製造業が大きな変革を迎える2025年。AIとIIoT(産業用インターネット)が牽引するスマートファクトリーは、従来の工場運営の概念を根本から覆します。トヨタ自動車はAIを活用し、各生産ラインの稼働状況を最適化する「リアルタイム生産管理」を確立。一方、パナソニックは工場見える化の実現で、ダウンタイムを劇的に減少させています。
サプライチェーンの柔軟化と品質向上を同時に実現するスマートファクトリーは、今後の競争力を左右する決定的な要素です。
パンデミック後の新しい製造業の常識として、AIとIoTの活用は欠かせません。本記事では、最新事例や製品の導入プロセスを紹介しながら、2025年の製造業がどう進化するのかを紐解きます。
AIとIIoTの融合が実現するスマートファクトリーの基本とは?
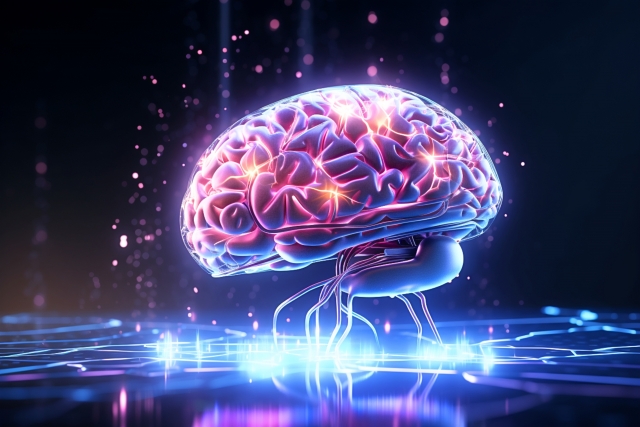
AI(人工知能)とIIoT(産業用インターネット)の融合は、スマートファクトリーの中核を担う技術です。従来、工場では人間が状況を判断し対応していましたが、AIは大量のデータを高速で分析し、即時に最適な生産計画を導き出します。IIoTは各機器にセンサーを搭載し、リアルタイムで稼働状況や温度、振動などの情報をクラウドに送信します。これにより、異常を即座に検出し、予兆保全が可能になります。
トヨタの工場では、AIとIIoTを活用した「カスタマイズ生産」の導入が進んでいます。これは需要の変動に合わせて生産ラインを素早く切り替えるシステムで、少量多品種のニーズに応じた効率的な生産を実現します。
また、パナソニックは「スマートメンテナンスシステム」を開発し、IIoTセンサーによる異常検知とAIによる最適なメンテナンススケジュールの提案を行っています。これにより、機器の故障を未然に防ぎ、ダウンタイムを大幅に削減しています。
このようにAIとIIoTは、単なる自動化にとどまらず、工場全体の生産性と柔軟性を向上させます。特にAIは、工場運営の予測精度を高め、トラブル発生前に対策を講じる「予兆保全型」のアプローチに大きく寄与しています。IIoTによるデータ収集は、生産設備の健全性を常にモニタリングし、予測保全だけでなく、環境負荷の低減にも役立っています。
トヨタとパナソニックの最新事例に学ぶ導入の成功ポイント
トヨタとパナソニックのスマートファクトリーへの取り組みは、製造業の未来を切り開く事例として注目されています。トヨタは、生産ラインにAIを導入することで、リアルタイムの稼働状況を監視し、需要変動に迅速に対応する「カスタマイズ生産」モデルを推進しています。この仕組みにより、複雑なモデルの多品種生産が可能となり、無駄のない効率的な運営を実現しています。
パナソニックの「スマートメンテナンスシステム」は、IIoTを活用して工場内の各種設備をモニタリングし、異常が予兆段階で検出されると、AIが最適な対応策を提示するシステムです。この結果、従来の事後対応型保守から「予兆保全型」にシフトし、故障によるダウンタイムが大幅に減少しました。
特に、トヨタはサプライチェーン全体の最適化にも注力しており、取引先との連携を強化しながら、必要な部品を適時に供給するシステムを構築しています。
このように、AIとIIoTを活用したスマートファクトリーの導入は、製造業において競争力を高めるための重要な要素となっています。労働力不足や市場の変化に対応するための柔軟な生産体制は、今後ますます求められるでしょう。
デジタルツインとメタバースがもたらす生産現場の革新
デジタルツインは、現実の工場や製品を仮想空間に再現する技術で、IoTセンサーから取得したリアルタイムデータを活用して、物理的な環境を仮想モデルでシミュレートします。これにより、製造現場では稼働状況を正確に把握でき、トラブルの原因を迅速に特定できます。たとえば、日立製作所ではデジタルツインを活用し、生産ラインの最適化と保守スケジュールの効率化を図っています。
さらに、メタバースは仮想空間内で製造プロセスや教育訓練をシミュレートする新しい手段として注目されています。シーメンスはメタバース内での「仮想工場ツアー」を提供し、世界中の顧客が工場の運営をリアルタイムで体験できる仕組みを導入しています。これにより、遠隔地からの生産管理や技術者の育成が可能となり、コスト削減と効率向上が実現しています。
自動車業界でも、BMWは生産拠点全体の運営をデジタルツインで管理し、メタバースを使った新製品開発のシミュレーションを行っています。開発段階で製品の問題点を迅速に発見でき、投入期間を大幅に短縮する効果が出ています。特に、生産設備の改良やプロセスの再設計を仮想空間で行うことで、現場に与える影響を最小限に抑えることが可能です。
ライトアウト・ファクトリー:労働力不足を解消する次世代工場
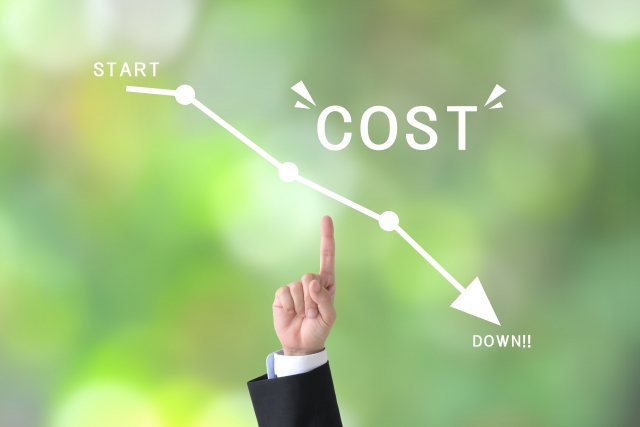
ライトアウト・ファクトリーとは、24時間無人で稼働する完全自動化工場のことを指します。自動化が高度に進んだ生産設備が導入され、AIが生産計画から品質管理までを自律的に行うため、人手をほとんど必要としません。このモデルは、労働力不足が深刻化する日本の製造業にとって大きな解決策とされています。
ファナックは、すでに山梨県にある工場でライトアウト・ファクトリーの運用を開始しています。ロボットが自らのメンテナンスを行い、AIが需要予測を基に生産計画を自動調整する仕組みを取り入れることで、24時間稼働を実現しています。これにより、生産性の向上と運営コストの削減が同時に達成されています。
また、川崎重工業はロボット技術を駆使した完全自動化ラインを構築し、航空機部品の製造においてライトアウト・ファクトリーを導入しています。 これにより、複雑な部品の高精度製造が可能となり、納期短縮と品質向上が実現しました。
ライトアウト・ファクトリーは、AIとロボットの協働による無駄のない運営を目指し、今後の製造業のスタンダードとなる可能性があります。これにより、特に中小企業でも人手不足の影響を軽減し、競争力を維持する手段として普及が進んでいます。
環境負荷軽減への挑戦:CO2見える化と再生可能エネルギーの活用
製造業において環境負荷を減らす取り組みが加速しています。特に、CO2排出量の「見える化」は、持続可能な経営戦略の柱として重要視されています。三菱電機は、工場全体でのエネルギー使用をリアルタイムで監視し、CO2排出量を自動計測するシステムを導入しています。このシステムは、電力使用のピークシフトを促し、再生可能エネルギーの利用を最適化するためのデータを提供します。
パナソニックは、自社工場で太陽光発電を活用し、電力の一部を自給する取り組みを進めています。また、製造過程での廃棄物削減にも力を入れており、循環型社会の実現に貢献しています。さらに、AIを使ったエネルギーマネジメントで効率を高め、二酸化炭素の削減目標を達成しています。
富士通はCO2の見える化を推進するため、IoTを活用したエネルギー管理プラットフォームを展開し、取引先との連携を強化しています。 このプラットフォームは、サプライチェーン全体のCO2排出量を可視化し、削減活動を支援します。環境規制の強化を背景に、各企業はこうしたデジタル技術の活用を通じて、環境対応力の向上を目指しています。
製造業DX展2025から探る、注目のプロダクトと今後の展望
2025年の製造業DX展は、スマートファクトリー関連の最新技術が一堂に集まる場となります。幕張メッセで開催されるこの展示会では、AIやIIoT、デジタルツインを活用した製品が注目の中心となっています。日立製作所は、工場全体の稼働状況を可視化する「スマートプロダクションソリューション」を展示予定です。このシステムは、稼働率や品質をリアルタイムで監視し、生産ラインの最適化を支援します。
また、シーメンスはAIとメタバースを組み合わせた新しい製造プラットフォームを紹介します。このプラットフォームは、遠隔地からでも工場の運営を完全に管理できるもので、パンデミック後の新しい運営モデルとして注目されています。さらに、富士通はAIによる需要予測と生産スケジュールの自動調整を実現するシステムを展示し、企業の効率向上に貢献します。
この展示会には、製造業向けのサイバーセキュリティソリューションも多く登場する予定です。特に、川崎重工業は航空機部品製造の分野でのセキュリティ対策を強化した製品を紹介し、今後の製造業界に必要な新しいセキュリティ標準を提示します。
スマートファクトリーを成功に導く経営戦略とリスク管理のポイント
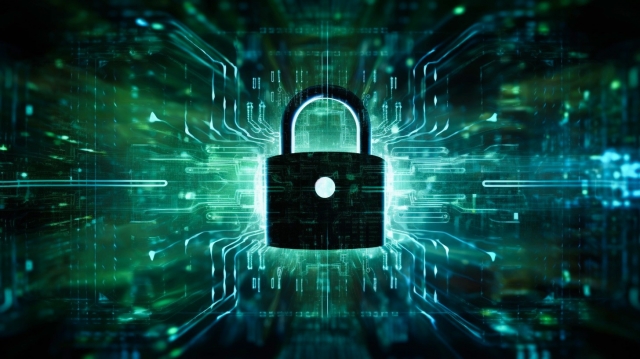
スマートファクトリーの導入にあたって、経営戦略の明確化とリスク管理は不可欠です。トヨタ自動車は、スマートファクトリーを構築する際に、AIとIIoTを活用した「カスタマイズ生産」を中心に据え、製品ごとの多様な需要に応じた生産ラインの柔軟性を確保しました。同時に、各プロジェクト段階でKPI(重要業績評価指標)を設定し、経営目標との整合性を保つことで、確実な成果を追求しています。
一方、パナソニックでは、システム導入の段階からIT部門と現場が連携する「協働型プロジェクトマネジメント」を採用しています。これにより、デジタル技術の導入がスムーズに進み、従業員がシステムを最大限に活用できる環境を整えました。さらに、設備投資の回収期間を短縮するため、AIを使った予測分析を導入し、迅速な意思決定を支援しています。
スマートファクトリー化には、サイバーセキュリティの強化も欠かせません。富士通は、製造業向けの高度なセキュリティ対策として、リアルタイム監視と異常検知機能を備えたシステムを導入しています。これにより、サイバー攻撃による生産ラインの停止を未然に防ぎ、工場の稼働率を維持します。
川崎重工業は、航空機部品の製造で「リスク分散型サプライチェーン」を構築しています。特定地域への依存を避けることで、予期せぬ供給不足のリスクを最小限に抑え、柔軟な生産体制を確保しています。また、IIoTによるデータのリアルタイム共有を通じて、取引先との連携を強化し、リスク管理を徹底しています。