2025年の製造業は、AI、5G、IoTを駆使したスマート製造へと大きく変貌しています。世界のリーダー企業が示す成功事例は、日本企業にとっても今後の成長戦略の指針となるでしょう。
例えば、トヨタはAIを活用して「トヨタ生産方式(TPS)」を進化させ、生産の最適化と在庫の最小化を実現しています。さらに、BMWのデジタルツイン技術や、GEのIoTプラットフォーム「Predix」など、各企業は最新技術を導入して競争力を強化しています。
2025年の製造業は、効率性、柔軟性、環境配慮の全てを両立するための革新が求められます。持続可能な未来に向け、ビジネスパーソンとして今すぐ準備を整えましょう。
AIとIoTの統合がもたらす製造業のプロセス最適化
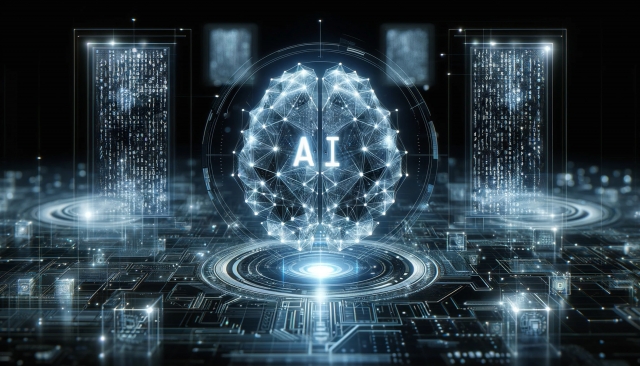
AIとIoTの組み合わせは、製造業の効率化に革命的な効果をもたらしています。IoTセンサーは工場内の設備からリアルタイムでデータを収集し、そのデータをAIが分析することで、生産ラインの最適化が進んでいます。例えば、温度や振動、圧力といった設備データを常時監視し、異常値を検出した場合には即座にAIがアラートを出し、予防保全のタイミングを自動提案します。
GEの産業用IoTプラットフォーム「Predix」は、このようなプロセス最適化の一例です。Predixは膨大な機器データをクラウドで分析し、製造ラインの効率を高めるための具体的な指示をリアルタイムで提供します。また、予知保全の機能により、故障の兆候を事前に察知し、設備の稼働率を最大化することが可能です。
これにより、工場全体の稼働状況が可視化され、無駄なエネルギー使用や生産停止が回避されます。さらに、AIは過去のトレンドを学習することで、需要の変動に合わせた最適な生産計画も提供します。こうした技術は、従来の生産プロセスにおけるダウンタイムや不良品率の削減に寄与しています。
5G通信の低遅延技術もAIとIoTの連携を促進する重要な要素です。リアルタイムのデータ転送が可能になることで、各設備の動作状況を即時に分析し、瞬時にフィードバックを行うことができます。これにより、製造プロセスはさらに効率化され、より迅速な対応が実現します。
トヨタ生産方式の進化:AIによるリアルタイム在庫管理と効率最大化
トヨタ自動車は、独自の「トヨタ生産方式(TPS)」をAIとIoT技術で進化させ、さらなる最適化を実現しています。TPSの基本理念である「ジャストインタイム」は、必要な物を必要な時に供給する仕組みですが、AIの導入により在庫管理がリアルタイムで行われ、さらなる効率化が進んでいます。
トヨタは、AIを用いて生産ラインから取得したデータを即座に分析し、需要予測と連動させるシステムを構築しています。このシステムにより、部品の欠品リスクを最小限に抑えることができ、供給チェーンの安定性が強化されています。また、IoTセンサーは各工場の生産状況をモニタリングし、稼働状況に応じて生産計画を自動調整します。
これにより、従来の在庫コストを大幅に削減し、不要な資源の浪費が抑えられています。トヨタのAIベースの在庫管理システムは、特に需要変動の激しい自動車産業において高い効果を発揮しています。
さらに、トヨタはAIによる品質管理も強化しており、製品の不良率を低減させています。生産過程で発生するわずかな異常も見逃さず、リアルタイムで修正する仕組みが導入されています。これにより、顧客満足度の向上とブランドの信頼性向上が期待されています。
トヨタの事例は、AIとIoTの統合が日本企業の生産方式にどのような変革をもたらすかを示す好例であり、他業界にとっても参考となるモデルです。
デジタルツイン技術を活用するBMWの先進的製造シミュレーション
BMWは、製造プロセス全体の効率化を目指し、デジタルツイン技術を積極的に導入しています。デジタルツインとは、物理空間の製品やプロセスを仮想環境上で再現する技術で、BMWはこれを活用して生産ラインの動作をシミュレートしています。新製品の導入前に仮想空間で試行錯誤を重ねることで、製品開発から市場投入までの期間を大幅に短縮することが可能になりました。
BMWの工場では、すべての機器やロボットがデジタルツインとして管理されています。これにより、設備の稼働率や消耗状態をリアルタイムで把握でき、機器のトラブルを未然に防ぐ予防保全を実現しています。生産ラインの再編や新たなロボットの導入も、仮想空間上でのシミュレーションにより、リスクを最小限に抑えつつ行われます。
さらに、BMWは複数の工場間のデータを統合し、グローバルな生産体制を最適化しています。例えば、異なる地域の工場で生じる需要の変動に即応するため、製造拠点間での生産調整が迅速に行われます。これにより、在庫管理が効率化され、コスト削減に貢献しています。
また、デジタルツインは品質管理の分野でも大きな成果を挙げています。生産中の部品や製品の状態をリアルタイムで監視し、微細な不良も見逃さずに即時修正する仕組みが整備されています。これにより、BMWは高品質の製品を安定的に市場へ供給することを実現しています。
GEの「Predix」プラットフォームが支える産業IoTの実力
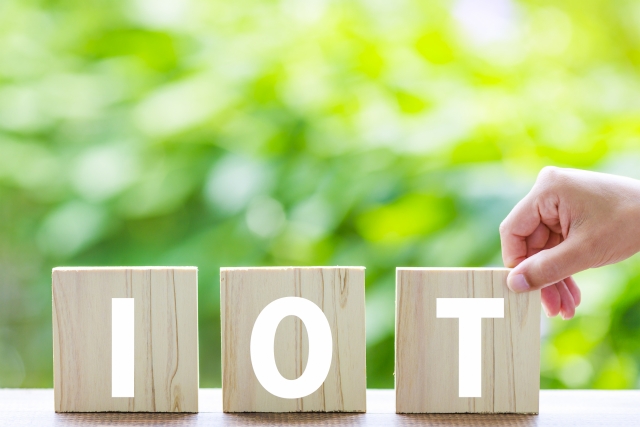
GEの「Predix」は、製造業における産業用IoTプラットフォームとして、工場のリアルタイム監視とデータ分析を支援しています。Predixは、各製造設備の状態やパフォーマンスを常時モニタリングし、最適な生産計画を導き出すためのデータを提供します。これにより、生産効率の向上だけでなく、予防保全の高度化も実現しています。
Predixは、機器の振動、温度、稼働時間など、さまざまなセンサーデータを一元管理します。AIアルゴリズムがこれらのデータを分析し、異常なパターンを検出すると即座にアラートが出され、メンテナンス担当者が迅速に対応できる仕組みが構築されています。これにより、機器の故障による生産停止を未然に防ぎます。
Predixは各設備のパフォーマンスを詳細に解析し、エネルギー消費を最適化することにも貢献しています。特にエネルギーコストが高騰する中、無駄な電力消費を抑えるための精密な制御が可能です。これにより、工場全体のコスト削減が促進されています。
さらに、Predixは工場間のデータを横断的に連携させ、サプライチェーン全体の効率化も支援します。各拠点の需要状況に合わせて生産を最適化することにより、在庫の最小化を実現し、供給の安定性を確保しています。Predixの活用により、GEは競争力のある製品を短期間で市場へ投入できる体制を構築しています。
中国の500スマート工場計画:5GとIoTで世界市場をリード
中国政府は「第14次五カ年計画」の一環として、2025年までに500か所のスマート工場を設立する大規模なプロジェクトを進行中です。これらの工場では、AI、5G、IoT、ビッグデータ、デジタルツインといった先端技術が活用され、製造業の生産性と品質向上が目指されています。
各スマート工場では、IoTセンサーが設備の稼働状態や生産ラインの進行をリアルタイムで監視し、5G通信の低遅延を活かして中央システムにデータが即時送信されます。このデータをもとにAIが異常を検出し、適切なメンテナンスを自動提案することで、故障のリスクが大幅に軽減されています。
さらに、デジタルツイン技術による仮想シミュレーションが導入され、製造ラインの最適化や新製品導入時のリスクを事前に回避する仕組みが整っています。これにより、計画外のダウンタイムが削減され、生産効率が飛躍的に向上しています。
また、中国国内での生産拠点同士がIoTネットワークで密接に連携し、需要に応じて生産量を調整することで在庫の最小化を実現。こうした取り組みにより、エネルギーコストや廃棄物を削減し、持続可能な製造を推進しています。
データセキュリティとAIバイアス:IoT製造における課題と対策
IoT技術の普及が進む中、製造業界におけるデータセキュリティの重要性がますます高まっています。各種センサーが収集する機密情報や設備の運用データがネットワーク上で共有されるため、サイバー攻撃によるデータ流出や不正アクセスのリスクが懸念されています。
特に、自動運転車などのシステムが攻撃を受けると、車両の安全性が損なわれる可能性があり、企業は高度な暗号化技術やファイアウォールによる防御を強化しています。また、IoT機器への多層的なアクセス制御を導入し、重要データの保護を徹底しています。
AIバイアスの問題も、IoT製造で克服すべき課題の一つです。AIは大量のデータから学習するため、そのデータが偏っている場合、不適切な意思決定が行われる可能性があります。このため、企業は多様性のあるデータセットを用意し、AIの判断が公平で信頼性の高いものとなるよう、定期的な検証を行っています。
セキュリティとバイアスへの対策は、IoT製造の成功に欠かせません。各企業はこうした課題に取り組むため、ガバナンス体制を強化し、AIの透明性を確保する取り組みを進めています。
持続可能な製造:AIが推進する環境配慮型生産モデル
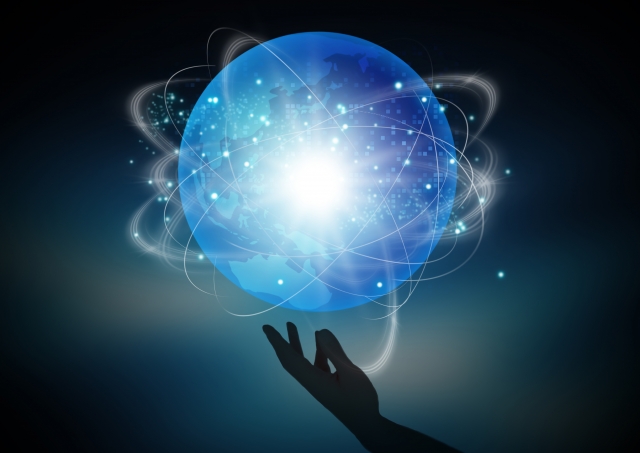
AIとIoT技術の活用により、持続可能な製造の実現が加速しています。工場のエネルギー使用量や廃棄物を最適化するため、IoTセンサーが各機器の消費量をリアルタイムで監視し、AIが効率的なエネルギー配分を提案します。これにより、無駄な消費を抑え、環境負荷が低減されています。
また、リサイクルプロセスにもAIが活用され、廃棄物の分別と再利用が効率化されています。センサーが素材ごとの分別を自動で行い、再利用可能な資源を正確に選別することで、リサイクル率の向上が期待されています。製造プロセスにおけるこうした取り組みは、資源の持続可能な利用に貢献しています。
さらに、AIは生産工程全体のシミュレーションを行い、資源消費を最小化するための最適なプロセスを導き出します。これにより、生産工程の無駄が排除され、効率的な製造が実現しています。廃棄物の削減と同時に、製造工程に必要なエネルギー消費も抑えられています。
環境負荷を軽減するための取り組みは、企業の競争力を強化するだけでなく、社会的責任を果たす上でも重要です。今後、持続可能な製造モデルは、業界全体での標準となることが予想されています。
2025年以降のビジネス展望:オンデマンド生産への移行と新市場の開拓
製造業の未来は、AIとIoT技術の進化により、従来の大量生産からオンデマンド生産へと移行しています。これにより、顧客一人ひとりのニーズに応じたカスタマイズ製品の提供が可能となり、製造業者は需要の変動に柔軟に対応することが求められています。各企業は、生産プロセス全体をデジタル化し、リアルタイムのデータ分析を活用することで、供給チェーンの最適化を進めています。
5Gの普及により、工場内のIoTデバイスが即時に連携し、生産計画がその場で調整されます。これにより、工場では最小限の在庫で効率的な生産を実現し、無駄なコストを抑えることができます。特にトヨタやBMWといったグローバル企業は、需要に応じた生産モデルを強化し、各地域の顧客ニーズに即応することで競争力を維持しています。
新市場の開拓にも注目が集まっています。製造業者は、IoTプラットフォームを活用し、新たなサービスモデルを構築しています。たとえば、製品の使用データを収集・解析することで、製品の改善だけでなく、サブスクリプション型のメンテナンスサービスを展開する企業も増えています。これにより、顧客との接点を増やし、長期的な関係構築が可能になります。
また、AIが顧客データを分析し、個々のニーズに応じた製品提案やプロモーション戦略を自動生成するケースも増加しています。これにより、製品の販売プロセスが効率化されるだけでなく、企業は市場のトレンドを迅速に把握し、新たな商機を捉えることが可能となります。
オンデマンド生産とサービス拡張の組み合わせにより、製造業のビジネスモデルは大きく進化しています。企業は製品の販売だけでなく、サービスを通じた収益拡大を目指す新たなフェーズに突入しています。