2025年を目前に控え、製造業界ではスマートファクトリーへの関心が急速に高まっています。
AIとIIoTの技術革新が進む中、各企業は競争力を強化するための新たな戦略を模索しています。
本記事では、生成AIによる自動化技術やリーダーシップの重要性を踏まえ、スマートファクトリーがもたらす未来を探ります。
次世代工場への進化を促すAIとIIoTの融合
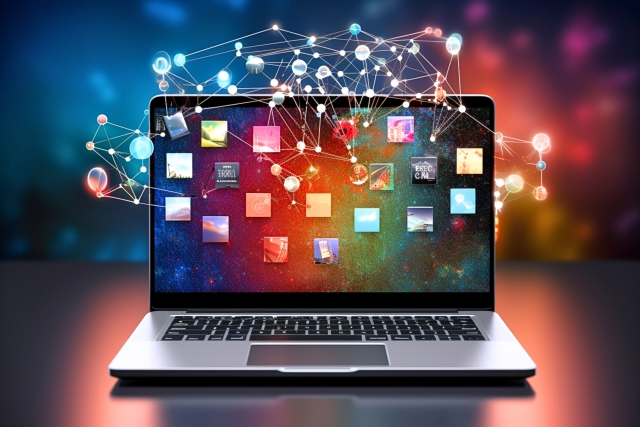
2025年に向けて、製造業の競争力を高めるためには、AI(人工知能)とIIoT(産業用IoT)の融合が欠かせません。これまで個別に発展してきたこれらの技術が、スマートファクトリーの実現に向けて一体化し、製造プロセス全体の効率を劇的に向上させています。
AIの進化は、製造現場におけるデータ解析や意思決定の迅速化を可能にしました。たとえば、AIがリアルタイムで生産ラインのデータを解析し、不具合の予兆を察知することで、ダウンタイムを未然に防ぐことができます。このように、AIの導入は生産性の向上だけでなく、製造品質の維持・向上にも寄与します。
一方、IIoTは、製造機器やシステムをネットワークでつなぎ、データの共有と管理を容易にします。これにより、製造プロセス全体の可視化が進み、各工程の最適化が実現します。さらに、IIoTによって収集されたデータは、AIによる高度な分析を受け、より精度の高い生産計画や予測が可能となります。
AIとIIoTの融合は、単なる技術革新にとどまらず、製造業全体のビジネスモデルの変革をもたらしています。従来の「モノづくり」から「コトづくり」へのシフトが進む中、データ駆動型の生産モデルが新たな価値を創出しているのです。この進化に対応するためには、企業は柔軟かつ迅速な意思決定が求められます。
このように、AIとIIoTが融合することで、製造業は次世代のスマートファクトリーへと進化を遂げています。これからの製造業は、これらの技術をいかに効果的に活用できるかが、競争優位性のカギとなるでしょう。
生成AIが変える製造業の未来:PLC制御プログラムの自動化
生成AI(Generative AI)の進化が、製造業においても大きな変革をもたらしています。特に注目されているのが、PLC(プログラマブルロジックコントローラー)制御プログラムの自動生成です。この技術により、これまで専門技術者が手作業で行っていた制御プログラムの作成が、AIによって瞬時に、しかも高精度に実行されるようになります。
従来、PLCのプログラムは高い専門知識が必要とされ、多くの時間とコストがかかっていました。しかし、生成AIは膨大なデータと過去のプログラム事例を学習し、それを基に最適な制御プログラムを自動で生成します。これにより、プログラム作成にかかる時間が大幅に短縮されるだけでなく、エラーの発生率も低減されます。
また、生成AIはプログラムの修正や最適化も自動で行うことができ、システムのアップデートや変更が必要な場合にも迅速に対応できます。これにより、製造現場での柔軟な対応が可能となり、生産ラインの稼働率を最大限に高めることができます。
さらに、生成AIの導入は、製造業全体の人材不足問題の解消にも寄与します。高度なプログラム作成能力を持つ技術者が不足している中、AIがその役割を担うことで、技術者の負担を軽減し、より戦略的な業務に集中できるようになります。
生成AIによるPLC制御プログラムの自動化は、製造業の効率化だけでなく、競争力の向上にも大きな影響を与えるでしょう。この技術の普及が進むことで、製造業はさらに進化し、新たなステージへと突入していくことが予想されます。
スマートファクトリー成功のカギ:リーダーシップとデータ駆動型意思決定
スマートファクトリーを成功させるためには、技術だけでなく、強力なリーダーシップとデータ駆動型の意思決定プロセスが必要です。これらは、製造業が直面する複雑な課題に対処し、競争力を維持するために不可欠な要素です。
リーダーシップは、組織全体に変革をもたらす原動力です。スマートファクトリーの導入においては、経営層がビジョンを明確にし、その実現に向けた道筋を示すことが求められます。これにより、従業員が共通の目標に向かって一体となり、技術導入がスムーズに進みます。さらに、リーダーシップは変化への抵抗を和らげ、組織文化の変革を促進します。
一方、データ駆動型の意思決定は、製造プロセスの最適化において重要な役割を果たします。スマートファクトリーでは、大量のデータがリアルタイムで生成されますが、それを効果的に活用するためには、データ分析に基づいた迅速な意思決定が必要です。データ駆動型のアプローチにより、無駄なコストやリスクを最小限に抑えながら、生産性を最大化することが可能です。
加えて、データの可視化と共有が進むことで、現場レベルから経営層までが同じ情報を共有し、より一貫性のある意思決定が可能となります。これにより、組織全体が連携しやすくなり、迅速な対応が可能となります。結果として、スマートファクトリーの導入は単なる技術革新にとどまらず、組織全体の競争力を大幅に向上させることが期待されます。
ドイツ発・インダストリー4.0の最新動向とその影響
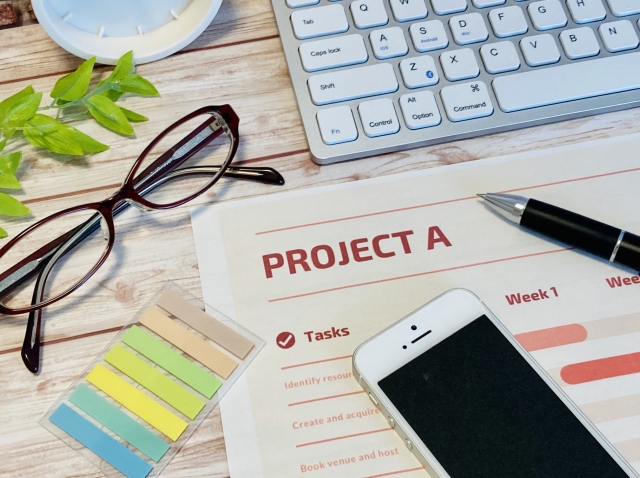
ドイツが主導するインダストリー4.0は、製造業界における第四次産業革命として世界中の注目を集めています。特に、データ連携を中心とした高度な生産システムの実現を目指すこのプロジェクトは、各国の製造業に大きな影響を与えています。
インダストリー4.0の中心にあるのは、「スマートファクトリー」の概念です。これは、製造設備がネットワークを通じて相互に連携し、リアルタイムでデータを共有・解析することで、生産効率を最大化することを目的としています。この取り組みは、AIやIIoTなどの先端技術を活用して、生産プロセスの最適化を図るものです。
また、ドイツ政府はインダストリー4.0の推進にあたり、標準化と国際連携を重視しています。これにより、異なるメーカーのシステムや機器がシームレスに連携できる環境が整い、グローバルな製造ネットワークが構築されつつあります。この動きは、製造業界全体に新たな競争原理をもたらし、各企業がこの潮流に乗ることを求められるようになっています。
さらに、インダストリー4.0は、ドイツ国内にとどまらず、他国にも大きな影響を及ぼしています。日本や米国をはじめとする先進国では、これをモデルにした独自のスマートファクトリー戦略が展開されており、製造業の革新が進んでいます。このように、インダストリー4.0は世界的な製造業の変革の波を生み出し、その影響は今後も拡大し続けるでしょう。
日本企業が取り組むべきスマートファクトリー戦略の最適解
日本の製造業が世界市場で競争力を維持するためには、スマートファクトリーへの移行が不可欠です。しかし、その導入には一律の解決策が存在せず、各企業の特性や市場環境に応じた戦略が求められます。
まず、既存の生産ラインや設備を最大限に活用しながら、スマートファクトリーへの移行を進めることが重要です。多くの日本企業は、長年にわたって培ってきた熟練の技術と高度な製造ノウハウを持っています。これらをデジタル技術と組み合わせることで、効率化だけでなく品質向上や生産性の向上も実現できます。
次に、データの利活用を戦略的に進めることが求められます。製造現場から収集される大量のデータを適切に分析・活用することで、予防保全や最適な生産計画が可能となります。特に、AIとIIoTを活用したデータ解析は、生産プロセスの隠れた問題を発見し、迅速に対応することを可能にします。
さらに、従業員のスキルアップと組織全体のデジタル化への適応も欠かせません。スマートファクトリーの導入は、技術だけでなく人材のスキルにも依存しています。日本の製造業が強みとする「人材力」をさらに高めるために、デジタルスキルの向上や、新しい技術を活用した生産プロセスの教育が必要です。
最後に、国内外のパートナーシップを強化し、オープンイノベーションを推進することも重要です。他企業や大学、研究機関との連携を通じて、新しい技術やアイデアを取り入れ、スマートファクトリーの導入を加速させることができます。このような多角的なアプローチが、日本企業にとっての最適なスマートファクトリー戦略を形作るのです。
2025年に向けた国際標準化と連携強化の重要性
スマートファクトリーの進展には、技術の進化だけでなく、国際的な標準化と連携の強化が重要です。特に、グローバルなサプライチェーンにおいては、異なる企業や国のシステムがシームレスに連携することが求められます。このため、標準化されたプロトコルやデータフォーマットの採用が急務となっています。
国際標準化は、製造業全体の効率を高めるだけでなく、技術の普及と互換性を確保するためにも不可欠です。たとえば、IIoTにおいては、異なるメーカーの機器が相互に通信し、データを共有できることが重要です。このため、国際的な標準に基づいた技術が採用されることで、グローバルな製造ネットワークの構築が可能となります。
また、標準化を進めることは、各国間の技術格差を埋め、競争の公平性を保つためにも重要です。特に、日本がリードする技術分野では、国際標準の策定に積極的に関与し、自国の技術がグローバルスタンダードとなるよう働きかけることが求められます。これにより、日本の製造業が国際市場での競争力を維持・強化することが可能となります。
さらに、国際的な連携強化も、スマートファクトリーの普及には欠かせません。各国の企業や研究機関と連携し、技術の共有や共同開発を進めることで、技術革新を加速させることができます。このような連携は、新しい市場の開拓や既存市場でのシェア拡大にもつながります。
標準化と連携強化は、スマートファクトリーを実現する上での土台となる要素です。これらを積極的に推進することで、2025年に向けた製造業の競争力を大幅に向上させることが期待されます。
成功事例から学ぶスマートファクトリー導入の実践ポイント
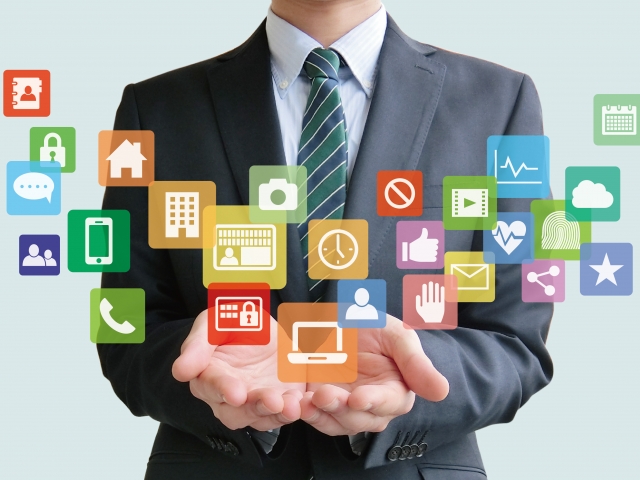
スマートファクトリーの導入は、単なる技術導入にとどまらず、製造プロセス全体の改革を伴います。成功事例から学ぶことで、導入時の具体的なポイントや課題を理解し、効果的なアプローチを取ることが可能です。
まず、成功している企業の多くが共通しているのは、小規模なパイロットプロジェクトからスタートしている点です。全体のシステムを一気に切り替えるのではなく、一部の生産ラインや工程でテストを行い、その成果を評価します。このアプローチにより、リスクを最小限に抑えながら、スマートファクトリーの有効性を検証することができます。
次に、社内の多部門との連携が重要です。製造部門だけでなく、IT部門や品質管理部門、さらには経営層と密接に協力し、全体的な戦略としてスマートファクトリーの導入を進める必要があります。このようなクロスファンクショナルなアプローチにより、導入プロセス全体がスムーズに進行し、各部門が一貫した目標を共有できるようになります。
さらに、データの収集と活用が成功の鍵となります。スマートファクトリーでは、製造現場からのリアルタイムデータを活用して、予防保全や生産最適化を図ります。しかし、データの質が低ければ、誤った判断を導くリスクが高まります。成功事例では、データの正確性と一貫性を確保するための仕組みが整えられており、これにより精度の高い意思決定が可能となっています。
また、外部パートナーとの協力も欠かせません。技術提供者やコンサルタントと連携し、最新技術の導入やトレンドを取り入れることで、スマートファクトリーの導入を加速させることができます。これにより、社内にない専門知識を補完し、導入リスクを軽減することができます。
これらのポイントを押さえた企業は、スマートファクトリーの導入によって、効率性の向上やコスト削減を実現し、競争力を大幅に強化しています。成功事例を参考に、戦略的な導入を進めることが、今後の製造業の成長にとって重要なステップとなるでしょう。
まとめ
2025年を見据えた製造業の競争力強化には、AIとIIoTを中心としたスマートファクトリーの導入が不可欠です。これにより、従来の生産プロセスが進化し、より効率的かつ柔軟な生産体制が実現されます。企業は、技術導入に留まらず、リーダーシップやデータ駆動型の意思決定を強化することが求められます。
また、国際標準化と連携強化は、スマートファクトリーの成功にとって重要な要素です。これにより、グローバルなサプライチェーンにおける競争力が向上し、製造業全体の生産性が向上します。さらに、成功事例から学び、実践的な導入ポイントを押さえることで、スマートファクトリーの導入リスクを軽減し、効果的な展開が可能となるでしょう。
このように、スマートファクトリーの進化は、技術、組織、戦略の全てにおいて革新を求められます。2025年に向けた競争力を確立するために、今からの取り組みが将来の成果に繋がるのです。