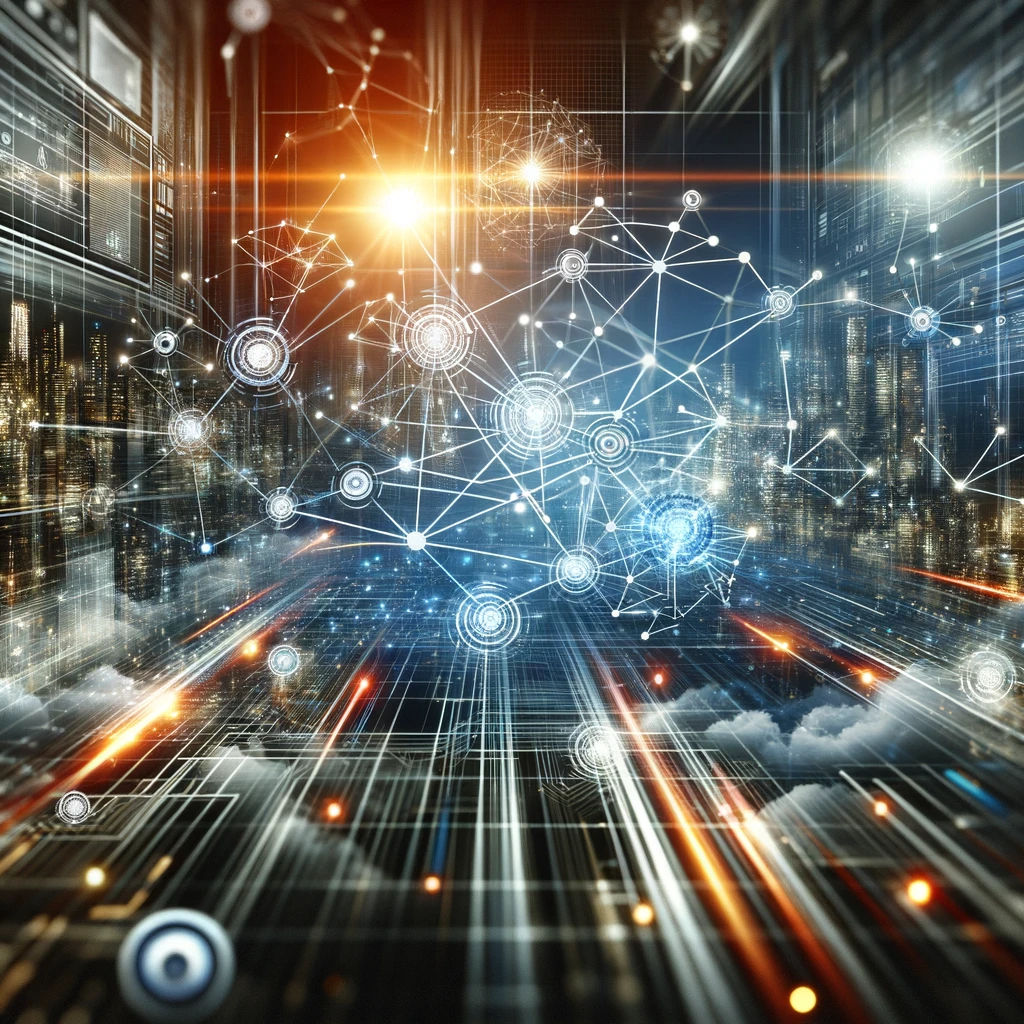
デジタルツインの導入は、段階的に進めることで成功率を高めることができます。まず、導入の第一ステップとして、自社の製造プロセスを詳細に分析し、デジタルツインがどの部分で最も効果的に活用できるかを特定します。この段階では、現状の課題や改善点を明確にし、具体的な導入目標を設定することが重要です。
次に、必要なデータ収集のためのインフラを整備します。センサーやIoTデバイスを設置し、製造ラインからリアルタイムデータを収集できる環境を構築します。このデータは、デジタルツインのモデル構築やシミュレーションに欠かせないため、精度の高いデータ収集が求められます。また、データの管理や分析のためのプラットフォームを導入し、データが効果的に活用される仕組みを整えることも重要です。
その後、デジタルツインの仮想モデルを作成し、シミュレーションを開始します。この段階では、実際の製造プロセスを仮想環境で再現し、様々なシナリオを試すことで、最適なプロセスを見つけ出します。また、モデルの精度を向上させるために、収集したデータを継続的にフィードバックし、モデルの更新を行います。これにより、デジタルツインが実際の製造プロセスに即したリアルタイムの洞察を提供できるようになります。
コスト削減の具体的な手法
デジタルツインとシミュレーション技術を活用することで、半導体製造における具体的なコスト削減手法が実現します。まず、製造プロセスの最適化です。シミュレーションを通じて、製造工程の各ステップを詳細に解析し、効率的な手順を確立します。これにより、無駄な工程やリソースの浪費を削減し、コストを抑えることが可能です。
次に、設備のメンテナンスコスト削減です。デジタルツインを用いて設備の状態を常時監視し、予防保全を実施することで、故障による予期せぬダウンタイムを回避します。これにより、修理コストの削減と稼働率の向上が実現し、全体的なコストパフォーマンスが向上します。また、設備の寿命を延ばすことで、長期的な資本投資の回収率も改善します。
さらに、エネルギーコストの最適化も重要な手法です。デジタルツインとシミュレーションを活用してエネルギー消費を詳細に分析し、エネルギー効率の高い運用方法を導入します。例えば、エネルギー消費のピークを避けるための生産スケジュールの調整や、高効率の機器へのアップグレードなどが挙げられます。これにより、エネルギーコストの削減と環境負荷の軽減が同時に達成されます。
このように、デジタルツインとシミュレーション技術を駆使することで、半導体製造における多角的なコスト削減が可能となり、競争力の向上が期待されます。
データ解析と予測モデルの活用
データ解析と予測モデルは、半導体製造の効率化と品質向上において重要な役割を果たします。まず、製造プロセスから収集される膨大なデータを解析することで、プロセスの最適化ポイントや潜在的な問題を特定できます。例えば、センサーからのリアルタイムデータを活用して、異常なパターンやトレンドを早期に発見し、迅速に対策を講じることが可能です。
予測モデルの活用も大きなメリットをもたらします。機械学習アルゴリズムを用いて、過去のデータから将来のトレンドや異常を予測することができます。これにより、設備の故障や不良品の発生を事前に予測し、計画的なメンテナンスやプロセス調整を行うことができます。例えば、特定の条件下での設備の劣化速度を予測し、最適なメンテナンス時期を決定することで、ダウンタイムを最小限に抑えることができます。
さらに、データ解析と予測モデルを組み合わせることで、製造プロセス全体のパフォーマンスを継続的に改善することが可能です。例えば、製品の品質データを解析し、製造条件と品質の関係を明らかにすることで、最適なプロセスパラメータを設定することができます。このように、データ解析と予測モデルの活用は、半導体製造における競争力を高めるための強力なツールとなります。
デジタルツインによる品質向上
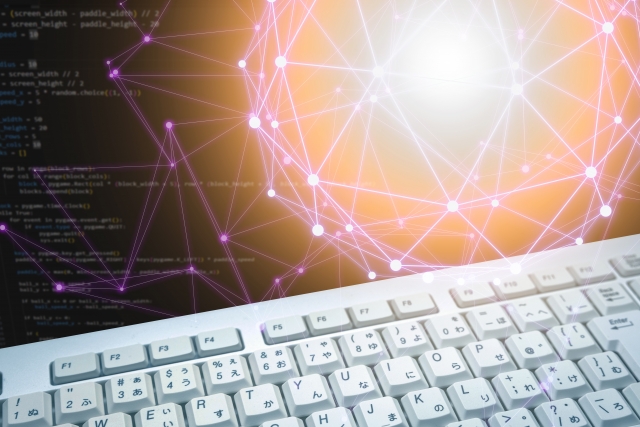
デジタルツイン技術は、半導体製造の品質向上に大きく寄与します。まず、製造プロセス全体をリアルタイムで監視し、詳細なデータを収集することで、品質管理の精度が向上します。例えば、製品の微細な欠陥を早期に検出し、迅速に修正することが可能です。これにより、不良品の発生を未然に防ぎ、製品の品質を一貫して高水準に保つことができます。
さらに、デジタルツインを活用することで、プロセスの最適化が進みます。仮想環境で様々なシナリオをシミュレートし、最適な製造条件を見つけ出すことができます。これにより、製品のばらつきを最小限に抑え、均一な品質を実現します。例えば、特定の温度や圧力条件が製品の性能に与える影響をシミュレーションで解析し、最適な設定を導き出すことが可能です。
また、デジタルツインは予防保全にも役立ちます。設備の状態をリアルタイムで監視し、異常を早期に発見することで、計画的なメンテナンスを実施できます。これにより、設備の故障による品質低下を防ぎ、安定した生産が可能になります。このように、デジタルツイン技術は、半導体製造における品質向上において不可欠な役割を果たしています。
技術導入に伴う課題と対策
デジタルツインとシミュレーション技術の導入には、いくつかの課題が伴います。まず、初期投資のコストが高いことが挙げられます。高度なセンサーやデータ解析プラットフォーム、シミュレーションソフトウェアの導入には、相当な資本が必要です。しかし、長期的な視点で見ると、これらの技術は生産効率の向上とコスト削減に寄与し、投資回収率が高いことが期待されます。
次に、データの品質とセキュリティの確保が重要です。デジタルツインの効果を最大限に発揮するためには、高品質で正確なデータが必要です。また、データの漏洩や不正アクセスを防ぐためのセキュリティ対策も欠かせません。企業は、データガバナンスの強化とセキュリティプロトコルの整備を進める必要があります。
さらに、技術の導入には専門知識が求められます。デジタルツインとシミュレーション技術の運用には、高度な技術スキルと知識が必要です。そのため、企業は専門家の採用や既存の従業員へのトレーニングを行い、技術導入の準備を整える必要があります。また、外部の専門機関やコンサルタントとの連携も有効です。このように、課題を克服するための対策を講じることで、デジタルツインとシミュレーション技術の効果を最大限に引き出すことが可能です。
まとめ
デジタルツインとシミュレーション技術は、半導体製造におけるコスト最適化と品質向上において重要な役割を果たします。これらの技術を活用することで、製造プロセスの効率化や無駄なコストの削減が実現します。また、リアルタイムでのデータ解析と予測モデルの活用により、設備の予防保全や最適な製造条件の設定が可能になります。
さらに、具体的な導入事例を通じて、その効果が実証されています。デジタルツインとシミュレーション技術の連携により、製造プロセス全体の最適化が進み、生産性の向上とコスト削減が同時に達成されています。また、品質管理の精度も向上し、不良品の発生を未然に防ぐことができます。これにより、製品の品質を一貫して高水準に保つことが可能です。
技術導入にはいくつかの課題が伴いますが、適切な対策を講じることでこれらの課題を克服できます。初期投資のコストやデータの品質とセキュリティ、専門知識の不足など、各課題に対する具体的な対策を実施することで、デジタルツインとシミュレーション技術の効果を最大限に引き出すことが可能です。