2025年、世界の自動車業界はさらなる軽量化を求めて革新を続けています。軽量化は、燃費向上や二酸化炭素排出削減だけでなく、電動化や自動運転技術との相乗効果も期待されています。
特に、高張力鋼板やアルミニウム、マグネシウムといった新素材の導入により、軽さと強度を兼ね備えた次世代の車が登場しています。これにより、安全性と効率性を両立した車づくりが実現されるでしょう。
自動車軽量化の重要性—環境と効率の両立
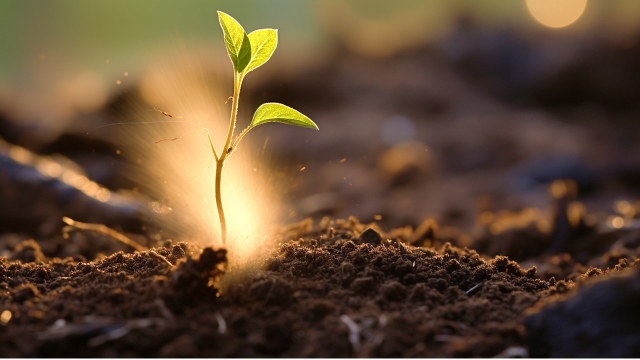
自動車の軽量化は、2025年に向けてますます重要視されています。自動車の重量が減少することで、燃費の向上や二酸化炭素排出量の削減が期待できるため、各国の環境規制に対応する上でも大きな意味を持ちます。特に、電動化が進む中で、車両全体の効率を高めるためには、バッテリーの重量を抑えることが重要です。バッテリーの重量は車両のパフォーマンスに直結し、航続距離や加速性能に大きな影響を与えます。
さらに、軽量化により自動車の運動性能も向上します。軽い車体はよりスムーズな加速や減速を可能にし、ハンドリングも向上します。これにより、ドライバーの運転体験が改善され、快適性や安全性が高まります。一方、軽量化にはコストや技術的な課題もありますが、2025年に向けた技術革新により、これらの問題が次第に解決されていくでしょう。
2025年には、燃費性能や環境負荷の低減を実現するだけでなく、より優れた走行性能を提供するための軽量化技術が、自動車業界において鍵となるでしょう。
2025年の自動車業界が求める軽量化技術とは
自動車業界では、軽量化技術が新たな競争力の源泉として注目されています。2025年に向けて、より効率的で持続可能な車両を製造するためには、従来の素材や製造プロセスに代わる新たなアプローチが求められています。
その中でも、高強度かつ軽量な材料の使用が特に注目されています。高張力鋼板やアルミニウム、マグネシウム、さらには炭素繊維強化プラスチック(CFRP)などの素材が、次世代の軽量化技術の中心となっています。
これらの新素材は、車体の剛性を維持しながら重量を削減するため、燃費性能の向上やCO2排出量の削減に貢献します。また、これらの素材は電動車のバッテリー重量を補完し、全体のバランスをとる上でも重要です。特にEV(電気自動車)やPHEV(プラグインハイブリッド車)においては、軽量化が車両の航続距離を大きく伸ばす要因となります。
自動車メーカーは、2025年の市場を見据え、これらの軽量素材の採用を加速しています。軽量化は、単なる技術革新ではなく、ビジネス戦略の一環として、サステナビリティや競争力強化を図る上で不可欠な要素となっています。
鋼鉄の進化—高張力鋼板の可能性
高張力鋼板は、自動車の軽量化における重要な素材の一つとして注目されています。この鋼材は、従来の鋼材に比べて大幅に強度が高く、それでいて軽量であるため、車体の剛性を保ちながら軽量化を実現することができます。2025年に向けた自動車産業において、特にEVやハイブリッド車での利用が拡大しています。
高張力鋼板は、車体の重要な構造部品に使用されることで、衝突安全性を維持しつつ、全体の車重を削減します。これにより、車両のエネルギー効率が向上し、結果として燃費の向上やCO2排出量の削減につながります。さらに、製造コストの面でも、他の軽量化素材に比べて比較的低コストであり、自動車メーカーにとってはコストパフォーマンスの高い選択肢です。
しかし、高張力鋼板の加工には高度な技術が必要であり、その加工プロセスが課題となっています。自動車メーカーは、より効率的でコストを抑えた加工技術の開発に取り組んでおり、2025年以降にはさらに性能が向上した高張力鋼板が普及することが期待されています。
軽量化を加速するアルミニウムとマグネシウムの活用
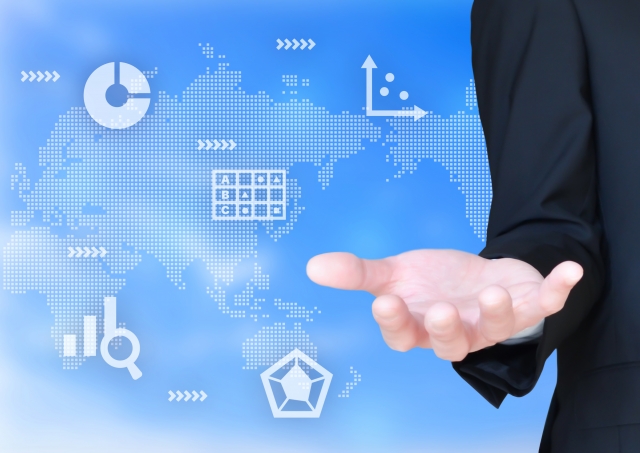
アルミニウムとマグネシウムは、自動車の軽量化において欠かせない素材です。特にアルミニウムは、従来の鋼材に比べて約30%も軽量であり、強度を保ちながら車体の重量を大幅に削減することができます。2025年に向けて、アルミニウムはエンジンブロックや車体フレームなど、重要な構造部品にますます採用されるようになっています。
一方で、マグネシウムはさらに軽量であり、鋼材に比べて75%も軽いことから、特定の部品においてはアルミニウム以上の軽量化効果が期待されています。しかし、マグネシウムは耐食性や加工の難しさが課題となっており、主に内部構造や細部の部品での利用に限られています。それでも、技術の進化により、これらの課題が解消されつつあり、より広範な用途での採用が進むと見込まれています。
アルミニウムとマグネシウムの活用は、車体の軽量化を加速させるとともに、燃費や環境性能を高めるための重要な手段となります。これにより、自動車メーカーは、環境規制に対応しつつ競争力を維持することが可能になります。
樹脂材料の新展開—未来の自動車構造の鍵
樹脂材料は、自動車の軽量化を促進する上で、鋼鉄やアルミニウムに代わる重要な選択肢として注目されています。特に、強度と軽さを兼ね備えたエンジニアリングプラスチックが車体の多くの部分に採用され始めています。これにより、重量削減のみならず、製造コストの削減や燃費の向上にもつながります。樹脂材料はまた、デザインの柔軟性も高め、自動車の内部構造や外装部品においても大きな役割を果たしています。
最近では、炭素繊維強化プラスチック(CFRP)やガラス繊維強化プラスチック(GFRP)といった高機能樹脂が、自動車産業においてますます重要な役割を果たしています。これらの素材は、高い剛性と耐久性を持ちながらも、軽量であるため、特に電動車両やハイブリッド車の構造に適しています。電動化が進む中で、これらの材料はバッテリーの負担を軽減し、全体の車両効率を向上させるために不可欠です。
さらに、リサイクル可能なバイオプラスチックの開発も進んでおり、持続可能性を意識した素材の使用が拡大しています。これにより、軽量化と環境配慮の両立が進み、次世代の自動車製造に新たな可能性が生まれています。
バイオプラスチックがもたらす持続可能な選択肢
自動車の軽量化と環境負荷の軽減を同時に達成するために、バイオプラスチックの活用が注目を集めています。バイオプラスチックは、植物由来の材料から作られており、石油ベースの従来のプラスチックに代わる持続可能な素材です。この素材は、従来の樹脂と同等の性能を持ちながら、製造過程での二酸化炭素排出量を大幅に削減できることが特徴です。
また、バイオプラスチックは、リサイクルが容易であることも重要なポイントです。自動車の製造から廃棄に至るライフサイクル全体での環境負荷を低減できるため、カーボンニュートラルを目指す自動車メーカーにとって、バイオプラスチックは魅力的な選択肢となっています。特に内装部品や一部の外装パーツでの利用が進んでおり、軽量で強度のある素材として多様な用途に応用されています。
バイオプラスチックの採用は、自動車産業の持続可能性を高め、未来の車両設計において軽量化と環境保護の両立を実現する重要な要素となるでしょう。これにより、今後さらに広範囲での利用が期待されています。
軽量化技術と電動化のシナジー効果
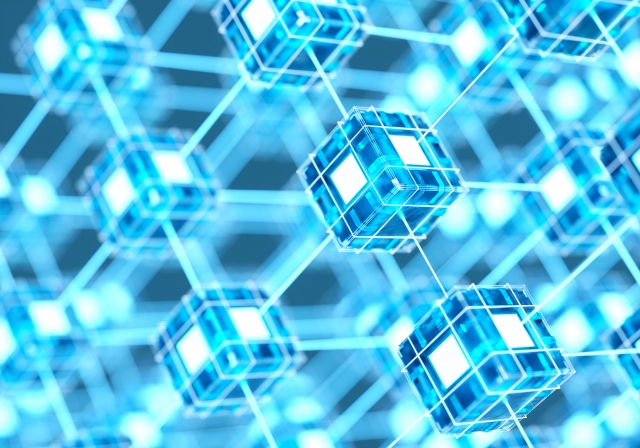
自動車の電動化と軽量化は、互いに相補完的な関係にあり、シナジー効果を生み出しています。電気自動車(EV)やプラグインハイブリッド車(PHEV)は、バッテリーの搭載により従来の内燃機関車両に比べて重量が増加する傾向があります。この重量を軽減するために、車体や構造部品の軽量化が重要となり、燃費や航続距離の向上に貢献します。
軽量化が進むことで、EVやPHEVのバッテリー容量を抑えつつ、より長い航続距離を実現することが可能となります。また、軽量化された車両は、電力消費の効率も向上し、充電インフラに対する負担も軽減されます。これにより、ユーザーにとってもコストパフォーマンスが向上し、電動車への移行が促進されるでしょう。
さらに、軽量素材の使用は、電動車両に求められる安全性や耐久性を損なわずに、車体設計の自由度を高めます。これにより、自動車メーカーはデザイン性と機能性を両立させた新しいモデルを展開することが可能となり、2025年に向けた競争力を強化することが期待されています。
自動車部品の脱炭素化とコスト削減の両立
自動車産業では、脱炭素化が大きな課題となっています。特に自動車部品の製造過程において、CO2排出量を削減しながら、コストを抑えることが求められています。軽量化技術は、この課題を解決する手段として注目されており、材料の選定や製造プロセスの見直しが進んでいます。例えば、高張力鋼板やアルミニウム、マグネシウムなどの軽量素材を活用することで、燃費向上に寄与し、結果としてCO2排出量の削減が可能となります。
脱炭素化を実現するためには、再生可能エネルギーの利用やエネルギー効率の高い製造設備の導入が必要です。また、部品自体のライフサイクル全体での環境負荷を減らすことが求められています。これにより、軽量化された部品は、製造時だけでなく使用時にもエネルギー消費を抑えることが可能となり、総合的なコスト削減に繋がります。
2025年に向けて、自動車メーカーは部品の脱炭素化と軽量化を両立させるために、革新的な技術と素材の開発を進めており、これが次世代自動車の競争力強化に直結するでしょう。
産学官連携による新素材開発の加速
2025年を見据えた自動車の軽量化に向けて、産学官連携による新素材の開発が急速に進んでいます。自動車産業においては、高性能かつ持続可能な軽量素材の需要が高まっており、その技術的課題を解決するためには、業界全体での協力が不可欠です。特に大学や研究機関、政府機関が参加することで、基礎研究から実用化までのプロセスが加速される傾向にあります。
高強度・軽量な新素材としては、ナノテクノロジーを駆使した複合材料や、より効率的な生産プロセスを可能にする樹脂材料が注目されています。これにより、車両の構造を根本から見直し、さらなる軽量化を実現することが可能になります。産業界では、これらの技術を商業化するために、特許取得や実証試験が進められており、2025年には多くの車両で新しい軽量素材が採用されると予想されています。
また、政府はこの分野への研究開発投資を支援しており、環境規制の強化に対応するためのインセンティブも設けています。このように、産学官が一体となって進める新素材開発は、自動車産業全体における競争力を高める重要な要素となっています。
軽量化と安全性のバランス—新しい規制の影響
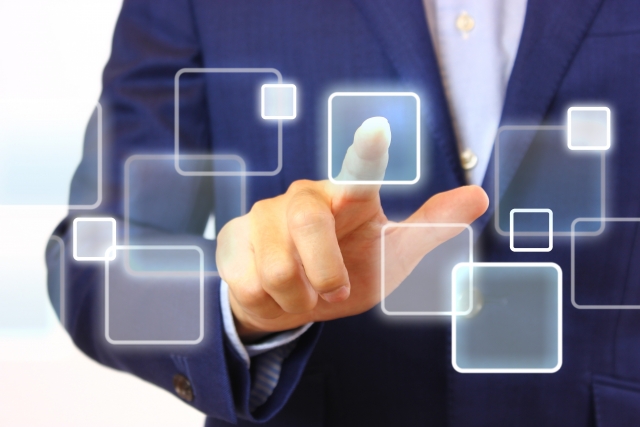
自動車の軽量化が進む一方で、安全性の確保も重要な課題として取り組まれています。軽量化によって燃費や走行性能が向上する一方で、衝突時の耐久性や車両全体の安全性を維持する必要があります。2025年には、世界各国でより厳しい安全基準が導入されることが予想されており、自動車メーカーはこのバランスをいかに取るかが大きな課題となっています。
高強度素材の導入や、クラッシャブルゾーンの最適化など、安全性を高めるための技術はすでに多くの車両に採用されています。特に、軽量でありながら衝突時のエネルギーを効率よく吸収する素材の開発が進んでおり、鋼材や複合材料がその中心となっています。また、アルミニウムやマグネシウムを用いた車体構造の改良も進められており、衝突時の乗員保護を重視した設計が求められています。
さらに、自動運転技術の進化により、事故回避性能も向上していますが、これにより車体の軽量化と安全性の両立がより一層求められるようになります。新しい安全規制が施行される中で、自動車メーカーは技術革新を通じてこの複雑な問題に対応していくことが必要となるでしょう。
軽量化によるドライビング体験の進化
自動車の軽量化は、ドライビング体験に大きな変化をもたらしています。軽量化された車両は、加速性能やハンドリング性能が向上し、よりダイナミックでスムーズな走行を実現します。特に、スポーツカーや高性能車では、軽量化による運動性能の向上が顕著であり、ドライバーにとっての操作性が格段に向上しています。
また、軽量化は燃費の向上にも貢献しており、エコドライビングが可能となることで、日常的な移動においても快適さを実感できるでしょう。電動車両やハイブリッド車においては、軽量化された車体が電力消費を抑えることで、航続距離の延長やエネルギー効率の向上にもつながります。これにより、都市部での短距離移動から長距離ドライブまで、幅広いシーンでメリットが生まれます。
自動車メーカーは、軽量化技術を取り入れた車両を多くラインナップに加えており、今後はさらに多くのドライバーがその効果を体感できるようになるでしょう。2025年以降、軽量化技術はドライビング体験を新たな次元へと押し上げる鍵となります。
まとめ—2025年以降の軽量化の展望
2025年を迎えるにあたり、自動車の軽量化技術は今後さらに進化し続けるでしょう。電動化の進展や環境規制の強化に伴い、より軽量でありながら高強度の素材が求められています。これにより、燃費の向上やCO2排出量の削減といった環境性能が向上するだけでなく、車両の運動性能や安全性も高められることが期待されています。
特に、アルミニウムやマグネシウム、樹脂素材の進化により、車両全体の軽量化が進み、自動車業界における競争力の強化に寄与します。また、産学官の連携による新素材開発や新しい安全基準への対応も、自動車メーカーにとっては重要な課題となるでしょう。軽量化は、次世代の自動車が環境に優しく、効率的であるための不可欠な要素として、今後もさらなる革新をもたらす分野です。