ホットスタンピング技術は、現代の製造業において重要な役割を果たしています。この技術は、特に自動車産業において軽量化と高強度を両立するために不可欠です。
この記事では、ホットスタンピング技術を用いた超高強度鋼板の成形と軽量化の最新トレンドと具体的な実例を紹介します。
ホットスタンピング技術とは?
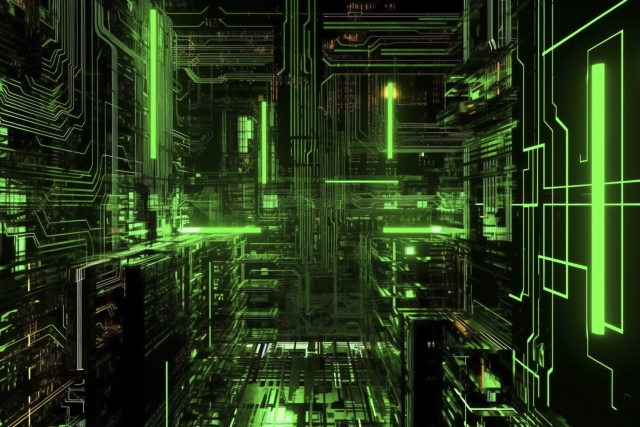
ホットスタンピング技術は、金属成形の一種であり、特に超高強度鋼板の加工に利用される先進的な技術です。このプロセスでは、鋼板を約900℃まで加熱し、その後迅速にプレス機で成形します。高温状態で成形することで、鋼板は柔らかくなり、複雑な形状にも対応可能です。そして急速冷却することで、マルテンサイト組織が形成され、非常に高い強度を持つ部品が得られます。
ホットスタンピング技術の利点は、その高い成形性と強度にあります。従来の冷間プレス成形では、非常に高強度の鋼板を成形する際に多くの課題が生じましたが、ホットスタンピング技術によりこれらの課題が解決されました。また、この技術により、部品の軽量化も実現可能であり、特に自動車産業では車体の軽量化と安全性向上に大きく寄与しています。
具体的には、ホットスタンピング技術は、車両のボディやシャーシの強度部品に広く適用されています。これにより、車両の全体重量を減らしつつ、衝突時の安全性能を向上させることができます。さらに、この技術は複雑な形状の部品を一体成形することができるため、生産工程の効率化にも貢献しています。
ホットスタンピング技術のもう一つの重要な利点は、スプリングバック(成形後の戻り現象)を最小限に抑えることができる点です。これにより、成形後の部品の寸法精度が向上し、製品の品質が確保されます。この技術は、自動車産業だけでなく、他の金属加工分野にも応用が期待されています。
超高強度鋼板の特性と利点
超高強度鋼板(UHSS)は、その名の通り、非常に高い強度を持つ鋼板であり、主に自動車産業で使用されています。この鋼板は、従来の鋼板と比べて、引張強度が非常に高く、耐衝撃性にも優れています。これにより、車両の安全性を向上させながら、軽量化を図ることが可能です。
UHSSの特性の一つに、高い強度と軽量化の両立があります。この特性により、車両の燃費が改善され、CO2排出量の削減にも寄与します。また、超高強度鋼板は耐久性にも優れており、長期間にわたって高い性能を維持することができます。
さらに、UHSSは成形性にも優れており、複雑な形状の部品を精度高く製造することができます。ホットスタンピング技術と組み合わせることで、非常に高い寸法精度を持つ部品を一度に成形することが可能となり、生産効率が向上します。この技術により、部品の製造コストも削減されます。
超高強度鋼板のもう一つの利点は、その優れた耐腐食性です。特殊なコーティング技術や材料組成により、錆や腐食に強く、厳しい環境下でも高い性能を発揮します。この特性により、車両の長寿命化が実現し、メンテナンスコストの削減にもつながります。
以上のように、超高強度鋼板は、その高い強度、軽量化、耐久性、成形性、耐腐食性などの特性により、自動車産業をはじめとする多くの分野で重要な役割を果たしています。ホットスタンピング技術と相まって、今後もさらなる発展が期待される材料です。
最新のホットスタンピング技術の進展
ホットスタンピング技術は、近年の技術革新によりさらなる進展を遂げています。特に、直接通電加熱技術の導入により、効率的な加熱と冷却が可能となり、生産サイクルタイムが大幅に短縮されています。この技術は、鋼板に直接電流を流して加熱するため、従来の加熱方法に比べてエネルギー効率が高く、コスト削減にも寄与しています。
さらに、部分非焼入れ技術の進展により、部品の一部のみを選択的に加熱・冷却することが可能となりました。これにより、部品の特定の部分だけを高強度化し、他の部分は柔軟性を保つことで、複雑な部品設計が可能となります。この技術は、車両の衝突安全性を向上させるために特に有効です。
また、先進的なシミュレーション技術の発展もホットスタンピングの進化に貢献しています。成形プロセスを詳細にシミュレーションすることで、製造前に問題点を予測し、対策を講じることができます。これにより、試作コストが削減され、生産の信頼性が向上します。さらに、AIや機械学習を活用したデータ解析により、プロセスの最適化が進んでいます。
ホットスタンピング技術の進展は、自動車産業以外にも広がりを見せています。例えば、航空機産業や家電製品の製造においても、この技術が応用されています。特に、軽量化と高強度が求められる分野では、その効果が顕著です。これにより、製品の性能向上とコスト削減が同時に実現されています。
ホットスタンピング技術の最新の進展は、製造業全体において革新をもたらし、次世代の製品開発に不可欠な要素となっています。今後もさらなる技術革新が期待されるこの分野は、ビジネスパーソンにとっても注目すべき領域です。
部分非焼入れ技術と生産性向上の実例
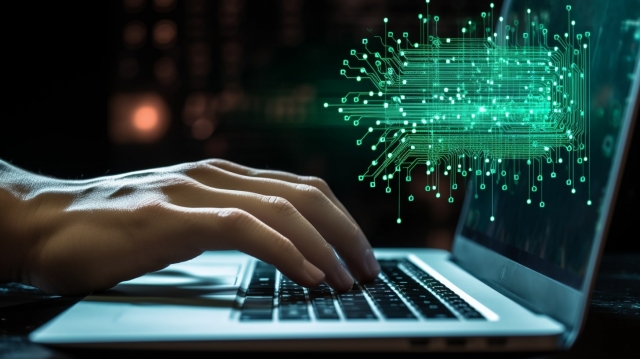
部分非焼入れ技術は、ホットスタンピング技術の中でも特に注目されている革新技術です。この技術は、鋼板の特定の部分のみを加熱・冷却することで、部品の一部を高強度化し、他の部分は柔軟性を保つことができます。これにより、部品全体の性能を最適化しつつ、生産効率を向上させることが可能です。
具体的な実例として、トヨタ自動車は部分非焼入れ技術を活用して、新型車両のボディ部品を製造しています。この技術により、衝突時のエネルギー吸収性能を向上させる一方で、車両の軽量化を実現しました。これにより、燃費の向上とCO2排出量の削減にも寄与しています。
また、日産自動車も部分非焼入れ技術を導入し、生産ラインの効率化を図っています。特に、複雑な形状の部品に対して、この技術を適用することで、従来の冷間プレス成形では実現できなかった高い寸法精度を達成しています。これにより、部品の品質向上とコスト削減が同時に実現されています。
さらに、部分非焼入れ技術は、製造業全体においても広く応用されています。例えば、航空機部品の製造においても、この技術が活用されています。航空機の構造部品は、高い強度と軽量化が求められるため、部分非焼入れ技術により、これらの要求を満たすことができます。
部分非焼入れ技術の導入により、生産性の向上だけでなく、製品の性能も大幅に向上しています。この技術は、今後ますます重要性を増し、製造業全体における競争力の向上に寄与するでしょう。部分非焼入れ技術の実例を通じて、その効果と可能性を理解することが、ビジネスの成功に繋がります。
自動車産業では、軽量化と安全性の両立がますます重要な課題となっています。このニーズに応えるために、ホットスタンピング技術を用いた超高強度鋼板の採用が進んでいます。軽量化は燃費向上とCO2排出削減に直結するため、自動車メーカーにとっては非常に重要です。一方で、衝突安全性を確保するためには、車体の高強度化が不可欠です。
ホットスタンピング技術を用いることで、車両の構造部品を高強度かつ軽量に製造することが可能となります。具体的には、車両の骨格部品や衝突時のエネルギー吸収部品に超高強度鋼板が使用されます。これにより、車両全体の重量を削減しつつ、衝突安全性能を向上させることができます。
例えば、マツダはMAZDA3において980MPa級以上の超高強度鋼板を積極的に採用し、車体の軽量化と衝突安全性の両立を図っています。また、日産も新型車種においてホットスタンピング技術を用いた高強度部品を採用し、燃費性能と安全性の向上を実現しています。これらの取り組みにより、自動車メーカーは市場競争力を高めることができます。
さらに、ホットスタンピング技術は成形時の寸法精度が高く、部品の一貫性を保つことができます。これにより、組み立て工程での誤差を減少させ、製品全体の品質向上にも寄与します。成形後のスプリングバック現象も最小限に抑えられるため、高精度の部品が安定して供給されます。
このように、ホットスタンピング技術と超高強度鋼板の組み合わせは、自動車産業における軽量化と安全性の両立に大きく貢献しています。自動車メーカーにとって、この技術の活用は不可欠であり、今後の技術革新とともにさらに進展していくことが期待されます。
環境への配慮:冷間プレス工法との比較
製造業において環境への配慮は重要な課題であり、ホットスタンピング技術と冷間プレス工法の環境影響の比較はその一環です。冷間プレス工法は、材料を常温で成形する方法であり、エネルギー消費が少ない点が利点です。しかし、高強度材料の成形には限界があり、成形性や寸法精度の面で課題が残ります。
一方、ホットスタンピング技術は、鋼板を高温に加熱し成形するため、エネルギー消費が大きいとされます。しかし、超高強度鋼板を効率的に成形できるため、最終製品の軽量化に寄与します。軽量化された車両は燃費が向上し、CO2排出量の削減につながるため、長期的には環境負荷の低減に貢献します。
例えば、冷間プレス工法では高強度の超ハイテン材の成形が難しく、成形荷重やスプリングバックの課題があります。しかし、ホットスタンピング技術を用いることで、これらの課題を克服し、複雑な形状の部品でも高精度に成形できます。これにより、製品の品質向上とともに、製造工程の効率化が図られます。
また、ホットスタンピング技術は、部分非焼入れ技術などの先進的な手法を取り入れることで、エネルギー効率を向上させています。部分非焼入れ技術により、必要な部分のみを加熱・冷却するため、全体のエネルギー消費を削減できます。これにより、環境負荷を低減しつつ、高性能な部品の製造が可能となります。
環境への配慮という観点からも、ホットスタンピング技術は重要な役割を果たしています。短期的にはエネルギー消費が大きいものの、長期的な視点で見ると、軽量化と高性能化を通じて環境負荷の低減に寄与する技術であると言えます。この技術のさらなる発展と普及が、持続可能な製造業の実現に向けた重要な鍵となるでしょう。
未来の展望:ホットスタンピング技術の可能性
ホットスタンピング技術は、その革新性と多様な応用可能性により、製造業の未来を大きく変える可能性を秘めています。この技術の発展により、今後さらに多くの産業分野での活用が期待されています。特に、自動車産業以外にも、航空宇宙産業、家電製品、建設機械などの分野での応用が進むでしょう。
まず、航空宇宙産業においては、軽量化と高強度化が求められるため、ホットスタンピング技術の適用は非常に有望です。航空機の構造部品において、この技術を用いることで、飛行機の全体重量を削減し、燃料効率を向上させることが可能です。また、耐久性の高い部品を製造することで、メンテナンスコストの削減にも寄与します。
次に、家電製品の製造においても、ホットスタンピング技術は重要な役割を果たします。薄型で高強度の金属部品を製造することで、製品の軽量化と耐久性を両立させることができます。特に、スマートフォンやノートパソコンの筐体など、精密かつ頑丈な部品が求められる分野での応用が期待されています。
さらに、建設機械や大型インフラの分野でも、ホットスタンピング技術は活用されています。これらの分野では、非常に高い強度と耐久性が必要とされるため、ホットスタンピング技術により製造された部品が求められます。例えば、クレーンや掘削機の部品にこの技術を適用することで、安全性と効率性を高めることが可能です。
ホットスタンピング技術の未来の展望には、技術的な進化も含まれます。例えば、AIと機械学習を組み合わせたスマート製造プロセスの導入により、成形プロセスの最適化と品質向上が図られます。リアルタイムでのプロセスモニタリングとデータ解析により、製造の精度と効率が飛躍的に向上するでしょう。
総じて、ホットスタンピング技術は、多くの産業分野での革新をもたらし、未来の製造業をリードする重要な技術です。その可能性を最大限に引き出すためには、継続的な研究開発と新しい応用分野の探索が不可欠です。この技術の進化が、持続可能で効率的な製造プロセスを実現し、産業全体の競争力を高めることに繋がるでしょう。
まとめ
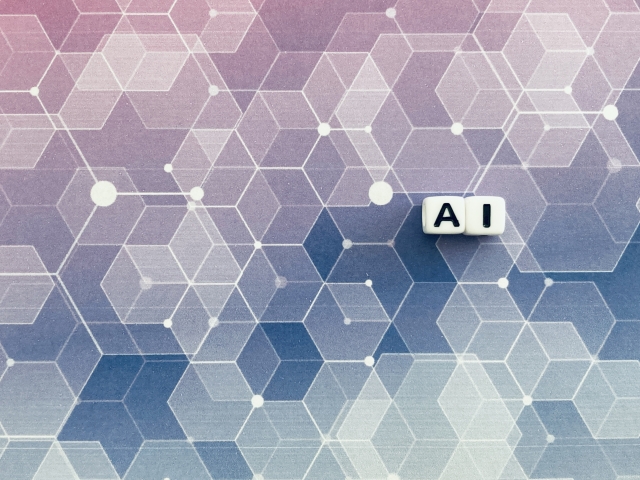
ホットスタンピング技術は、超高強度鋼板の成形と軽量化を実現するための革新的な技術です。高温での成形と急速冷却により、鋼板は高い強度を持ち、複雑な形状の部品でも高い寸法精度を保つことができます。この技術は、自動車産業をはじめ、航空宇宙、家電製品、建設機械など多くの分野で応用が進んでいます。
自動車産業においては、軽量化と衝突安全性の両立が重要な課題であり、ホットスタンピング技術はこれに大きく貢献しています。部分非焼入れ技術の導入により、特定の部位のみを高強度化し、生産効率と部品性能を同時に向上させることが可能となりました。また、環境への配慮としても、冷間プレス工法と比較して長期的な環境負荷の低減が期待されています。
ホットスタンピング技術の未来には、AIや機械学習を活用したスマート製造プロセスの導入が含まれ、さらに効率的で高品質な製造が実現されるでしょう。この技術は、持続可能な製造業の実現と産業全体の競争力向上に寄与する重要な要素であり、今後の発展が非常に期待されます。