2025年に向けて、3Dプリント技術は航空部品の製造において革命的な変化をもたらしています。従来の製造方法では困難だった複雑な部品の生産が可能になり、軽量化やコスト削減が実現される時代が到来しています。特に航空機メーカーや防衛産業において、3Dプリントの活用が広がり、業界全体に新たなトレンドが形成されつつあります。
本記事では、最新の市場動向と技術革新について詳しく解説し、2025年以降の3Dプリント航空部品の未来を展望します。
イントロダクション:3Dプリント技術の進化と航空部品製造の未来
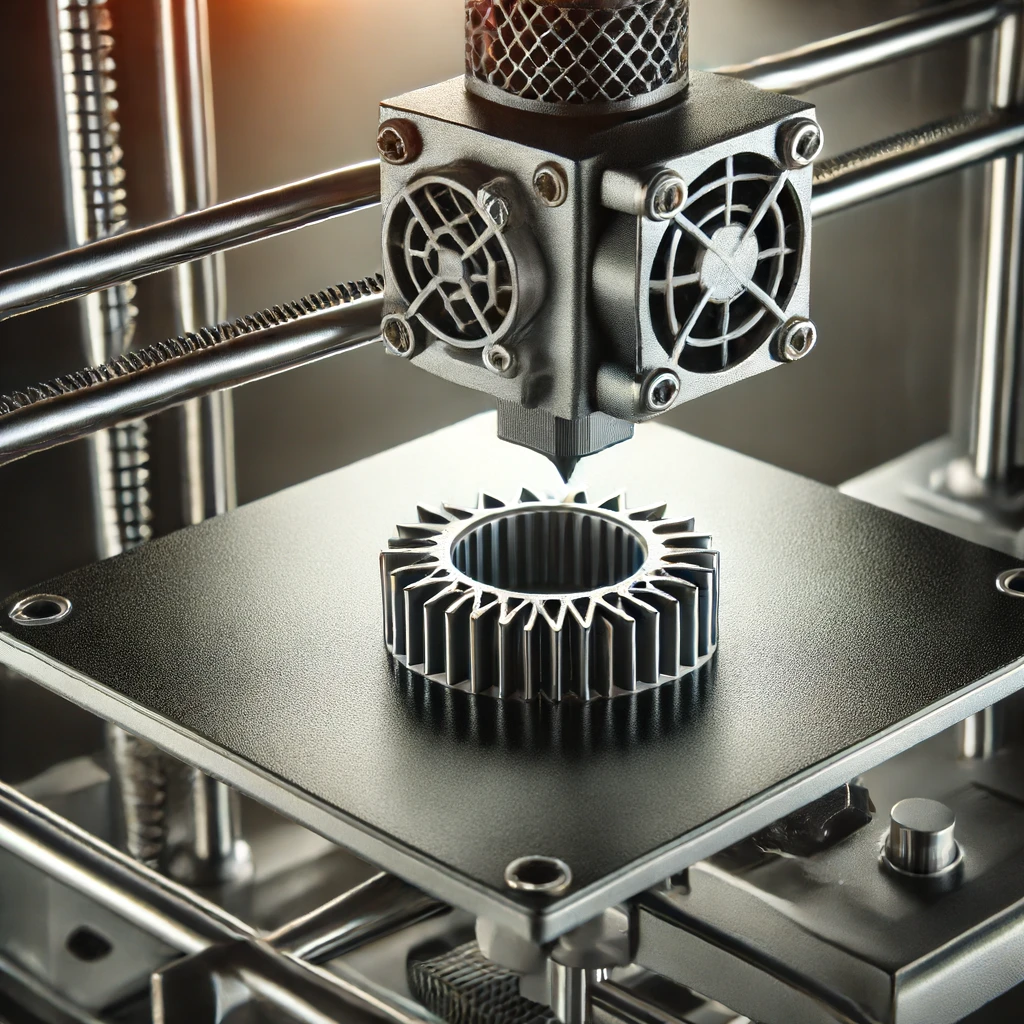
3Dプリント技術は、製造業全体において大きな変革をもたらしていますが、特に航空部品の製造においてはその影響が顕著です。従来の削り出しや鋳造に依存していた複雑な形状の部品が、3Dプリント技術により短期間で高精度に製造できるようになりました。この技術の進化により、航空業界では新しい設計の自由度が得られ、従来の製造制約から解放されています。
たとえば、従来ならば何十もの部品を組み合わせて作らなければならなかった部品が、3Dプリンターで一度に成形されることで、製造工程の簡素化とコスト削減が実現しています。
さらに、3Dプリントは素材の使用効率も向上させています。従来の削り出し加工では、素材の多くが無駄になっていましたが、3Dプリントでは必要な部分のみを正確に積層するため、廃材を大幅に削減できます。この特性は、特に高価なチタンや特殊合金など、航空機部品に用いられる高価な素材において大きなメリットを生み出しています。加えて、軽量化が求められる航空機設計において、3Dプリントによる部品は従来の製造方法に比べて軽量でありながら、強度を維持することが可能です。
また、3Dプリント技術の進化は、製造時間の短縮にもつながっています。従来は数週間かかっていた部品の製造が、数日、あるいは数時間で完了することも珍しくありません。これにより、航空機の開発サイクルが短縮され、新しい技術やデザインの迅速な導入が可能になりました。特に、エアバスやボーイングなどの大手メーカーは、こうした技術を積極的に取り入れることで、製造コストの削減と生産性の向上を実現しています。
3Dプリントの市場成長予測:2025年の見通し
航空宇宙分野における3Dプリント市場は、2025年までに急速な成長が見込まれています。市場調査によると、3Dプリント市場全体は2025年には約250億ドルに達すると予測されており、特に航空部品の製造においては重要な役割を果たしています。
従来の製造方法では高額な設備投資と長期間の生産計画が必要でしたが、3Dプリント技術の導入により、これらのコストが大幅に削減され、より迅速な生産体制が可能となりました。特に、航空機エンジン部品や機体構造における3Dプリントの活用は、製造工程の効率化において大きな効果を上げています。
また、2025年までに航空部品の製造における3Dプリントのシェアはさらに拡大すると見られています。これは、軽量化や燃費効率の向上が求められる中で、3Dプリントがその要件に応えられる技術だからです。航空業界においては、重量の削減が直接的にコスト削減につながるため、3Dプリント技術による軽量かつ高強度な部品がますます重要視されています。
さらに、アディティブ・マニュファクチャリングの導入は、サプライチェーン全体においても柔軟性をもたらしており、必要な部品を必要な時に製造できる体制が整いつつあります。
2025年までに中国やインドなどの新興市場においても3Dプリント技術の導入が加速し、これらの国々の航空宇宙産業が急速に成長することが期待されています。特に中国では、政府主導の製造業強化政策「メイド・イン・チャイナ2025」の一環として、航空機製造における3Dプリント技術の採用が積極的に進められています。
航空業界における3Dプリントの主な利用分野
3Dプリント技術は、航空業界においてさまざまな分野で活用されています。特にエンジン部品や構造部品の製造においては、その効率性と精度の高さから注目を集めています。航空機エンジンは非常に高い温度や圧力に耐える必要があるため、従来の製造方法では複雑で高コストな部品が多く存在していました。しかし、3Dプリント技術を使用することで、これらの部品は一体成型が可能となり、製造工程の簡素化や材料コストの削減が実現されています。
さらに、3Dプリントは航空機の内装部品の製造にも適用されています。例えば、座席やキャビン内の装飾パーツは、従来のプラスチック成型技術よりも軽量で耐久性のある素材を使用し、カスタマイズが容易です。この技術により、航空会社は顧客の要望に応じたデザインを実現しやすく、また航空機全体の重量を軽減することで燃費効率の向上も期待されています。
加えて、3Dプリントはスペアパーツの生産にも適しており、特定の部品を必要なときに即座に製造できるため、航空会社の保守や修理において大きなメリットをもたらしています。これにより、長期間の在庫管理が不要となり、コストの削減やリードタイムの短縮が可能になります。これらの利用分野において、3Dプリントは従来の製造技術に比べて圧倒的な効率性を誇り、今後も広範囲での導入が進むと見られています。
大手航空機メーカーの3Dプリント導入事例
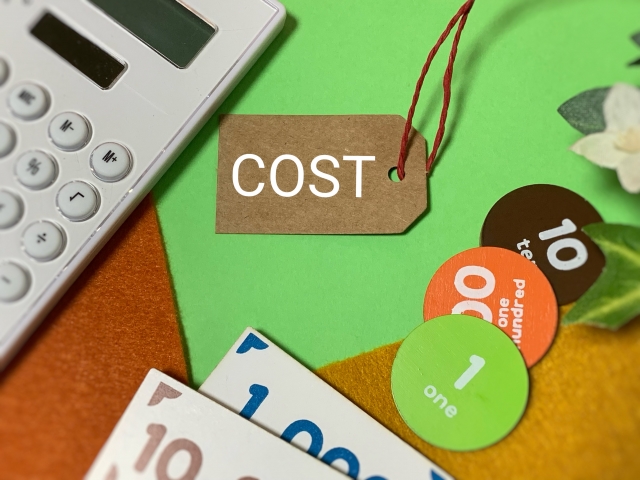
大手航空機メーカーは、3Dプリント技術を積極的に導入し、その利点を最大限に活用しています。特にエアバスやボーイングなどの企業は、自社製品の革新を進めるために3Dプリントを活用し、製造プロセスの効率化を図っています。エアバスは、自社のA350 XWBに3Dプリントされた1000点以上の部品を導入しており、これにより部品の軽量化とコスト削減を実現しました。これらの部品は、機体の内装からエンジン部品に至るまで、多岐にわたる分野で使用されています。
ボーイングも同様に、3Dプリント技術を採用しており、特に最新のB777X型機においては、GE製エンジンの燃料ノズルやセンサー、タービンブレードなどに3Dプリント部品が使用されています。これにより、エンジンの性能向上や燃費効率の改善が図られています。これらの取り組みは、航空機全体のパフォーマンス向上に貢献するとともに、将来的な維持管理コストの削減にもつながっています。
また、スペアパーツの即時製造という点でも3Dプリントは有効です。ボーイングは、必要なパーツを必要な場所で迅速に製造できる体制を整えており、これにより航空機の修理やメンテナンスにかかるダウンタイムを大幅に短縮しています。これらの事例は、3Dプリント技術が航空機製造業界にとって不可欠な技術であることを示しており、今後も多くの航空機メーカーが導入を進めていくと予想されています。
金属3Dプリント技術の革新とその応用
金属3Dプリント技術は、航空部品製造における革新的な技術として大きな注目を集めています。従来の金属加工技術では不可能だった複雑な形状や微細な構造を実現できることから、航空機エンジンや機体構造部品などの製造で広く活用されています。特に、軽量化と高強度が求められる航空機部品において、この技術は極めて有効です。金属3Dプリントは、粉末金属を層状に積み上げることで製造するため、無駄な素材を削減し、必要な部分だけを精密に成形することが可能です。
エアバスやボーイングなどの主要航空機メーカーは、3Dプリント技術を活用し、エンジン部品や構造材の製造を効率化しています。たとえば、GE製のエンジンに使用されている燃料ノズルは、金属3Dプリントによって一体成形されており、従来の製造方法に比べて軽量で高耐久な部品となっています。また、エンジン内部で使用されるタービンブレードも、複雑な冷却構造を持つ3Dプリント部品として製造されており、エンジンの性能向上に大きく寄与しています。
金属3Dプリントの導入により、製造プロセスの迅速化と部品精度の向上が可能となり、これまでにないレベルの性能を持つ航空機部品が実現されています。 さらに、製造業者は必要な部品を必要なときに製造できるため、サプライチェーン全体の効率化も期待されています。金属3Dプリント技術は、今後さらに高度化し、航空機製造の未来を牽引する重要な技術としての位置付けを強固にしていくことでしょう。
軽量化とコスト削減:航空部品製造の新しい潮流
航空機製造において、軽量化とコスト削減は常に最重要課題とされています。これに対し、3Dプリント技術は革新的なソリューションを提供しており、特に航空機の燃費効率を改善するための軽量化に大きく貢献しています。従来の製造方法では、一つの部品を複数のパーツに分けて組み立てる必要がありましたが、3Dプリント技術を活用することで、複数のパーツを一体成形することが可能になり、部品数の削減や軽量化が実現されています。
航空業界で採用されている多くの3Dプリント部品は、従来の部品に比べて数十パーセントの軽量化を達成しています。特に、エンジン部品や機体構造部品においては、軽量化による燃費向上や運用コストの削減が顕著です。また、3Dプリントは材料の無駄を減らすことができるため、製造コストの削減にも寄与しています。これは、特に高価な素材が多く使用される航空部品において、非常に重要な要素です。
さらに、従来の製造方法では高額な型や治具が必要でしたが、3Dプリントではこれらのコストがかかりません。これにより、特に少量生産やプロトタイプ開発において、コスト効率が大幅に改善されています。航空業界では、軽量でありながら高強度を誇る部品が求められるため、3Dプリント技術は今後さらに広範囲にわたり採用され、製造工程全体の効率化が進むことが期待されています。
アディティブ・マニュファクチャリングのメリットと課題
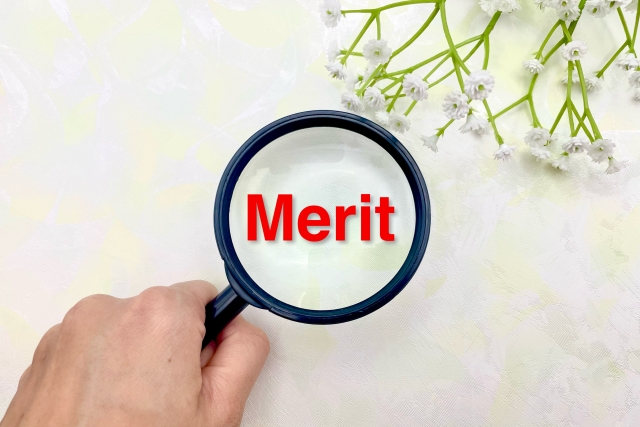
アディティブ・マニュファクチャリング(AM)は、従来の削減加工に対する革新技術として広く注目されています。その最大のメリットは、製造工程の自由度が大幅に向上し、設計の制約が減る点です。これにより、航空機の部品製造では、軽量化や複雑な構造の部品が容易に製造できるようになりました。特に、従来の製造方法では不可能だった複雑な内部構造を持つ部品が、AM技術により短期間で実現され、性能向上やコスト削減が進んでいます。
さらに、AM技術を使用することで、無駄な素材を削減し、必要な材料のみを使用して部品を成形することが可能です。この効率性の高さは、特に高価な素材を使用する航空部品製造において、重要なコスト削減効果をもたらしています。また、部品の即時生産が可能なため、在庫管理の手間やコストを削減できる点も、大きなメリットとされています。これは特にスペアパーツの製造において重要で、必要な部品を必要なタイミングで製造できるため、リードタイムが大幅に短縮されます。
一方で、AM技術の課題も存在します。たとえば、部品の品質が安定しない場合があり、特に高精度が求められる航空部品では、品質保証の基準が高く設定されています。また、3Dプリント技術そのものがまだ新しい分野であるため、技術の成熟度や標準化の遅れが進行の妨げとなることがあります。これらの課題を克服するためには、さらなる技術開発や業界内での協力が不可欠です。
中国・インド市場における3Dプリントの拡大
中国やインドは、航空宇宙分野における3Dプリント技術の導入を急速に進めている地域の一つです。特に中国では、政府主導の「メイド・イン・チャイナ2025」計画の一環として、3Dプリント技術の採用が航空産業において積極的に推進されています。この計画により、中国の航空機メーカーは、国内で開発された技術を活用し、独自の航空機製造技術を強化しています。たとえば、C919ナローボディ機では、3Dプリントによって製造された部品が多く採用され、機体全体の軽量化と性能向上が実現しています。
インドもまた、航空宇宙分野における3Dプリント技術の導入に力を入れています。特に、インド宇宙研究機関(ISRO)やインド海軍、空軍などが、3Dプリント技術を活用した部品の製造を進めており、防衛分野でもその応用が広がっています。バンガロールやチェンナイなどの主要都市では、航空機用のスペアパーツや重要な機体部品が3Dプリント技術を活用して製造されており、これにより迅速な供給とコスト削減が実現されています。
さらに、インドでは新興企業も次々と登場し、航空宇宙分野での3Dプリント技術の研究開発が盛んに行われています。これにより、国内の製造能力が強化され、外国への依存度が低減されるとともに、自国の航空産業の競争力が向上しています。中国やインドの市場拡大は、今後さらに3Dプリント技術の普及を加速させ、世界的な航空部品製造のトレンドに影響を与えることが期待されています。
3Dプリント技術の未来:持続可能な航空機製造
3Dプリント技術は、持続可能な航空機製造において重要な役割を果たしています。従来の製造方法では、素材の無駄やエネルギー消費が大きな課題となっていましたが、3Dプリント技術はこれらの問題を解決する手段として期待されています。積層造形による製造は、必要な部分にのみ素材を使用し、従来の削り出しや鋳造に比べて廃棄物を大幅に削減することができます。この点は、特に高価な素材を使用する航空機部品製造において、大きなメリットを生んでいます。
また、3Dプリントによって製造される部品は、軽量でありながら高い強度を持つため、燃料消費の削減にもつながります。軽量化された航空機は、より少ない燃料で飛行でき、二酸化炭素排出量の削減に貢献します。さらに、従来の製造方法では複数の部品を組み合わせる必要があった複雑な構造も、3Dプリントでは一体成形が可能なため、製造工程の簡素化と効率化が実現されています。この技術は、サプライチェーンの短縮にもつながり、航空機製造の全体的な環境負荷を低減する要因となっています。
今後、3Dプリント技術は再生可能エネルギーやリサイクル素材を組み合わせた製造プロセスと統合されることで、さらに持続可能性を高める可能性があります。航空業界全体がカーボンニュートラルを目指す中で、3Dプリント技術はその実現に不可欠な要素となりつつあります。こうした技術的進化により、航空機製造業界は環境に配慮した製造手法をさらに進化させることが求められています。
航空宇宙業界での3Dプリントと防衛分野への波及効果
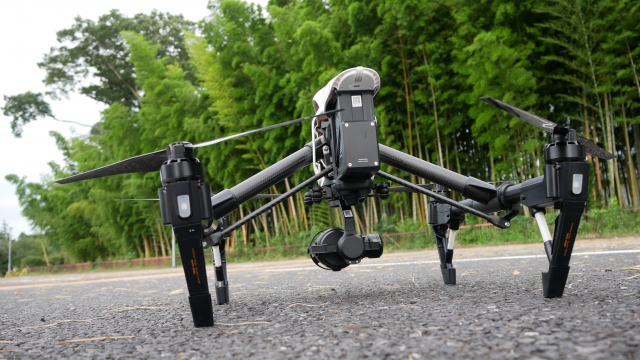
航空宇宙業界において、3Dプリント技術は急速に普及し、防衛分野にもその影響が広がっています。航空機の部品製造で培われた技術は、軍用機やミサイルシステムなどの製造にも応用され、防衛分野における製造プロセスの効率化とコスト削減が進んでいます。特に、軽量で強度の高い部品が求められる戦闘機やドローンの設計において、3Dプリント技術は大きな効果を発揮しています。
防衛分野では、従来の製造方法に比べて短期間で必要な部品を製造できる点が重視されています。3Dプリントは、急速に変化する戦略環境に対応するため、柔軟な生産体制を提供します。これにより、必要なタイミングで即時に部品が供給できるため、部隊の即応性が向上し、長期にわたる部品在庫の管理コストも削減されます。特に、戦闘機の修理やメンテナンスにおいて、現場で迅速に部品を製造できる能力は大きなアドバンテージとなっています。
さらに、3Dプリントは複雑な形状や内部構造を持つ部品の製造にも適しており、ミサイルの先進的な設計や防衛システムの改善に寄与しています。これにより、従来の製造技術では不可能だった新しいデザインや機能を持つ防衛装備が実現可能となっています。今後、防衛分野における3Dプリント技術の導入は、さらに広範囲にわたり普及し、新しい軍事技術の開発においても重要な役割を果たすと予想されます。
2025年以降の技術革新と予測される次のステップ
2025年以降、3Dプリント技術はさらなる進化を遂げると予測されています。特に、航空機製造における複雑な部品の一体成形技術が進展し、設計の自由度がさらに高まるでしょう。この技術革新により、製造業者は部品の軽量化や耐久性の向上を実現し、航空機の性能が飛躍的に向上することが期待されています。一方で、製造コストのさらなる削減とサプライチェーンの効率化も進み、航空業界全体の競争力が高まるでしょう。
また、次世代の3Dプリント技術として、複合材料の積層造形やマルチマテリアルプリントの研究開発が進んでいます。これにより、異なる材料を組み合わせた部品の製造が可能となり、軽量化と強度の両立がさらに進化します。この技術は、航空機だけでなく、宇宙開発や防衛分野にも広く応用され、極限環境に対応した新しい製品が開発されるでしょう。
さらに、デジタルツイン技術との連携も進むと見られています。3Dプリントによって製造された部品のリアルタイムなデータをデジタルで管理し、予知保全や設計の最適化が可能となるため、製造業者は迅速かつ効率的に新しい航空機を設計・製造することができるでしょう。
まとめ:2025年に向けた3Dプリント技術の展望
2025年に向けて、3Dプリント技術は航空部品製造においてますます重要な役割を果たすことが予想されます。従来の製造方法に比べ、3Dプリントは設計の自由度が高く、複雑な部品の製造が可能であり、軽量化とコスト削減を同時に実現する手段として広く普及しています。航空機メーカーはこの技術を活用し、エンジン部品や機体構造材の製造において革新を続けており、その結果、燃費効率の向上や性能の飛躍的な向上が期待されています。
また、金属3Dプリント技術の進化により、軽量かつ強度の高い部品が製造され、航空機の持続可能な製造方法としての位置づけが強固なものとなっています。これにより、航空業界全体がより環境に配慮した製造プロセスを採用することが可能になり、カーボンニュートラルに向けた取り組みが進んでいます。さらに、アディティブ・マニュファクチャリングのメリットは、防衛分野にも波及しており、戦闘機や軍用機における即応性の向上やコスト削減に貢献しています。
中国やインドなどの新興市場においても、3Dプリント技術の導入が急速に進んでおり、航空宇宙分野での競争力が一層高まることが予想されます。これらの国々では、政府の主導により、国内の航空機製造における自給自足の体制が強化されており、特にC919ナローボディ機の開発などでその成果が顕著です。今後も、3Dプリント技術の進展により、航空業界と防衛分野のさらなる成長が見込まれ、持続可能な製造革命が加速していくでしょう。